Galet de béton pour la station de pompage
Du béton projeté pour façonner un galet : focus sur une prouesse dans la recherche et une haute technicité dans la conception et la réalisation.
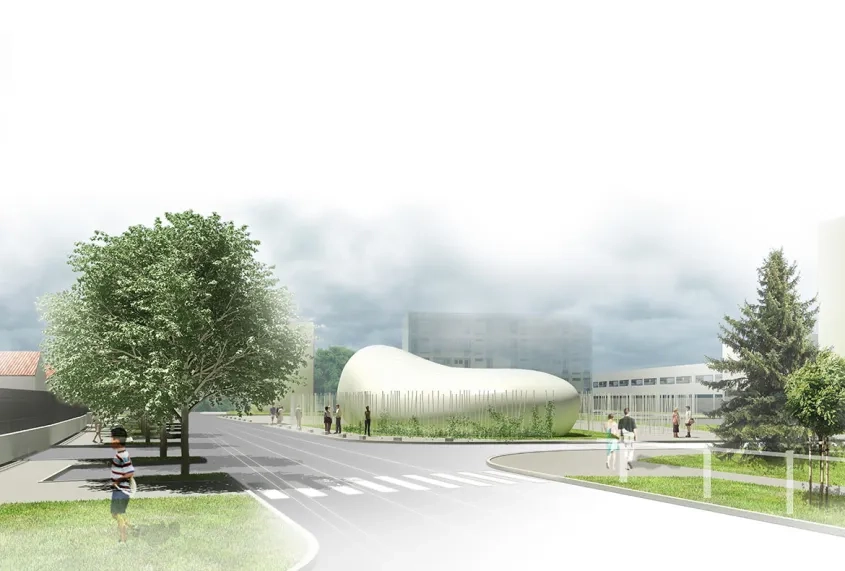
Avec ce galet blanc posé en pied d’immeubles, l’architecte Monique Labbé explore toutes les possibilités et repousse les limites qu’offre le béton.
La nouvelle station de pompage de Massy-Antony, en travaux depuis 2015, se substituera à quatre réservoirs aériens, culminant à près de 50 m.
La demande du SEDIF (Syndicat des Eaux d’île-de-France), le maître d’ouvrage, était de moderniser le réseau, le sécuriser, tout en intégrant davantage le bâtiment dans l’environnement très urbain de Massy. « Le choix de cet objet a fait consensus. Les élus, experts et membres du conseil d’administration ont été subjugués par la forme que nous proposaient Monique Labbé et Egis », explique Isabelle Radlak, responsable du service Ouvrages du SEDIF. « Pour nous, même si nous avions une totale confiance dans le projet de l’équipe choisie, notamment imaginé par l’architecte, la question de la faisabilité de la forme ne se posait pas, mais c’était plutôt comment la réaliser. »
Mais l’équipe de maîtrise d’œuvre a su rassurer et « ce galet, lisse et comme recouvert d’une peau, d’une grande pureté », que souhaitait Monique Labbé, est bien sorti de terre. Entre les anciens fûts aériens d’une cinquantaine de mètres de haut, et datant de la fin des années 60, et l’ovoïde blanc qui se déploie aujourd’hui, le contraste est donc total. De plus, les performances attendues, une capacité moyenne de 4 700 m3/jour dont un pompage d’eau maximal de 1 100 m3/h, imposaient des dimensionnements conséquents. Pour répondre à ces objectifs, tout en intégrant au maximum le projet, l’équipe de maîtrise d’œuvre a privilégié un bâtiment en deux zones distinctes, l’aérienne et la souterraine.
Un objet très complexe
En effet, il ne faut pas se fier au visible : la forme courbe, convexe et concave, mais aussi en larges débords, cache en fait une importante usine de surpression souterraine, située dans les entrailles de la bulle de béton. S’enfonçant à plus de 7 m, la salle des machines se présente comme une sorte de cuve oblongue de 23 m sur 13 m environ. Le site se trouvant à proximité de la nappe phréatique, la première étape a été l’étanchéification du périmètre de la cuve, à l’aide de palplanches. Ces palplanches ont par la suite servi de coffrage négatif pour le coulage des voiles béton (classe de résistance C30/37) d’une épaisseur de 50 cm. Le coffrage de la surface intérieure des voiles a été assuré par des panneaux de 7 m de hauteur. L’ensemble de cette opération était délicat et technique, notamment en raison des conditions particulières du site : un milieu urbain habité en bordure immédiate d’une avenue très passante, sur une zone spatialement très contrainte, avec très peu d’aire de stockage pour le matériel et les intervenants.
Pour maintenir l’ensemble des voiles béton, plusieurs poutres-butons en béton (classe de résistance C25/30) de dimensions importantes ont été mises en place : la salle des machines étant avant tout un local technique, certaines poutres servent de support au matériel de levage pour les éléments des pompes, dont certains pèsent plusieurs centaines de kilos. Les parois ont aussi une fonction structurelle pour le galet : elles reprennent en partie les charges des prémurs de la structure aérienne, et les forces contraires dues aux porte-à-faux relativement importants. Le visible et l’invisible sont donc intimement liés.
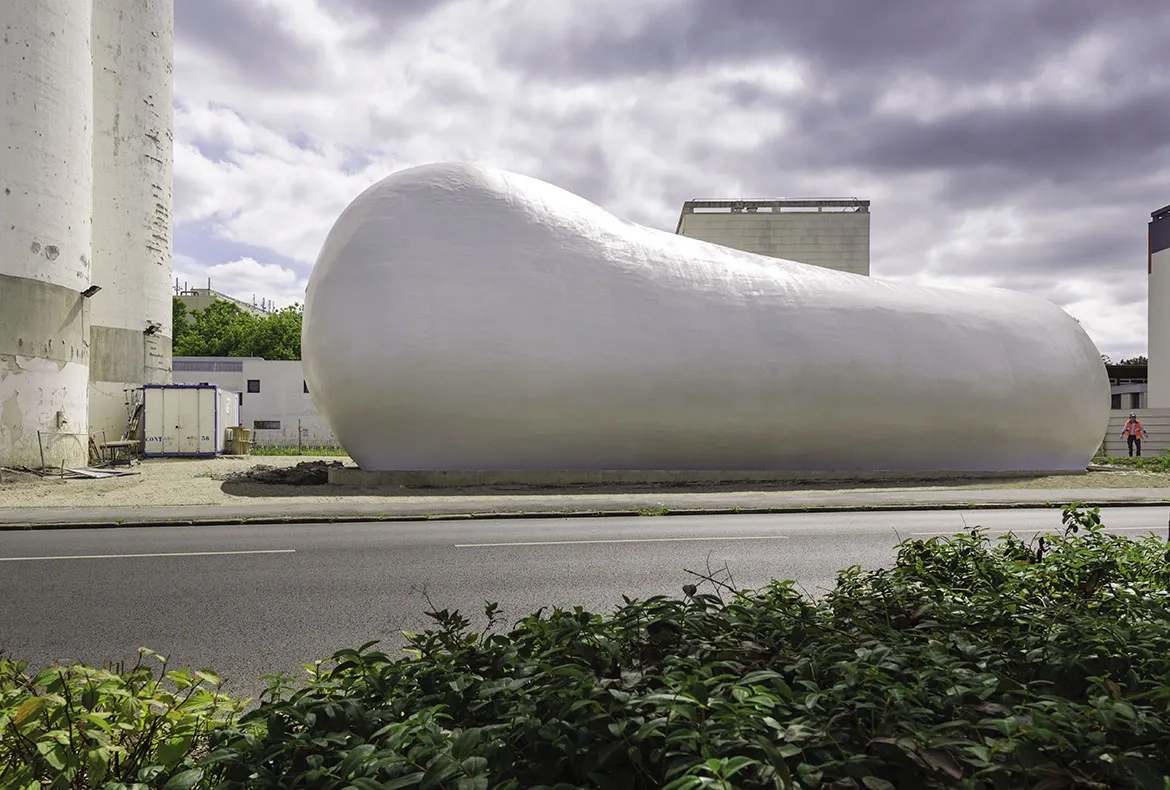
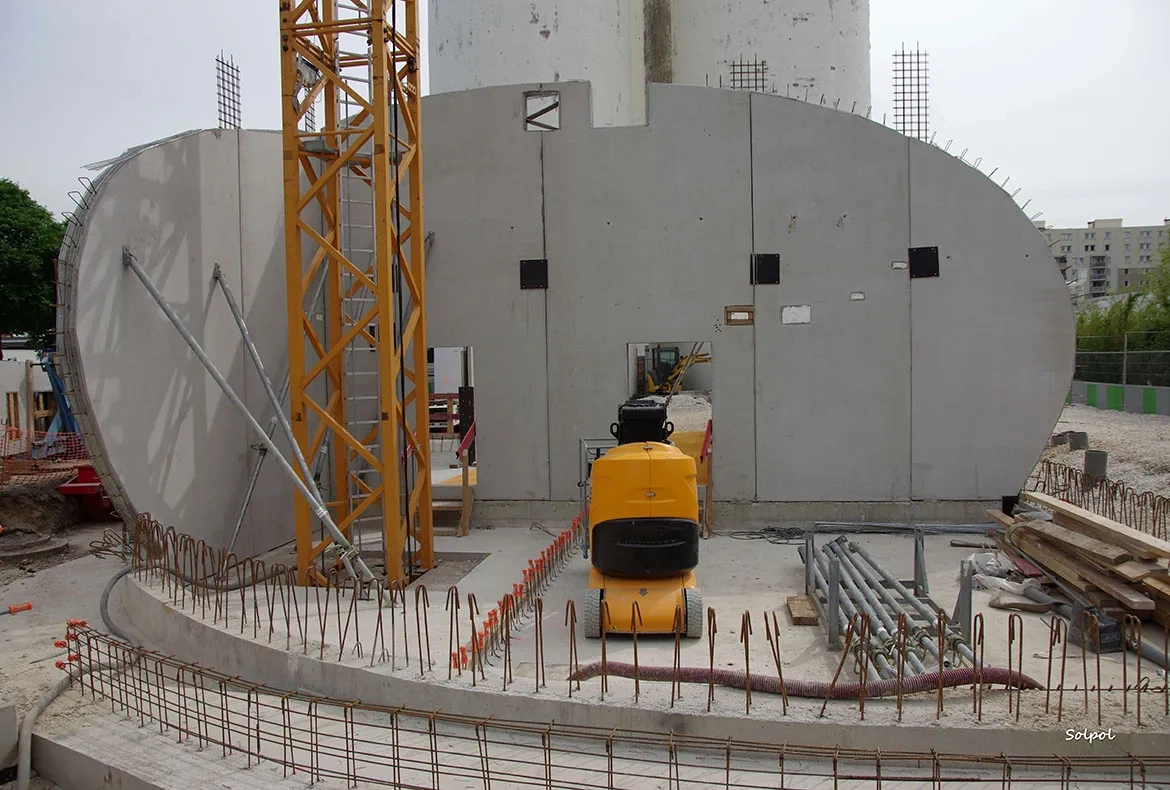
Le galet, summum de précision et de calcul
« La complexité de l’ouvrage vient de sa forme absolument unique, non symétrique, non sphérique, dans laquelle chaque point est particulier », commente Dany El Sibaï, directeur des travaux chez Sogea île-de-France Génie Civil. La méthode choisie pour réaliser une forme aussi inédite s’est portée, après de nombreuses discussions des concepteurs et bureaux d’études, sur une coque en béton projeté double face. La coque devant bien sûr reproduire au millimètre l’objet dessiné par l’architecte.
La forme de galet, d’une superficie de 600 m2 environ, a été esquissée puis modélisée à l’aide de logiciels 3D, avec surtout le calcul dans l’espace (X, Y, Z) d’un très grand nombre de points de la coque. C’est cette maquette numérique 3D qui a permis ensuite de calculer chaque point d’assise de la structure, toutes les données étant exploitées selon une démarche BIM, afin de servir de base à chaque étape de la conception pour l’ensemble des intervenants du chantier.
Pour supporter une telle structure, une dizaine de prémurs en partie arrondis, ou en forme de demi-lunes et mesurant jusqu’à 8 m de hauteur, pour 2 à 8 m de longueur, ont été spécialement fabriqués par l’entreprise KP1. Un véritable challenge pour le bureau d’études (Ingérop), le préfabricant, mais surtout pour les équipes chargées de leur mise en œuvre : les assises de certaines de ces pièces en béton étant les parties les plus étroites des prémurs. D’où « une instabilité au moment du grutage, mais surtout lors des positionnements sur le site », précise encore le directeur de travaux.
360 points à régler, en X, Y, Z
Une fois les différents prémurs implantés sur la dalle de couverture, la réalisation de la coque proprement dite a débuté... Mais « comment créer un coffrage pour réaliser une telle forme inhabituelle ? C’était vraiment notre interrogation », se souvient Isabelle Radlak, du SEDIF. « Les études de conception ont d’ailleurs été assez longues, tout était à inventer, ou presque. »
Étape préliminaire au coffrage, un étaiement très particulier a été spécialement mis au point. Il est constitué d’une centaine de poteaux d’étaiement, réglables en hauteur et terminés par une fourche. Chacune de ces fourches, mobile et réglable, a alors été précisément positionnée selon les coordonnées X, Y, Z, fournies par la modélisation 3D. Un travail d’orfèvre, qui a nécessité de nombreuses journées d’intervention. Une fois cette forêt de poteaux mise en place, y compris sur les côtés à cause des nombreux débords de la future coque, la mise en œuvre des armatures a pu débuter. « C’est le ferraillage qui fait la forme du bâtiment », souligne Dany El Sibaï. Pour compliquer l’opération, deux nappes d’armatures ont été réalisées, séparées par un écarteur d’une dizaine de centimètres.
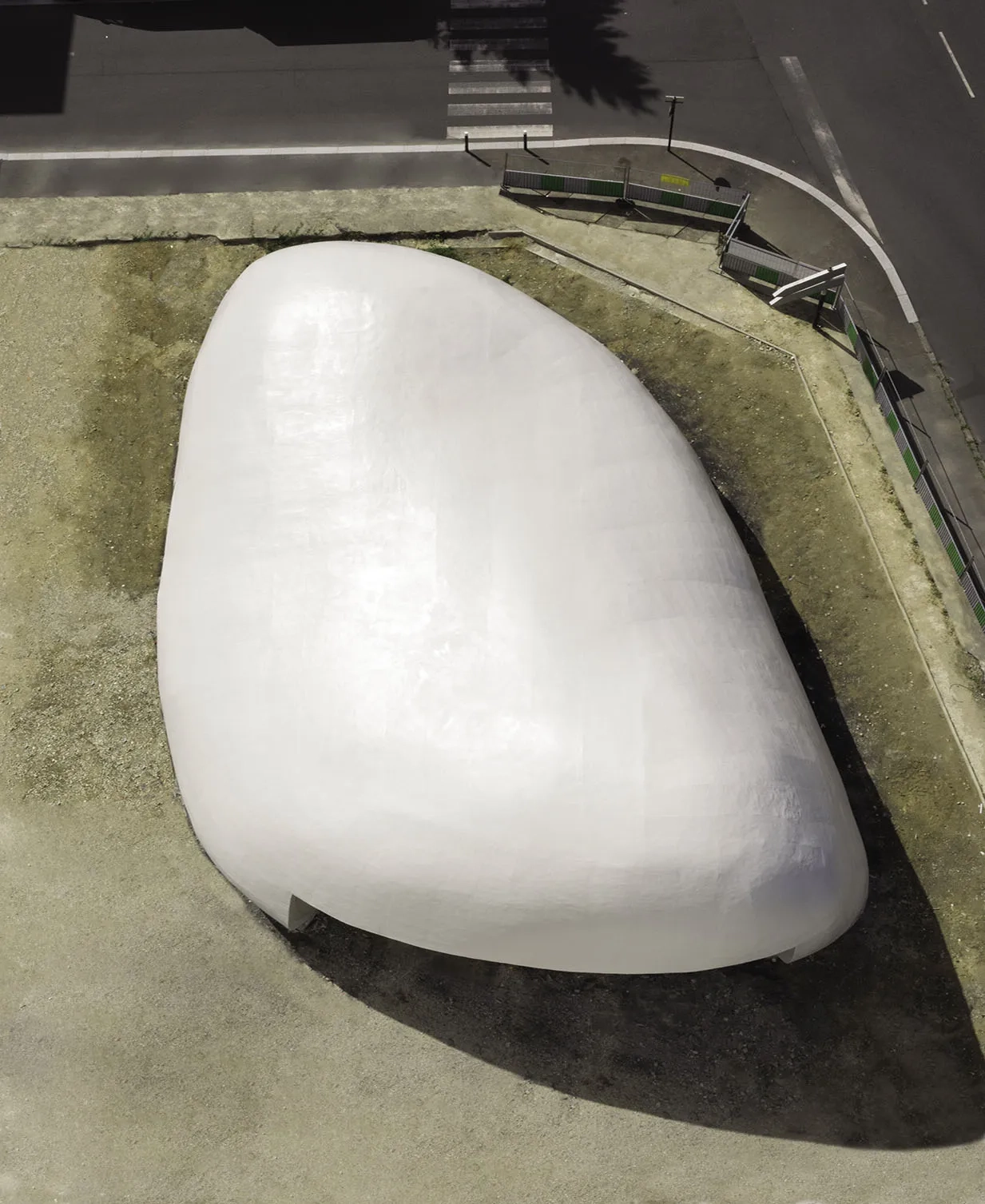
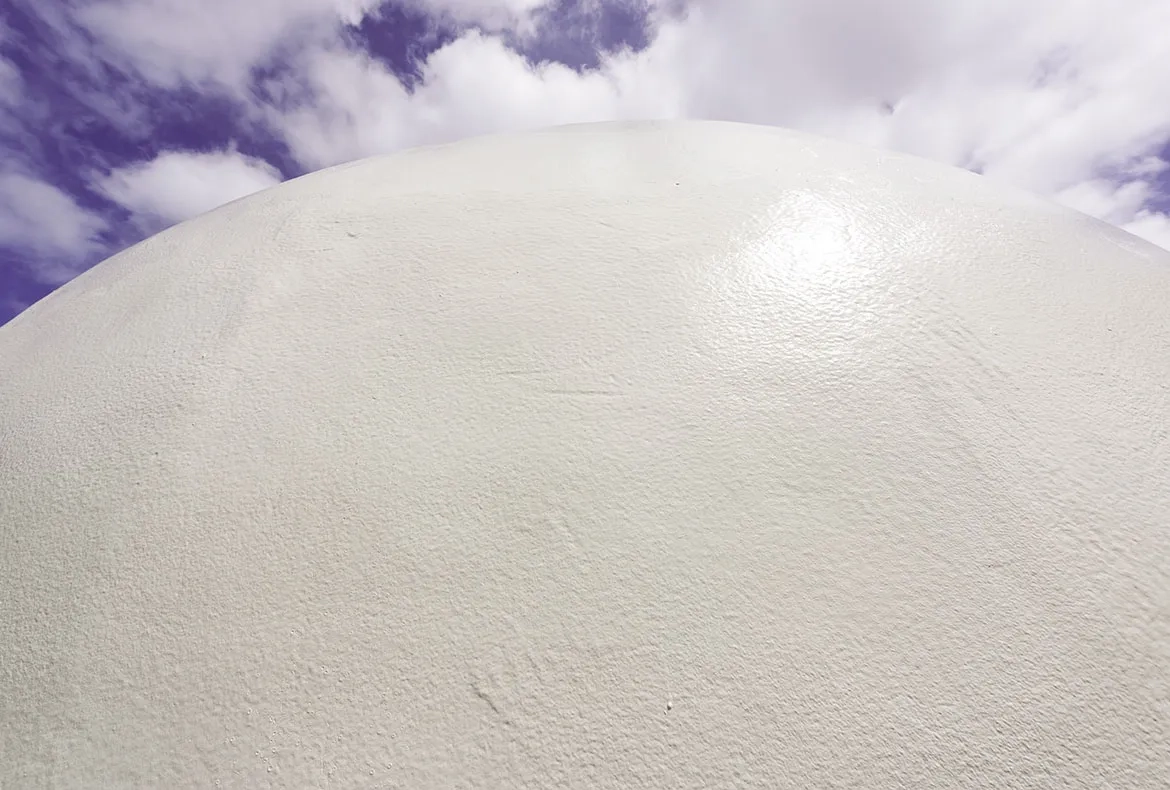
Une coque en béton projeté
La coque en béton armé, de 20 cm d’épaisseur, est donc constituée d’un « mille-feuille » : les deux nappes d’armatures, un lattis (sorte de filet très fin) métallique. Le lattis est fixé sur la nappe d’armatures, son rôle étant de maintenir le béton projeté. Sa souplesse lui permet d’épouser au mieux la forme particulière de la coque.
Le béton projeté a été mis en œuvre en trois phases pour le toit :
- une projection de béton par voie sèche, réalisée depuis l’intérieur de la coque sur une épaisseur de 13 cm, afin de remplir l’espace entre les deux nappes d’armatures
- puis une projection par voie sèche d’une couche de finition de 3 cm par-dessous, de l’intérieur, afin d’enrober le treillis inférieur, suivie d’une finition à la règle.
- La troisième phase de la projection s’est déroulée depuis l’extérieur, sur le toit de la coque et les façades courbes, avec un béton projeté par voie humide et une finition manuelle à la taloche.
Pour les façades, la méthode employée était relativement similaire, mais la projection de béton par voie sèche sur 12 cm d’épaisseur s’est faite par l’extérieur, suivie d’une projection depuis l’intérieur sur 3 cm ; troisième phase, la projection d’un béton par voie humide depuis l’extérieur, de 4 cm, finie à la taloche.
C’est donc un process très complexe, technique et exigeant une très grande patience de la part des deux équipes de trois personnes (projeteur, aide-projeteur, centraliste et 3 ouvriers qualifiés pour le talochage) déployées tout au long de cette opération extrêmement délicate, « une première », comme le souligne Dany El Sibaï.
Dix semaines ont été nécessaires pour réaliser le béton projeté de la coque, sans compter les 35 jours pour le talochage des deux faces. La partie en sous-coque, accueillant des locaux électriques ou techniques, devait aussi répondre à des règles d’isolation. Ainsi, une sorte de flocage permettant une isolation thermique/acoustique et coupe-feu a été projetée côté intérieur, avant une couche de finition d’enduit, elle aussi projetée et talochée à la main ! Le béton de la coque n’étant pas suffisamment imperméable, il a été recouvert en début d’été, lorsque les températures étaient plus douces, et la météo plus stable, d’une résine d’une épaisseur de 2 mm, projetée au pistolet, avec une peinture de finition blanche.
Le béton se niche dans les détails
Pour ceindre l’espace extérieur qui sera planté d’arbres de hautes tiges et d’arbustes, Monique Labbé a imaginé une fine clôture constituée d’un muret de béton de forme trapézoïdale, très intégré, servant d’assise à un barriérage constitué d’une multitude de barreaux verticaux non symétriques et laissant passer le regard ; cela donnera un peu de verticalité à cet espace si curviligne.
Chiffres clés
Béton projeté : 20 cm d’épaisseur
Coque : 360 points référencés et positionnés
Béton projeté par voie sèche : GUNISEC 40
Béton projeté par voie humide : GUNIDROFIN 301
Fournisseur des bétons : Socli
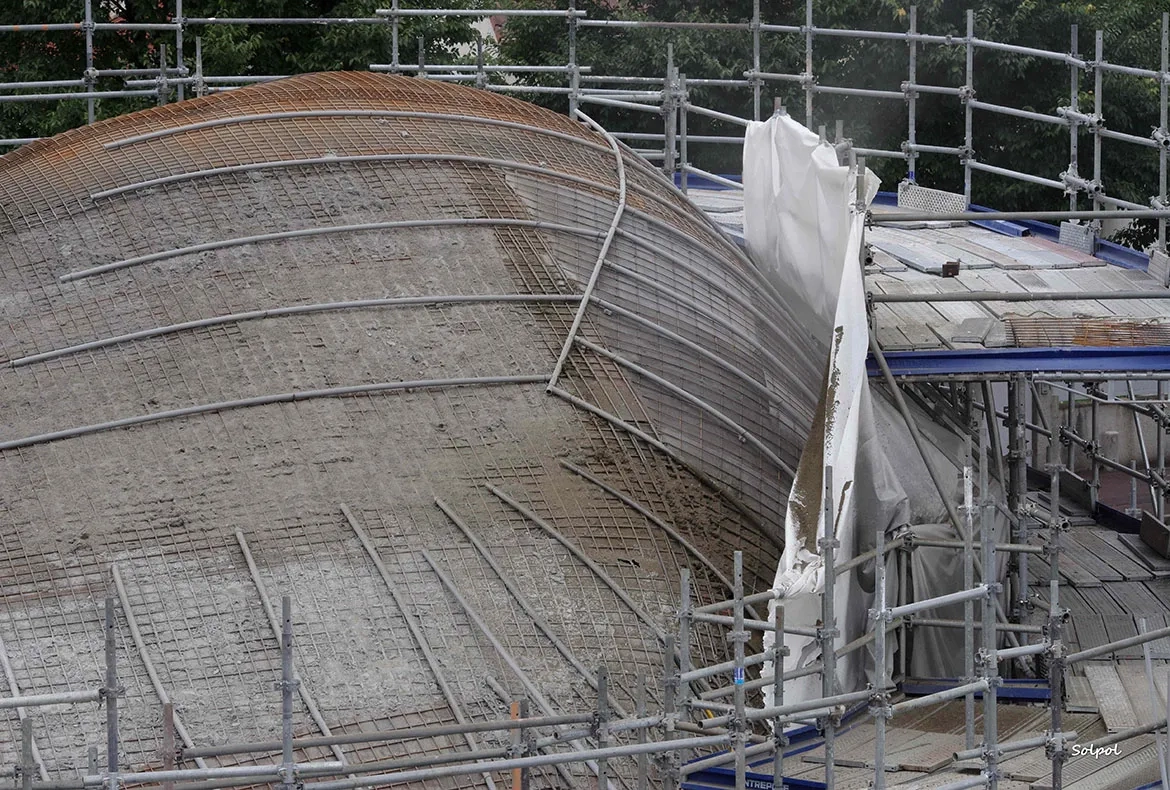
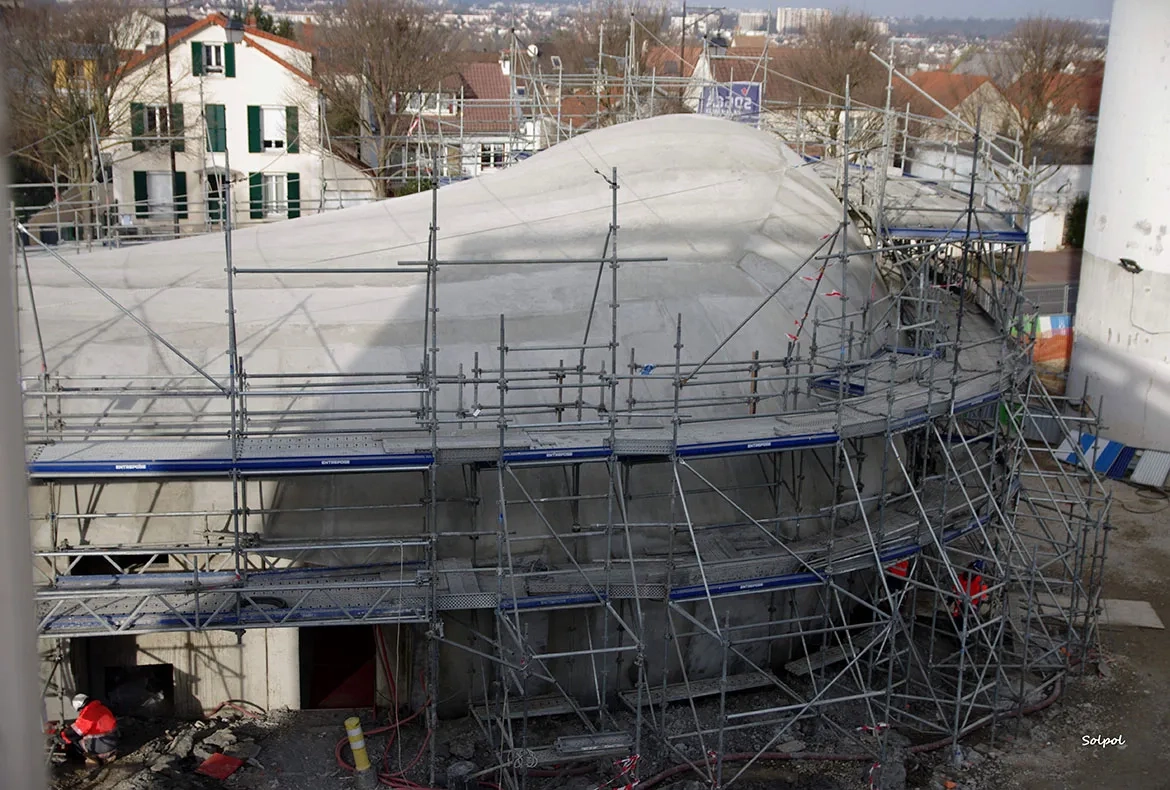
Reportage photos : Les Ateliers Monique Labbé ; Laurent Thion ; Solpol
Maître d’ouvrage : SEDIF – Maître d’œuvre : BPR France ; Safege ; Egis Eau ; Les Ateliers Monique Labbé – Contrôleur technique : Socotec – Coordinateur SPS : Presents –Entreprises : Sogea IDF Génie Civil (mandataire) ; Sogea IDF Hydraulique ; PRS ; Cofely-Ineo ; Dodin IDF – BET : Ingérop – Durée des travaux : 25 mois – Coût : 7,3 M€ HT.
COMMENTAIRES
LAISSER UN COMMENTAIRE