Mise en œuvre des bétons projetés
Préparation du support
La préparation du support est importante notamment pour favoriser l’adhérence du béton projeté et dépend du type de travaux à réaliser. Elle consiste à purger les éléments non adhérants au support, nettoyer et humidifier à refus le support, et, le cas échéant, dégager les armatures en place. La projection de béton par voie sèche, du fait des fluides sous pression, est moins adaptée aux supports fragiles et friables. Pour ces supports, on privilégiera la projection par voie mouillée ou on prendra des précautions particulières pour le démarrage de la couche.
Quelle que soit la technique de projection, il est nécessaire d’humidifier le support (aspect mat, mais pas ruisselant) avant projection afin d’éviter un gradient hydrique au sein de la couche de béton projeté, ce qui entraînerait inévitablement sa fissuration.
A contrario, les venues d’eau à travers le support doivent être colmatées afin d’éviter le délavage et les chutes du béton fraîchement projeté.
Réalisation de la couche de béton projeté selon la technique de projection
Le mode de confection de la couche de béton projeté diffère d’une technique de projection à l’autre. Dans le cas de la projection par voie mouillée, cela s’apparente à des « masselottes » de béton qui se collent les unes aux autres sur le support pour former une couche de béton.
Dans le cas de la projection par voie sèche, l’air comprimé sert à véhiculer les granulats enrobés de matrice cimentaire. En début de projection, les granulats rebondissent sur le support après avoir plaqué la matrice cimentaire contre celui-ci, formant ainsi un « matelas » de pâte sur le support. Ensuite, ce matelas accueille les granulats qui continuent d’affluer, formant ainsi la couche de béton. Tout au long de la projection, le martèlement des granulats compacte le béton.
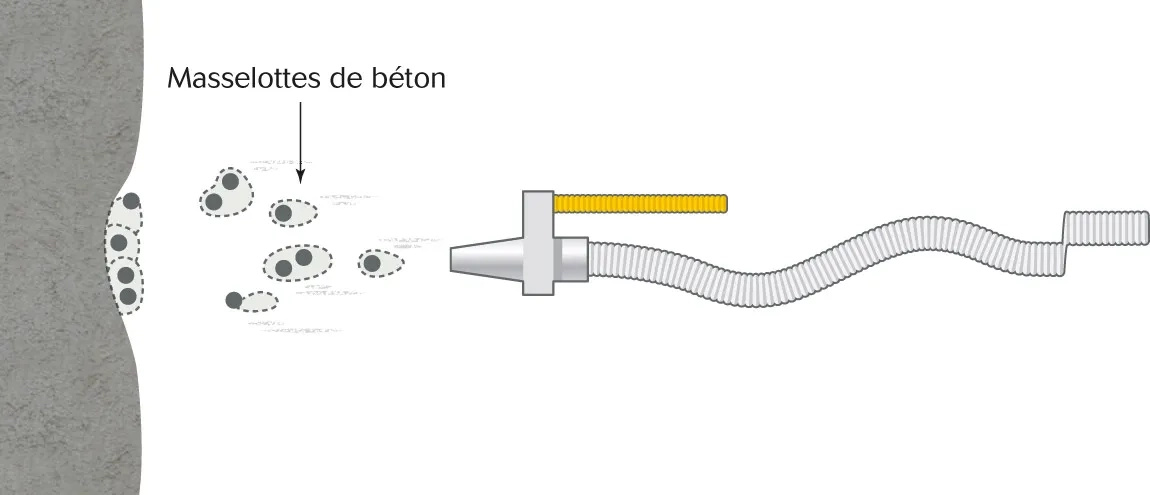
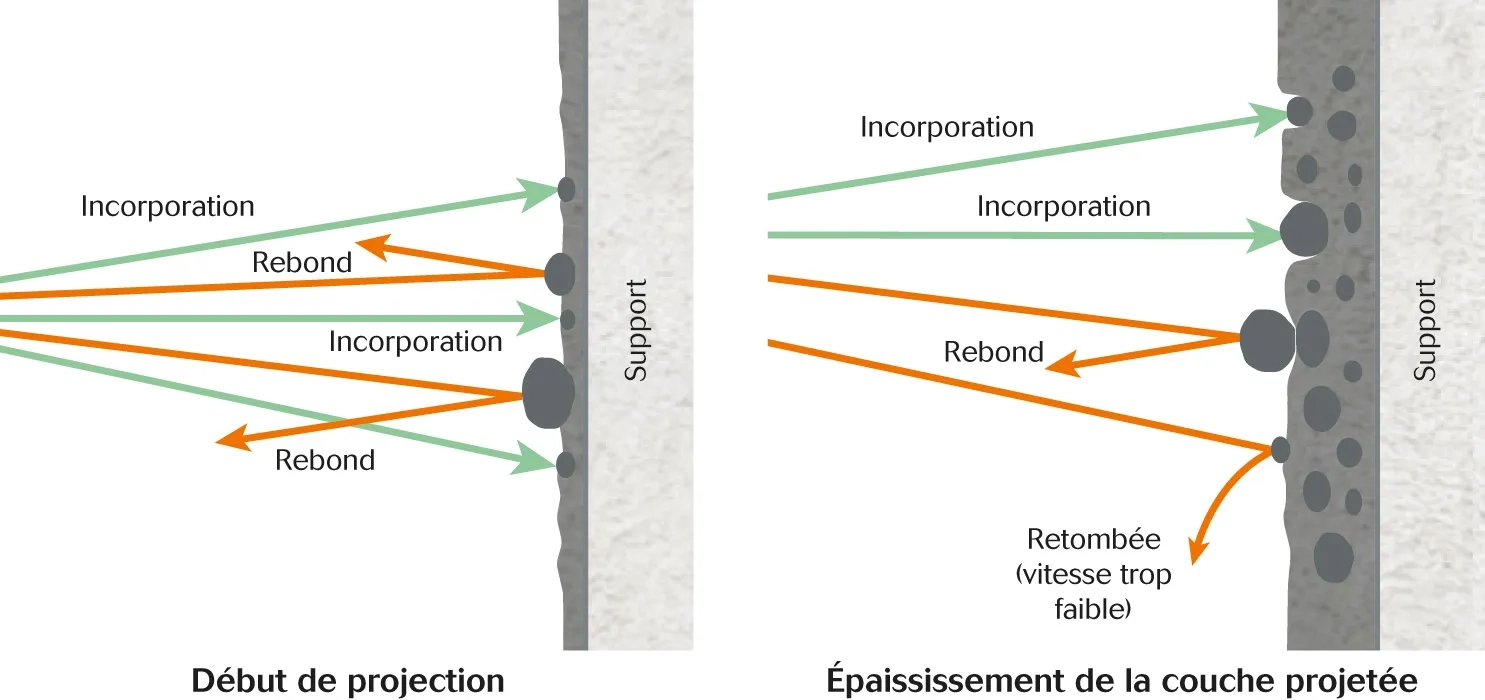
Pertes de béton et nettoyage du chantier
En béton projeté par voie sèche, on parle non pas de réduction des pertes mais d’optimisation. En effet, le process de réalisation de la couche de béton projeté par voie sèche s’appuie justement sur les granulats qui vont frapper la couche déjà en place. Ils vont la compacter, rebondir et tomber au sol, soit parce qu’il n’y a pas assez de matière déjà en place pour qu’ils s’incrustent dans la couche de béton, soit parce qu’ils frappent un autre gravillon.
S’ajoutent à ces granulats et augmentent les pertes, les matériaux qui n’ont pas assez d’énergie pour arriver jusqu’au support ou s’y incruster. Les pertes sont essentiellement constituées de granulats, ce qui génère un enrichissement en ciment, surtout dans les premiers millimètres de la couche de béton projeté. On comprend donc qu’une réduction trop importante des pertes en projection par voie sèche ne saurait être un gage de qualité.
Plusieurs facteurs influent sur la quantité de pertes :
- La formulation (matelas de pâte cimentaire),
- les granulats (nature et forme),
- le sable (quantité de fines),
- les réglages de projection (débit d’air et pression, distance lance-paroi, orientation de la projection),
- les contraintes du chantier (support, armatures, épaisseur des couches de béton projeté, position du support) et, de manière prépondérante, l’expérience de l’opérateur de projection.
La production de pertes (rebonds et retombées) impose un poste de nettoyage du chantier plus efficient que pour les chantiers de bétonnage traditionnel.
Dans le cas de la projection par voie sèche, ces pertes (majoritairement des rebonds) sont quasi dénuées de pâte de ciment et donc assimilables en fin de journée à un stock de granulats assez aisément évacuable voire valorisable. En revanche, en voie mouillée, ces pertes sont des petites « masselottes » de béton qui font prise et s’agglomèrent. Il est donc important de les évacuer à l’avancement. Leur gestion est une sujétion supplémentaire.
La quantité de pertes doit également être prise en compte pour ne pas excéder la capacité portante des échafaudages. Les pertes doivent être régulièrement évacuées de ces équipements (a minima à chaque changement de poste).
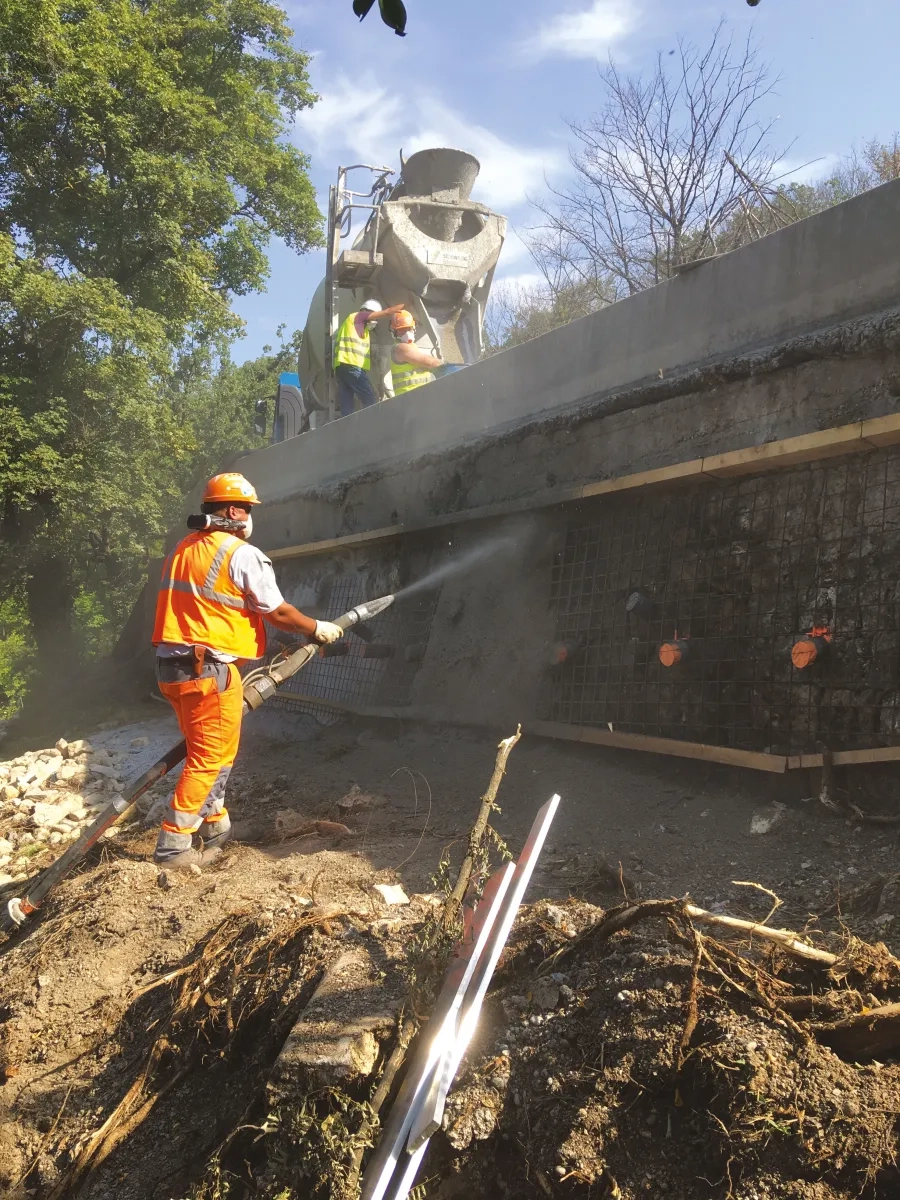
Conseils et bonnes pratiques pour des bétons projetés de qualité
Il est primordial que le béton projeté soit maîtrisé tant au niveau de l’opérateur (reconnaissance d’un travail bien exécuté) que de l’encadrement (choix des matériels, des matériaux, estimation des pertes et du rendement) et de la maîtrise d’œuvre et de la maîtrise d’ouvrage afin de minimiser les risques sur chantier.
Il est nécessaire, avant tout, de déterminer les besoins et de spécifier les exigences dans les pièces techniques des marchés :
- projection d’un béton défini et validé ;
- respect des épaisseurs ;
- obtention de l’adhérence à l’interface (entre le béton fraîchement projeté et le support et entre deux couches de béton le cas échéant) ;
- respect des performances mécaniques ;
- réduction des émissions de poussière ;
- respect des rendements du chantier (en tenant compte du volume des pertes) ;
- protection des opérateurs (protections individuelles notamment) et de l’ensemble des personnels en coactivité (à limiter).
Afin de répondre à l’ensemble de ces exigences, il est vivement recommandé que le choix du matériel et des matériaux soit défini par un encadrant de chantier compétent en projection.
Avant le début de la projection, tous les équipements disponibles doivent être contrôlés, leur état de fonctionnement doit être vérifié et la compatibilité des matériels les uns avec les autres doit être validée (à titre d’exemple, le branchement du groupe électrogène avec la machine à projeter afin qu’elle tourne dans le bon sens, le type de lance afin d’éviter les bouchons ou les coups de canon, la vérification de la pression de bridage du compresseur…).
En cours de projection, l’opérateur doit effectuer des réglages d’air et d’eau, adapter la distance lance-paroi en fonction du type de béton. Il doit obtenir l’épaisseur à réaliser, le bon compactage du béton, l’enrobage des éventuelles armatures et la résistance du béton escomptée, tout en limitant l’émission de poussière.
Il est indispensable que les opérateurs fassent leur réglage en fonction des besoins :
- pour la voie mouillée (VM), régler l’air à bon escient (trop d’air génère beaucoup plus de poussière et allonge la distance lance-paroi, générant plus de pertes par retombées) ;
- pour la voie sèche (VS), régler l’eau (l’excès d’eau implique une moins bonne compacité, une chute de résistance et parfois des chutes de béton ; le manque d’eau génère beaucoup de poussière et une augmentation considérable des pertes) ;
- pour la machine, régler le débit de béton (un flux trop important de béton va nécessiter des déplacements plus rapides des opérateurs et une émission de poussière plus importante ; un trop faible débit de béton va impliquer des discontinuités de flux et un rapport E/C très hétérogène) ;
- dans les deux cas (VM ou VS), régler la distance lance-paroi (une distance trop importante implique une augmentation des pertes et des vides mais permet une meilleure maîtrise de l’épaisseur et de la planéité ; une distance trop faible rendra difficile la maîtrise de l’épaisseur et de la planéité mais permettra une réduction des pertes).
Par ailleurs, la projection se fera toujours par une action circulaire au niveau de la lance afin d’homogénéiser le mélange sur le support et de maîtriser l’épaisseur.
Le choix du matériel est primordial et est la base d’une projection de qualité, d’où l’importance d’avoir sur un chantier un ou des opérateurs formés, certifiés et expérimentés.

COMMENTAIRES
LAISSER UN COMMENTAIRE