Les combustibles solides de récupération (CSR), une valorisation matière et énergétique dans le process de cuisson du clinker
Les cimentiers mettent en œuvre plusieurs leviers pour réduire leur empreinte carbone. Plusieurs axes d’amélioration sont couramment déployés, dont le remplacement progressif des combustibles fossiles par des combustibles de substitution. Parmi ces combustibles alternatifs, les combustibles solides de récupération (ou CSR).
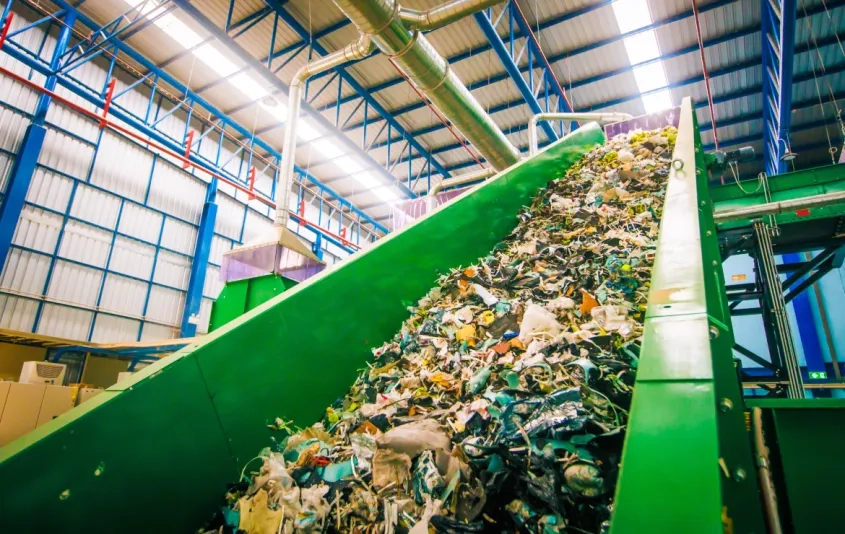
Ils occupent une place de tout premier rang. Issus du traitement industriel de déchets solides non valorisés, les CSR sont doublement valorisés en cimenterie : non seulement ils produisent la chaleur nécessaire à la fabrication du ciment, mais les cendres issues de leur combustion sont directement intégrées dans la composition du clinker. Explications.
Lors de son passage dans le four de la cimenterie, le cru, mélange de calcaire et d’argile, (sous forme solide ou liquide selon les procédés) est progressivement chauffé jusqu’à une température de 1450°C sous une flamme à 2000°C afin de permettre sa transformation en clinker. Cette flamme de cuisson est produite par une tuyère, à l’intérieur de laquelle sont injectés différents types de combustibles :
- Combustibles d’origine fossile, comme le charbon, le coke de pétrole, le fioul lourd ou le gaz naturel.
- Combustibles de substitution, comme les déchets liquides (solvants usagés, huiles...), les pneus usagés non réutilisables, les farines animales, et les combustibles solides de récupération (CSR).
Les CSR contiennent entre 25 et 45% de biomasse, et suivent une logique de circuit court
Mais que sont les CSR ? Se présentant sous la forme de confettis, ces combustibles, aux caractéristiques standardisées par un cahier des charges en entrée de cimenterie, sont issus d’une transformation industrielle - tri, déshydratation, compression - des déchets solides non dangereux en mélange (résidus de bois, plastiques, cartons, papiers...) ne pouvant pas être valorisés par les installations de traitement des déchets (ce sont des refus de tri). Ils sont constitués d’une part non négligeable de biomasse. Disponibles localement, ils bénéficient de schémas d’approvisionnement en « circuits courts » compatibles avec les principes de l’économie circulaire.
Une valorisation énergétique doublée d’une valorisation « matière »
Si d’autres installations, comme les chaufferies biomasse ou les centrales de production d’électricité, utilisent également les CSR comme combustibles alternatifs, les cimenteries constituent leur exutoire le plus performant. Dans une cimenterie, les CSR subissent en effet une double valorisation :
- Une valorisation énergétique : leur combustion alimente la flamme de la tuyère pour produire de la chaleur. Disposant d’un bon pouvoir calorifique (entre 12 et 15 MJ/kg), ils émettent également moins de gaz à effet de serre que les combustibles fossiles, la combustion de la part de leur biomasse étant considérée comme neutre en termes de bilan carbone.
- Une valorisation « matière » : les cendres issues de leur combustion sont intégrées dans la composition du clinker. Les composants de ces cendres - silice, alumine, fer, chaux – sont en effet les mêmes que ceux du clinker. Le process ne génère donc pas de déchet ultime.
Une prévision de consommation des CSR en cimenteries triplée d’ici 2025
Alors que les combustibles fossiles sont progressivement remplacés par les combustibles de substitution - leur proportion dans le mix énergétique devrait atteindre 80% en 2030, contre 43% en 2019 – l’utilisation de CSR par l’industrie cimentière devrait connaître une croissance importante dans les années à venir. Les cimentiers visent ainsi une consommation de 1 million de tonnes par an d’ici à 2025, contre 300 000 tonnes en 2019.
...une bonne nouvelle pour la planète, qui nécessite des investissements importants
Pour l’industrie cimentière, cette augmentation massive de recours aux CSR passera par des investissements importants. Le recours aux CSR nécessite en effet d’adapter la logistique d’approvisionnement des cimenteries ainsi que, dans certains cas les installations existantes :
- Côté logistique, il faut créer une installation dédiée pour recevoir les CSR, les stocker puis les acheminer jusqu’aux tuyères (principale voire secondaire si existante. Afin d’assurer une alimentation continue des tuyères en CSR, un stock de plusieurs jours est généralement constitué
- Au-delà d’un certain volume de CSR consommé, les tuyères en place doivent être modifiées, voire remplacées par des tuyères adaptées à des volumes de combustibles solides plus conséquents
- Des ateliers dédiés de séchage et préparation de CSR peuvent aussi être créés afin de garantir la qualité requise au sein de la cimenterie
COMMENTAIRES
LAISSER UN COMMENTAIRE