Le béton compacté routier (BCR) fait peau neuve
Un nouvel adjuvant de surface permet d’améliorer les finitions esthétiques du BCR tout en augmentant ses performances et sa durabilité. Un nouvel avantage compétitif pour ce béton très résistant qui ne manque pas d’atouts !
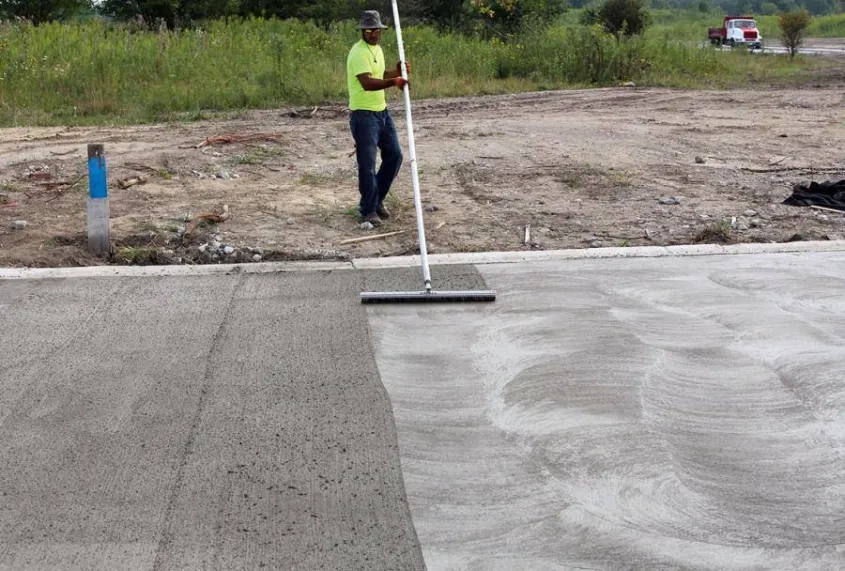
L’utilisation du béton pour la réalisation d’infrastructures routières suscite un intérêt sans cesse croissant, en France et dans le monde. Ce succès tient à ses multiples avantages.
En premier lieu, la polyvalence : il permet de réaliser une vaste gamme de voies, de l’autoroute à la chaussée urbaine en passant par les axes secondaires ou les voiries rurales, forestières, agricoles ou de lotissement.
Ensuite, les nombreux avantages procurés aux usagers, aux maîtres d’œuvre et aux maîtres d’ouvrage :
- un niveau de service élevé, associé à un haut niveau de sécurité (adhérence par tous les temps, absence d’orniérage, bonne visibilité due à une bonne réflexion de la lumière) ;
- un bilan économique à long terme favorable procuré par sa durabilité (résistance à la chaleur, au froid et au gel), sa solidité (résistance aux charges, à l’érosion et aux agressions chimiques) et son entretien réduit ;
- une intégration environnementale, avec l’utilisation de granulats locaux ;
- une réalisation normée (NF P 98-128 du 9 août 2014) et une mise en œuvre rapide.
À partir des mêmes constituants, il est possible d’obtenir une grande variété de bétons aux caractéristiques adéquates pour une utilisation routière. On peut ainsi recourir à un béton pervibré (dosé de 300 à 350 kg de ciment par m3), à du béton fluide de composition classique (avec incorporation d’un fluidifiant), un béton poreux (porosité entre 15 et 30 %) ou encore un béton compacté, réputé pour sa résistance et sa durabilité.
Le béton compacté routier (BCR)
Mais d’abord, un rappel. Le béton compacté routier (BCR) est obtenu avec les mêmes constituants de base que le béton classique, à savoir un mélange de :
- ciment : conforme à la norme NF EN 197-1, de type CEM I, CEM II, CEM III, CEM IV ou CEM V ;
- granulats : conformes aux normes NF EN 13242 et NF P 18 545. Ils constituent 75 à 85 % du volume total, et peuvent être roulés (sable siliceux) ou concassés (sable calcaire, gravier, grave...). Pour limiter les problèmes de ségrégation et en vue d’une meilleure qualité de surface, la dimension maximale du granulat doit être inférieure à 20 mm et le fuseau granulométrique divisé en plusieurs fractions (exemple : 0/3-3/8-8/16). Toutes les fractions doivent avoir un indice de concassage supérieur à 30 % dans le cas d’un trafic faible et environ 100 % dans le cas d’un trafic élevé. Ces granulats ont un indice de plasticité non mesurable et une teneur en matière organique inférieure à 0,2 % ;
- eau : conforme à la norme NF P 98 100, le BCR est un béton sec à affaissement nul. Sa teneur en eau doit donc être faible ;
- éventuellement, adjuvants : dans des proportions spécifiques et avec précaution. En effet, la durée courte de malaxage et la faible quantité d’eau limitent l’effet de ces adjuvants, d’où une augmentation du dosage pour en accroître l’efficacité.Les plus courants sont des retardateurs de prise, permettant d’augmenter la durée de transport et de mise en place du béton, de maintenir longtemps la consistance recherchée du BCR ou de ménager la contrainte des reprises de bétonnage. D’autres sont des réducteurs d’eau permettant une amélioration de l’homogénéité de la pâte. Les accélérateurs de prise sont peu utilisés et les fluidifiants exclus, car ils peuvent provoquer un ressuage ou une déformation excessive à la suite du compactage.
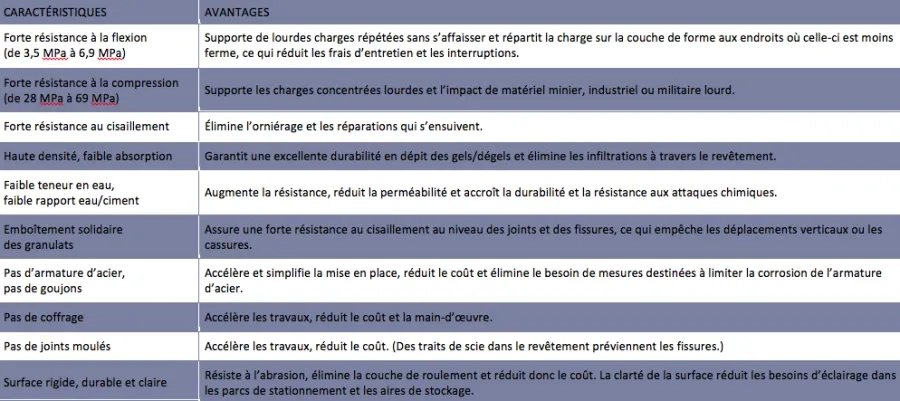
C’est pour ce béton, qui cumule de nombreux avantages, qu'un adjuvant de nouvelle génération, qui en facilite grandement la mise en œuvre vient d'être mis au point.
Gain esthétique très appréciable
Dans ce domaine des adjuvants, le dernier-né de Moderne Méthode, leader européen des bétons décoratifs, marque une évolution décisive. Selon son concepteur, BCR Surface Pro change la donne en offrant deux avantages ultra-compétitifs.
D’abord, il offre un gain esthétique très appréciable car il permet au béton d’être taloché fin, avec suffisamment de pâte cimentaire en surface pour recevoir une finition balayée traditionnelle. Il peut également être teinté pour renforcer l’apparence de revêtement traditionnel coloré.
Ensuite, il procure un gain plus directement économique en augmentant les performances et la durabilité du matériau. Les tests réalisés par la société soulignent l’amélioration de la résistance de surface aux cycles de gel/dégel, ainsi qu’aux attaques chimiques et à l’usure par abrasion.
« C’est une innovation décisive qui apporte une plus-value importante au béton compacté routier, se réjouit Frédéric Ljung, le PDG de Moderne Méthode, basée à Saint-Soupplets (Seine-et-Marne).
La fonctionnalité et la dimension économique du BCR alliées à l’esthétisme du dallage béton coulé sur place rendent ce procédé unique. Ce nouvel adjuvant favorise le développement de la pâte cimentaire pour une meilleure finition, augmente la résistance à l’abrasion, crée une surface plus dense et moins perméable et donne au BCR une surface fermée, lisse ou balayée. »
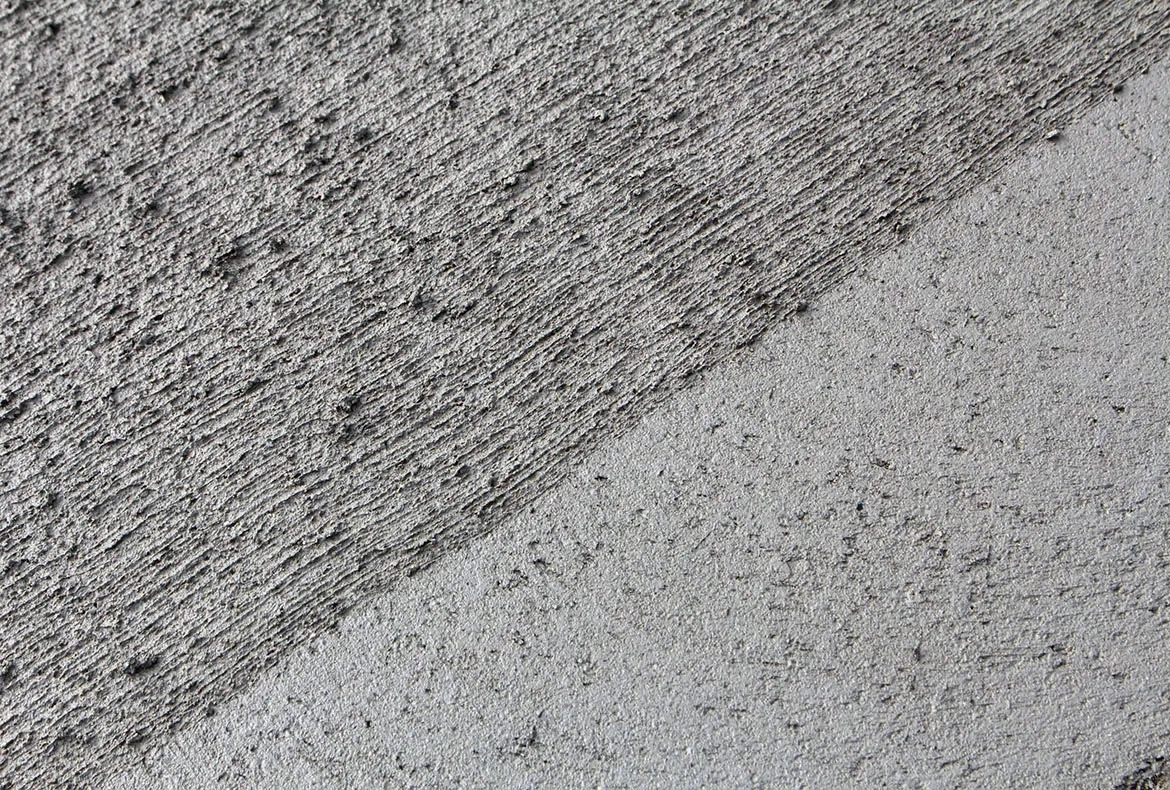
Efficacité avérée
Moderne Méthode a fait réaliser des tests indépendants sur des chantiers récents, en conditions réelles, qui confirment les bonnes performances de son adjuvant. Pour le BCR choisi, une moitié de la surface a été traitée avec le nouveau produit et finie à la talocheuse mécanique, l’autre moitié n’a pas été traitée et finie traditionnellement au rouleau. Après 28 jours, les échantillons ont été découpés et examinés en laboratoire.
Résultats : la résistance à l’écaillage du BCR traité et exposé aux produits chimiques de déverglaçage a bondi de 84 %, tandis que le cycle gel/dégel accéléré dans l’eau a progressé de 15 %. Les résistances à l’impact (+ 49 %) et à l’abrasion (+ 23 %) ont été grandement améliorées, tout comme la résistance à la pénétration d’ions de chlorures (+ 34 %).
Cette efficacité avérée se double d’une utilisation aisée. « Conditionné en bidons de 210 litres ou en conteneur IBC de 1 000 litres, BRC Surface Pro s’applique sur la surface juste avant le passage de la truelle mécanique, avec un pulvérisateur à grand débit. Il suffit ensuite de s’assurer que l’adjuvant a bien été mécaniquement intégré dans la surface avant d’entamer les finitions sur la pâte cimentaire additionnelle ainsi générée », résume Frédéric Ljung. Simplicité et efficacité.
COMMENTAIRES
1 COMMENTAIRE