Déviation d’étampes : une couche de forme innovante
Performances techniques, optimisation des structures de chaussées routières, préservation des ressources, réduction des coûts, protection de l’environnement : autant d’avantages qui expliquent l’engouement pour cette nouvelle technique élaborée par l’entreprise Charier et qui consiste à traiter un sol, préalablement renforcé de fibres de chanvre, au liant hydraulique routier (LHR). En voici un nouvel exemple très significatif avec la déviation d’Étampes (Essonne), dernier tronçon du programme de désenclavement du parc Sud Essor à Étampes.
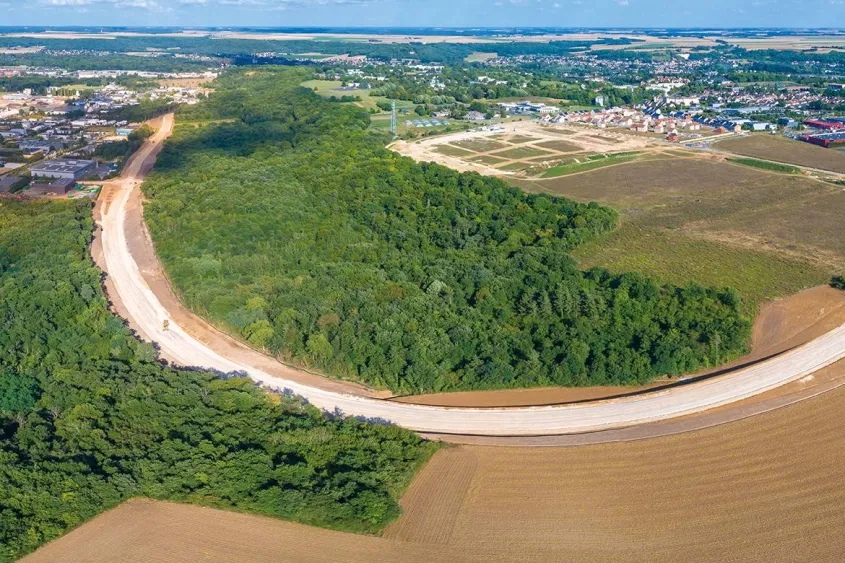
L’opération est innovante à plusieurs titres :
Sur le plan technique
Il s’agit d’une couche de forme traitée avec un liant hydraulique routier et renforcée à la fibre de chanvre. L’innovation, par rapport à une couche de forme traitée classique, réside dans l’utilisation des fibres de chanvre. « L’objectif recherché est, d’une part, de maîtriser la fissuration du sol traité et, d’autre part, d’augmenter les performances mécaniques du matériau traité afin de soulager la structure bitumineuse de la chaussée (couche de fondation, couche de base et couche de surface) et de réduire par conséquent son épaisseur », répète inlassablement Valéry Ferber, directeur Environnement & Innovation de l’entreprise Charier.
Sur le plan technologique
Pour atteindre les objectifs techniques, l’entreprise Charier a développé une machine spécifique, « l'épandeur à fibres », pour disperser et épandre, sur une largeur de 2,50 m, la fibre de chanvre à la surface du matériau à renforcer, et ce d’une façon précise et homogène.
Sur le plan financier
Le chantier est réalisé dans le cadre d’un partenariat public-privé (PPP), au terme d’un dialogue compétitif qui a permis d’affiner le projet, d’élaborer une solution technique, d’optimiser la structure de la chaussée bitumineuse qui sera réalisée au-dessus de la couche de forme et de mettre au point la conception intégrant le procédé Satis. Enfin, la communauté d’agglomération de l’Étampois Sud-Essonne a confié à l’entreprise Charier la conception, la construction, le financement, l’entretien courant et l’entretien structurel pendant vingt ans de cette nouvelle route qui achève la déviation d’Étampes. Elle relie la RD 191 au parc d’activités Sud Essor, en utilisant plusieurs innovations technologiques. Comme le rappelle Bernard Laplace, vice-président de la communauté de communes de l’Étampois Sud-Essonne, « le dialogue a permis de s’orienter vers une solution atypique, mettant en œuvre un procédé et une solution innovants associés à d’autres innovations techniques et en particulier une solution pour la gestion des eaux pluviales, conformément aux recommandations de l’agence de l’eau ».
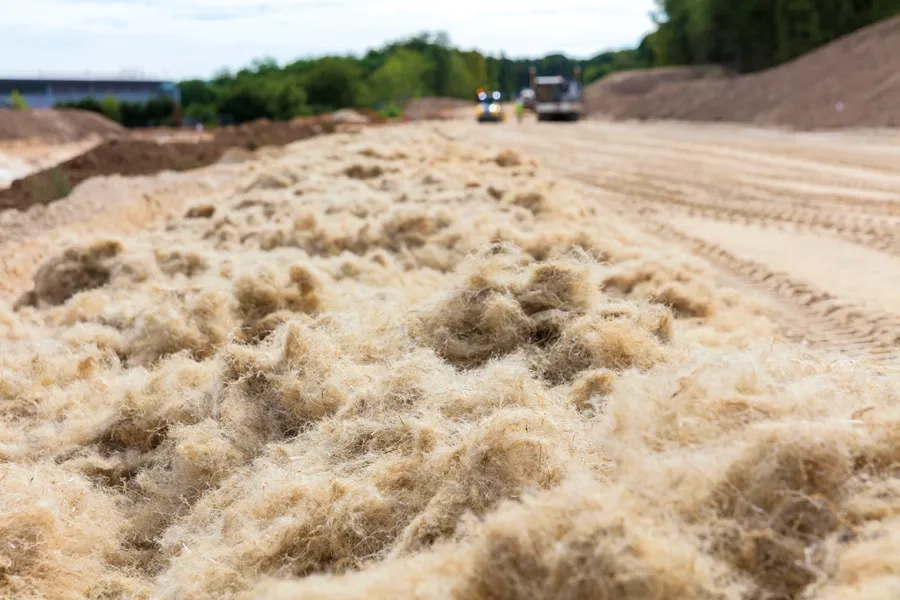
Une idée innovante qui a fait lentement son chemin
L’objectif principal est de réduire l’utilisation des matériaux nobles dans la structure. Cela a conduit à concevoir une couche de forme traitée performante, que l’on puisse intégrer dans le dimensionnement de l’assise de chaussée. Cette couche de forme doit donc présenter une régularité irréprochable en épaisseur et en homogénéité de performance. Les fibres de chanvre apportent une contribution notable à la résistance, puisqu’elles améliorent la résistance en fatigue de 20 %. De plus, elles présentent un double intérêt :
- Ce sont des fibres végétales naturelles.
- Elles sont produites par plusieurs fournisseurs potentiels de manière industrielle pour assurer leur régularité.
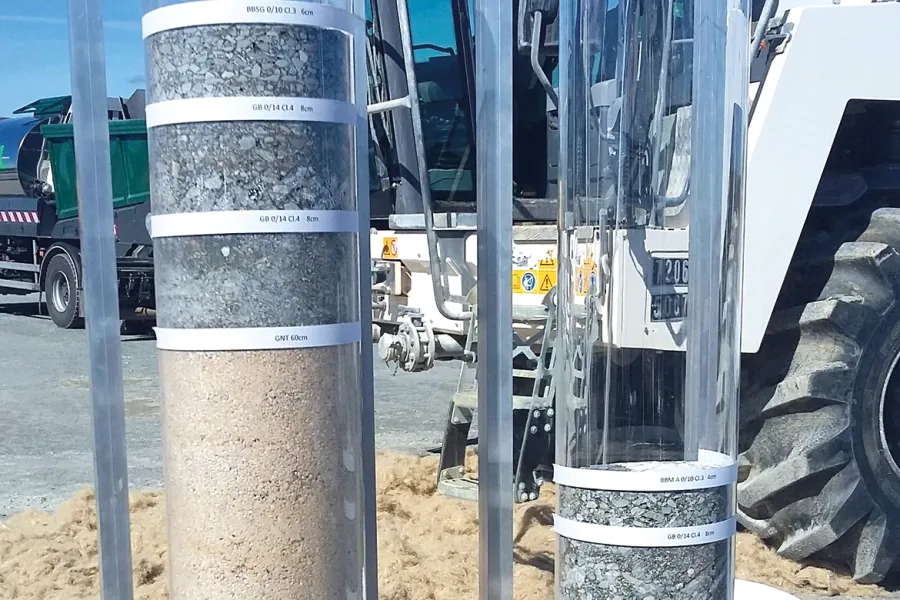
Critère retenu : dosage de la fibre de chanvre permettant l’obtention d’un niveau de seuil de la résistance à la flexion du sol traité.
Objectif : gagner sur le dimensionnement de l’assise de chaussée. Gain escompté : 4 à 6 cm sur l’épaisseur des couches bitumineuses.
La méthodologie a été élaborée après de longues recherches en laboratoire et sur chantier. Le traitement de la couche de forme s'est fait en plusieurs étapes :
- Correction granulométrique du sable par une grave calcaire 0/20.
- Incorporation des fibres de chanvre à un dosage étudié en laboratoire et dépendant de la nature du matériau.
- Traitement avec un liant hydraulique routier (6 %).
Dimensionnement de la structure
Le dimensionnement de la structure a intégré les performances de la couche de forme traitée (liant hydraulique + fibre de chanvre) et a été effectué avec les hypothèses suivantes :
- Trafic estimé à la mise en service : 9 000 Véh dont 650 PL/j.
- Portance de l’arase : 35 MPa visée mais 80 MPa mesurée à la réception.
- Durée de vie : vingt ans.
- σ6 (sigma 6) de la couche de forme traitée et renforcée de fibres = 1,2 σ6 (sigma 6) de la couche de forme traitée sans fibres.
Le calcul mené avec le logiciel Alizé donne la structure de chaussée suivante :
- Couche de base : 8 cm GB3.
- Couche de surface : 3 cm BBM.
Des difficultés à surmonter
Le premier problème à résoudre était de corriger le matériau de la couche de forme, à savoir le sable de Fontainebleau. En effet, c’est un matériau fin (<350 µm), à granulométrie uniforme et homométrique, de grande pureté, extra-siliceux et de grains ronds à subanguleux. Son aspect est clair, régulier et homogène. Ce sable est composé de 97 à 99 % de silice pure, ce qui lui confère une forte résistance à l’usure et une bonne longévité. Mais sa finesse et sa granulométrie uniforme lui donnent des aptitudes médiocres pour le traitement et le compactage. Aussi est-il indispensable de les amender ou de les stabiliser pour une utilisation plus rationnelle.
Le second problème à résoudre était : comment incorporer la fibre de chanvre dans le matériau de la couche de forme et assurer une répartition homogène dans le matériau ? Cette difficulté a été surmontée par la mise au point d’un matériel spécifique, capable de disperser d’une façon homogène la fibre de chanvre à la surface du matériau de la couche de forme. Le malaxage à l’aide du pulvimixeur permettra sa répartition au sein du matériau jusqu’à la profondeur visée par le traitement.
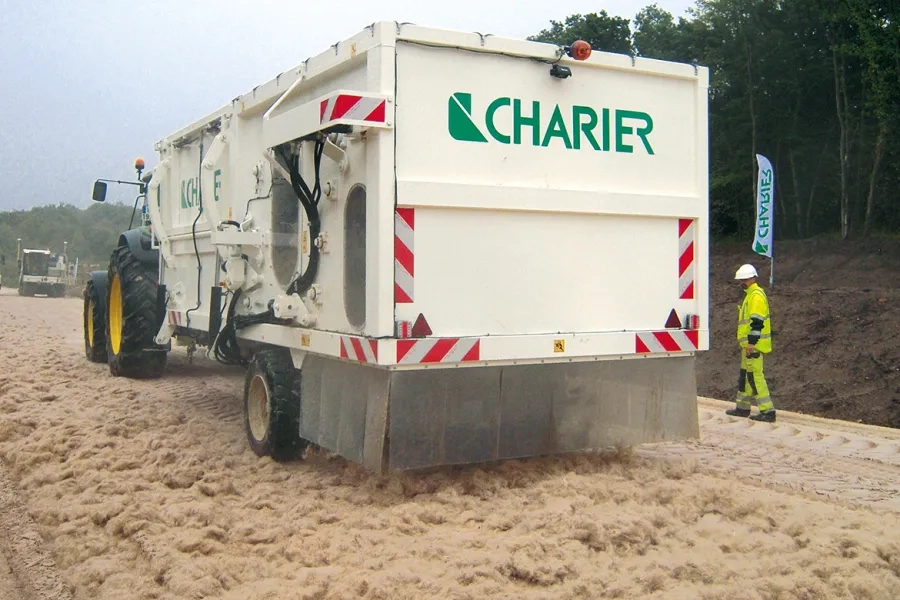
La réalisation de la couche de forme
Sur le chantier, une fois les terrassements réalisés, la portance de la partie supérieure des terrassements (PST) s’élevait à 80 MPa (au lieu de 35 MPa visés). Ensuite, pour réaliser la couche de forme, il a fallu rapporter dans un premier temps les matériaux (sable de Fontainebleau et grave calcaire). Puis ont suivi différentes phases : implantation (largeur de la voie à traiter) ; approvisionnement avec reprise sur stock (pelle sur chenilles, tombereaux articulés) ; mise en œuvre sur 40 cm pour une épaisseur finale de 36 cm (bull assisté GPS), afin de tenir compte du compactage et de la recoupe finale ; et enfin préréglage avec une niveleuse asservie GPS de façon à avoir une épaisseur homogène avant traitement.
Cette phase est très importante, car un bon réglage ne peut être garanti que s'il y a une recoupe de la couche après traitement. Aucun apport n'est possible dans la phase de réglage. " Une étape clé a été la parfaite humidification du matériau. Pour obtenir une teneur en eau optimale, nous avons employé une arroseuse à enfouissement (jets en profondeur) puis réalisé un malaxage d’homogénéisation au pulvimixeur, et ce préalablement aux opérations de traitement de la couche », explique Grégory Verhaeghe, directeur des travaux chez Charier. Puis il a été procédé à l’épandage des fibres de chanvre à l’aide d’un matériel spécifique conçu et fabriqué par l’entreprise Charier ".
Cette opération, réalisée en deux passages, a été suivie de l’opération de malaxage à l’aide d’une stabilisatrice Wirtgen WR 240i, assurant au mélange matériau + fibres de chanvre une bonne homogénéité.
Le traitement proprement dit a été réalisé en deux opérations successives : un épandage du liant hydraulique routier à raison de 6 % (soit plus de 40 kg/m2) à la surface du matériau, suivi d’un malaxage à l’aide de la stabilisatrice Wirtgen. Le sol a ensuite été remis en forme. La teneur en eau est contrôlée : si elle s’avère insuffisante, on procède alors à un ajustement par enfouissement et à une nouvelle remise en forme. Trois types de compacteurs se sont chargés du compactage (10 passes) : à bille lisse, dameur (pour limiter le feuilletage), puis à pneus (pour donner un bel uni).
« Une niveleuse assistée par théodolite motorisé effectue le réglage par recoupe de la couche traitée, pour obtenir un résultat au centimètre près. On obtient ainsi un très bon uni et un profil en long très régulier », ajoute Grégory Verhaeghe. Un enduit de cure a ensuite été appliqué pour protéger la couche de forme et pour assurer une bonne prise hydraulique du mélange, puis un gravillonnage léger a été réalisé. À noter que la circulation des véhicules a été neutralisée pendant une semaine, pour ne pas rompre la prise hydraulique.
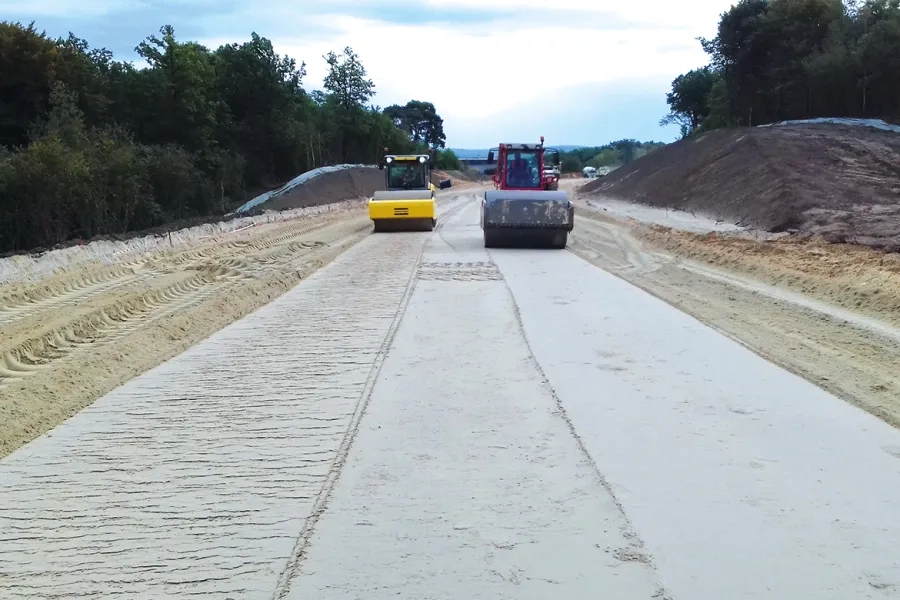
Un contrôle strict, réalisé en continu sur le site
« Tout est rigoureusement contrôlé sur le chantier : teneur en eau avant traitement, contrôle par pesée de la quantité de liant épandue, vérification de la profondeur de malaxage, teneur en eau après le deuxième malaxage », explique Miguel Dioniso, chef du laboratoire Charier. La qualité du compactage et les objectifs de densification (taux de compactage) ont été vérifiés sur la base d’essais et de références Proctor en laboratoire. Ensuite, le compactage « chantier » a été mesuré au moyen d’un gammadensimètre, l’objectif étant d’atteindre 98,5 % de l’optimum Proctor en couche moyenne et 96 % en fond de couche. À cela ont été ajoutés des essais sur éprouvettes pour les tests d’écrasement à 14, à 28 et à 90 jours, des carottages à 28 et à 60 jours, des essais en compression aux jeunes âges, des mesures de résistance à la traction, des mesures du module. Enfin, pour contrôler la déformabilité de la couche de forme, des déflexions ont été mesurées sur l’ensemble du tracé.
« Quand l’entreprise Charier nous a fait part de l’innovation de ce chantier et des enjeux à atteindre, nous avons proposé un de nos meilleurs liants hydrauliques routiers : le Rolac Optimum du Havre compatible avec cette solution de traitement fibrée. L’étude technique a ensuite démontré le bien-fondé de ce choix », précise Jean-Christophe Redon, directeur adjoint à la direction nationale des ventes Routes de LafargeHolcim. Et il ajoute : « Nous sommes très heureux d’avoir pu accompagner cette innovation, qui sera, nous l’espérons, une voie supplémentaire pour l’optimisation des structures routières en sols traités. »
Le Partenariat Public-Privé (PPP)
- Dialogue compétitif durant un an pour aboutir à une solution innovante.
- Dossier proposé dans le cadre du concours de l’Agence de l’eau.
- Agglomération : 279 k€/an sur vingt ans + 1000 k€ pour la phase de mise au point de la solution innovante et des études (aucun emprunt n’a été contracté).
- Entreprise Charier : la conception, la construction, le financement, l’entretien courant et l’entretien structurel pendant vingt ans.
Comme toutes les techniques innovantes menées dans le cadre d’un partenariat PPP, ce chantier va permettre de gagner sur le coût total du projet à hauteur de 30 %.
Réalisation de la couche de forme en 10 phases
- La préparation du matériau : mélange du sable de Fontainebleau et de la grave calcaire.
- L’ajustement de l’état hydrique : humidification pour obtenir une teneur en eau optimale.
- L’épandage de la fibre de chanvre.
- Le malaxage du matériau de la couche de forme avec la fibre de chanvre.
- L’épandage du liant hydraulique routier : pour réduire et maîtriser la dispersion du liant, il convient d’utiliser un épandeur à dosage pondéral, asservi à la vitesse d’avancement.
- Le malaxage : réalisé au moyen d’un pulvimixeur dont la cote de fond de malaxage est asservie en GPS.
- Le compactage partiel doit suivre la fin du malaxage pour ne pas laisser un matériau foisonné exposé aux intempéries et doit apporter 70 à 80 % de l’énergie exigée pour obtenir la qualité de compactage recherchée.
- Le réglage : par rabotage, à la niveleuse, sur toute la largeur.
- Le compactage final doit être réalisé immédiatement après le réglage final.
- La protection de surface : destinée à imperméabiliser la couche traitée et à la protéger des intempéries, de l’évaporation de l’eau et du trafic.
- Le dimensionnement de la structure a intégré les performances de la couche de forme traitée (liant Hydraulique + fibre de chanvre)
La fibre de chanvre
Le chanvre est une variété de cannabis à faible teneur en THC (< 0,2 %). Il est cultivé dans plusieurs régions françaises sur environ 15 000 hectares, dont 900 hectares dans le sud de l’Île-de-France.
Fibre de chanvre du chantier en provenance de Vendée (production locale indisponible au moment des travaux, usine en cours de construction dans l’agglomération de l’Étampois Sud-Essonne).
Un concentré d’innovations
Les innovations techniques, technologiques et de développement durable s’appliquent dans tous les domaines :
- Valorisation de la production locale de chanvre en sous-couche routière
- Autonomie énergétique
- Gestion des eaux pluviales
- Intégration paysagère
- Création de cheminements doux
- Protection de la biodiversité
- Protection de la flore
Caractéristiques de la déviation
- Longueur de la déviation : 2 km
- Largeur de la chaussée : 9 à 13 m
- Décapage de la terre végétale : 20 000 m3
- Déblais/remblais : 50 000 m3
- Couche de forme : 6 000 m3
- Liant hydraulique routier : 1 000 t de Rolac Optimum LH
- Fibre de chanvre : Chanvre technique Biofib‘ de Cavac Biomatériaux
- Matériaux bitumineux : 6 000 t
Principaux intervenants
Maîtrise d’ouvrage : Agglomération de l’Étampois Sud-Essonne - Entreprise : Charier TP - Fournisseur du liant hydraulique routier : Rolac Optimum LH - LafargeHolcim - Fournisseur de la fibre de chanvre : Gâtichanvre
COMMENTAIRES
LAISSER UN COMMENTAIRE