Un viaduc tout en finesse pour le métro
La qualité architecturale du viaduc est essentielle à sa bonne insertion dans le tissu urbain de la métropole bretonne. La finesse et la légèreté de l’ouvrage masquent une vraie complexité technique.
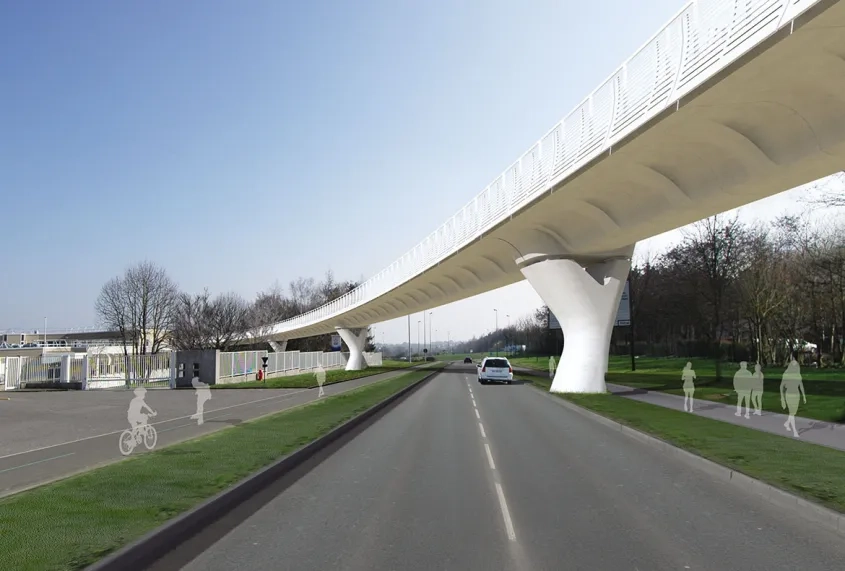
La future ligne B du métro automatique de Rennes Métropole reliera en 2020 le sud-ouest et le nord-est de l’agglomération bretonne. Après le succès de la ligne A, inaugurée en 2002, cette infrastructure vise à compléter l’offre de transport collectif et accompagner l’essor de pôles d’attractivité majeurs. Longue de 12,8 km et dotée de 15 stations, elle devrait accueillir 113 000 trajets quotidiens. Souterraine sur la majeure partie du tracé en cœur de ville, la ligne devient aérienne en son extrémité nord-est. Elle s’élève alors pour prendre la forme d’un viaduc urbain en béton précontraint de 2 400 m de long, ponctué de 3 stations aériennes.
Une architecture légère...
Le maître d’ouvrage, Rennes Métropole, et son mandataire, la Semtcar, ont veillé à ce que l’ouvrage s’insère le plus harmonieusement possible dans le tissu urbain. Implanté à 30 m environ des premières habitations, « ses abords font l’objet d’un aménagement paysager intégrant des masques arborés évitant les vues directes sur les maisons ainsi que des circulations douces (promenades piétonnières et voies vélos) », décrit Frédéric Philippeau, directeur Interface Projets pour la Semtcar.
La réussite esthétique de l’ouvrage constituait aussi pour le maître d’ouvrage un enjeu majeur. En lien avec le groupement de maîtrise d’œuvre, piloté par Egis Rail, la réflexion du cabinet d’architecture Lavigne Chéron s’est orientée vers la recherche de la plus grande finesse. L’ouvrage, intégralement réalisé en béton clair de teinte uniforme, dispose d’un tablier unique de très faible épaisseur (1,70 m), constitué de 973 voussoirs en béton précontraint assemblés en 36 ouvrages indépendants à 1 ou 2 travées, de 30 à 38 m de portée. Ses rives sont équipées d’écrans acoustiques doublés de bandeaux architecturaux en Béton Fibré à Ultra hautes Performances (BFUP). « Ce matériau qualitatif permet de dessiner un bandeau de rives ménageant des persiennes qui donnent de la légèreté à l’ouvrage », expose Frédéric Philippeau. Pour souligner les fortes variations de courbures du tracé et le fort dévers de la voie, les 70 piles sur lesquelles repose le tablier possèdent un « déhanché » caractéristique dessinant tantôt un « Y » dans les courbes, tantôt un « X » aux abords des trois stations.
... masquant une grande complexité technique !
Chacune des spécificités architecturales du viaduc masque une grande complexité technique. Si l’obtention d’une teinte claire et uniforme entre le tablier et les piles est un défi (voir encadré), la réalisation du « déhanché » des piles en est un autre. Pour soutenir les efforts induits par cette courbure gracieuse, et résister aux chocs de véhicules, les piles sont très fortement ferraillées : la densité d’armatures de leur chevêtre atteint jusqu’à 385 kg/m3. Pour s’assurer de la bonne répartition du béton dans tout le volume dans cet enchevêtrement d’armatures, de nombreuses cheminées de bétonnage et colonnes de vibration sont prévues lors de l’assemblage des cages d’armatures. « La difficulté principale pour la mise au point du ferraillage des appuis est due au fait que ces réservations entraient en conflit avec les armatures principales », explique Michel Bousquet, directeur du projet pour le groupement constructeur. Pour résoudre ce casse-tête, les entreprises ont fait appel à un modèle numérique de calcul tridimensionnel.
Autre défi à relever pour le groupement constructeur : la prise en compte de la forte sinuosité du tracé – le rayon de courbure atteint par endroits 125 m – et du dévers – jusqu’a 10 %. Ces contraintes pesaient notamment sur la géométrie des voussoirs. Ainsi, « chacun des 973 voussoirs possède des caractéristiques et une géométrie uniques, décrit Matthieu Carry. Pour arriver à optimiser leur fabrication, nous avons conçu des outils de coffrage en nombre limité et réglables, permettant de maîtriser l’ensemble des variations géométriques ».
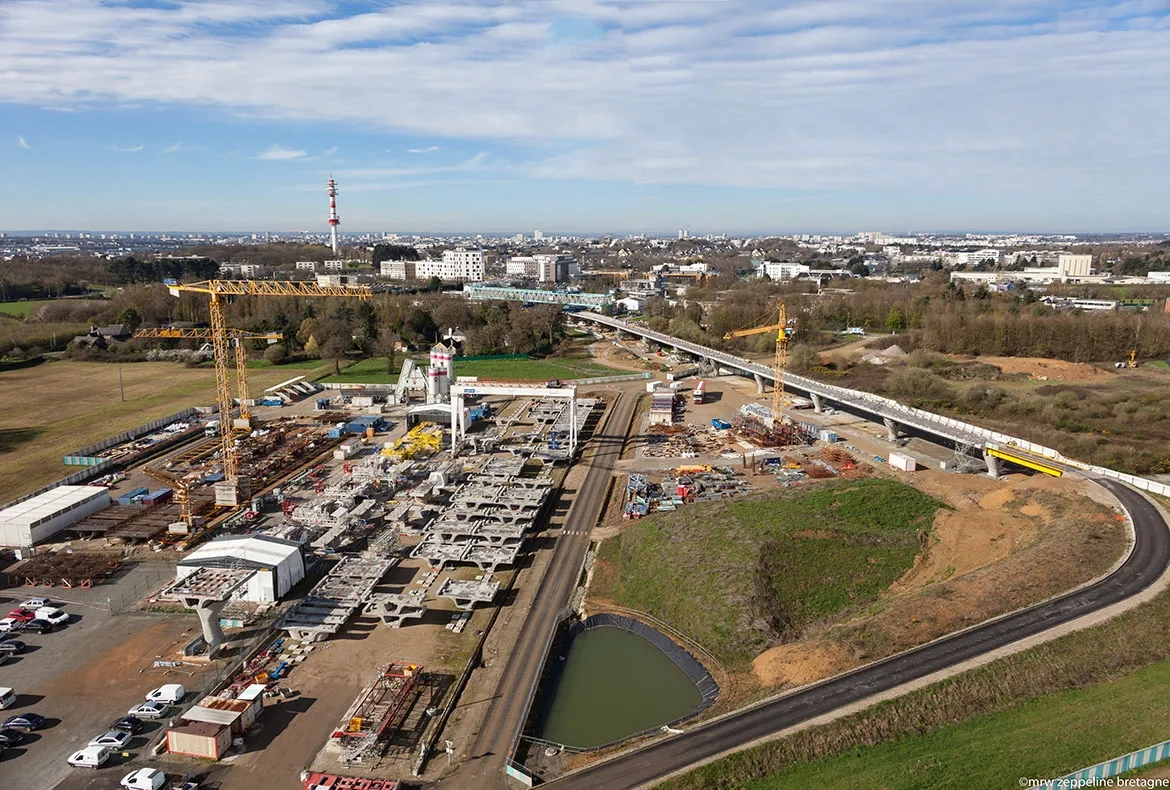
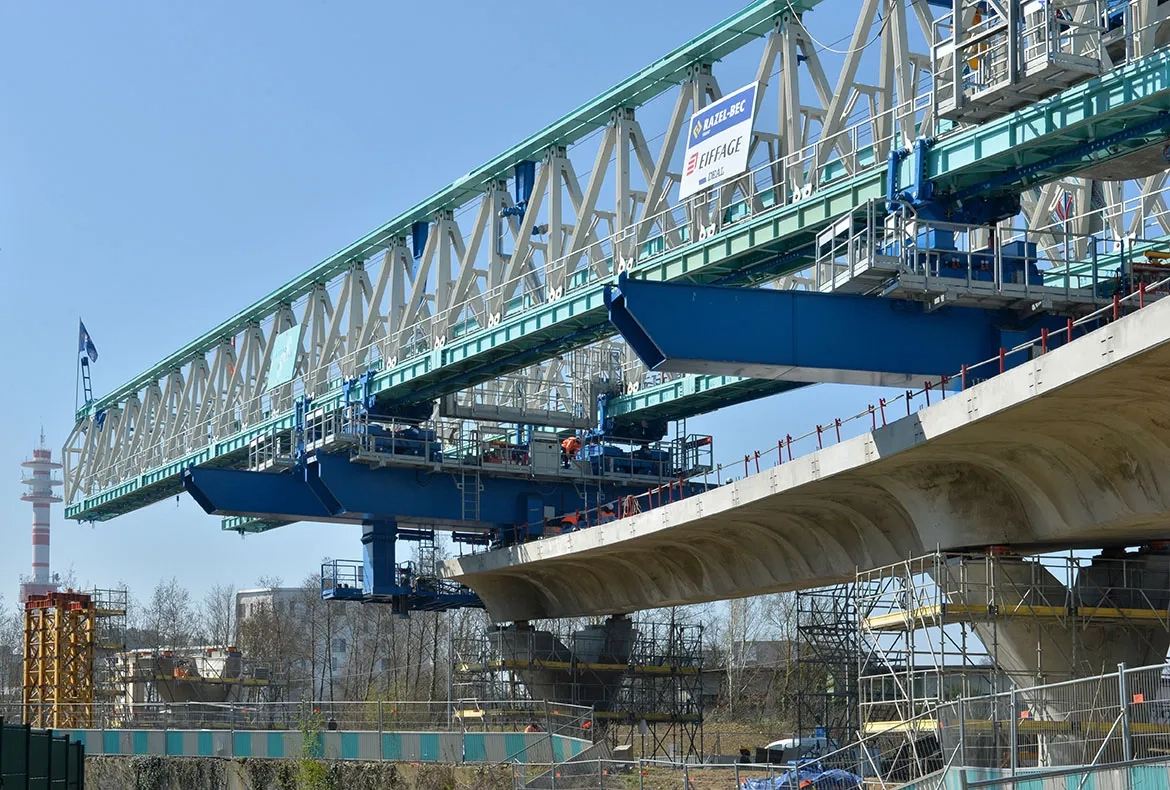
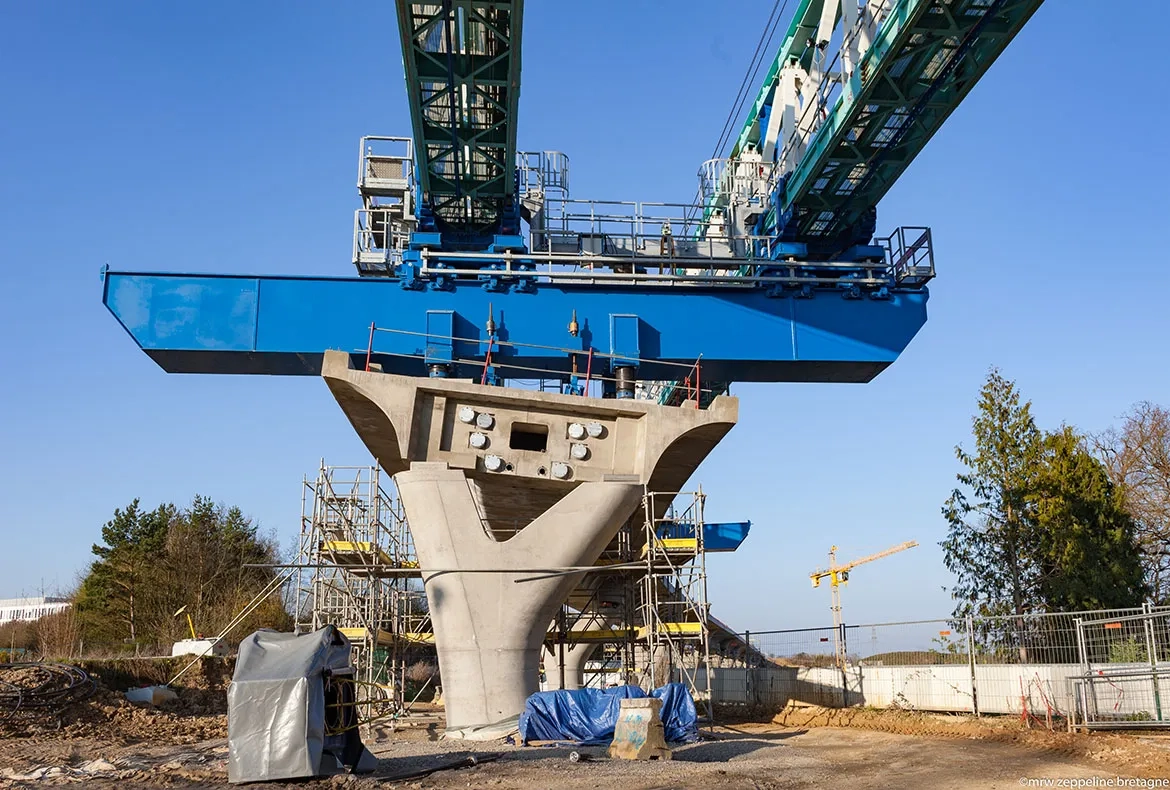
La préfabrication au service de la furtivité
Pour mieux faire accepter le projet aux riverains, le maître d’ouvrage souhaitait un chantier « furtif », minimisant les nuisances et son incidence sur la circulation routière, qui devait être maintenue la quasi-totalité du temps. Pour répondre à cette problématique, le groupement d’entreprises a décidé d’industrialiser les méthodes de construction. La totalité des voussoirs est ainsi préfabriquée sur une aire dédiée de 4,5 ha. Une fois préfabriquées dans un atelier spécifique, les cages d’armatures sont transférées à l’atelier de bétonnage des voussoirs. Là, six cellules coffrantes fonctionnant en parallèle permettent de réaliser les voussoirs courants (30 t en moyenne) et les voussoirs sur pile, de 63 t. L’objectif est de fabriquer 80 unités en moyenne par mois. Les voussoirs sont pris en charge par un portique roulant qui les dépose sur une zone de stockage. Ils sont ensuite acheminés par des fardiers jusqu’à la zone de pose en empruntant les portions de tablier déjà construites. La fabrication, le stockage et l’acheminement des voussoirs jusqu’à leur lieu de pose se font ainsi selon un circuit propre au chantier, qui n’impacte pas l’environnement extérieur.
Deux travées lancées par une poutre en une seule fois Précédant la pose du tablier, l’atelier de construction des piles prend la forme d’un chantier mobile très étroit évoluant le long des voies de circulation que longe le tracé. Très étroite, son emprise au sol s’étire sur seulement 200 m pour limiter la gêne. Les cages d’armatures des chevêtres sont acheminées depuis l’aire de préfabrication et connectées à celles des fûts, qui sont elles assemblées in situ. Le coulage en place des piles peut alors démarrer dans un outil coffrant courbe fabriqué sur mesure.
La dernière étape est celle de la pose des voussoirs. Elle est réalisée à l’aide d’une poutre autolanceuse, structure métallique qui permet de mettre en place jusqu’à deux travées de 38 m en une seule fois. Reposant sur trois des appuis définitifs du futur viaduc, cette poutre géante est munie d’un chariot de levage capable de reprendre les voussoirs approvisionnés par les fardiers. Ces voussoirs sont suspendus les uns après les autres à la poutre dans un ordre prédéterminé. Une fois l’équivalent de deux travées complètes suspendu, les voussoirs sont repris et mis en position définitive. Les câbles de précontrainte, qui permettent de rendre le tablier monolithique, sont alors mis en tension. La poutre est ensuite avancée par une succession de déplacements de ses points d’appui et de translation, qui lui permettent de négocier les virages les plus serrés. Un nouveau cycle de deux semaines peut alors démarrer à raison de 2 postes de travail 6 jours sur 7. Le chantier, démarré en octobre 2015, devrait être livré mi-2018. Les nouvelles rames sur pneus CityVal de Siemens devraient quant à elles entrer en service en 2021.
Un béton clair homogène pour les voussoirs et les piles
Pour la qualité esthétique de l’ouvrage, le maître d’ouvrage souhaitait que les teintes claires des bétons des piles et du tablier soient homogènes. Pour s’assurer de l’homogénéité du rendu, le groupement d’entreprises a fait le choix d’un béton unique pour couler l’ensemble des éléments structurels. Mais ceux-ci n’étant pas soumis aux mêmes sollicitations mécaniques, une formulation optimale devait être trouvée. « Elle devait d’une part permettre d’obtenir une résistante importante au jeune âge pour pouvoir décoffrer les voussoirs dans un délai compatible avec la cadence de production, et d’autre part offrir une résistance élevée à 28 jours », précise Matthieu Carry, directeur de production pour le groupement d’entreprises. Finalement, un béton de classe de résistance C 55/67 a été choisi. Le liant équivalent dosé à 405 kg/m3 est constitué d’un ciment CEM I 52,5, de laitiers moulus de hauts-fourneaux et de métakaolins pour obtenir la teinte claire.
Le viaduc entre en gare !
Le viaduc de la ligne B du métro desservira trois stations aériennes. Chacune d’elles est conçue comme une « boîte » à l’architecture spécifique. Pour raccourcir le délai de construction global de la ligne, les phasages des chantiers du viaduc et des stations ne sont pas interdépendants. La poutre de lancement du viaduc doit ainsi être en mesure de poser les voussoirs de la section traversant la station avant que celle-ci soit terminée. Les stations sont structurellement totalement indépendantes du viaduc. Les entreprises de construction des stations ont adapté leurs méthodes constructives à cette spécificité. Elles n’ont pas droit à l’erreur : lorsque le viaduc entre en gare, quelques centimètres seulement peuvent séparer le bord du tablier des quais !
Chiffres clés
Longueur du viaduc : 2,4 km
Largeur du tablier : 8,6 m
70 piles : dont 40 % fondées sur pieux, 60 % sur semelles superficielles
973 voussoirs
Béton : 22 000 m3
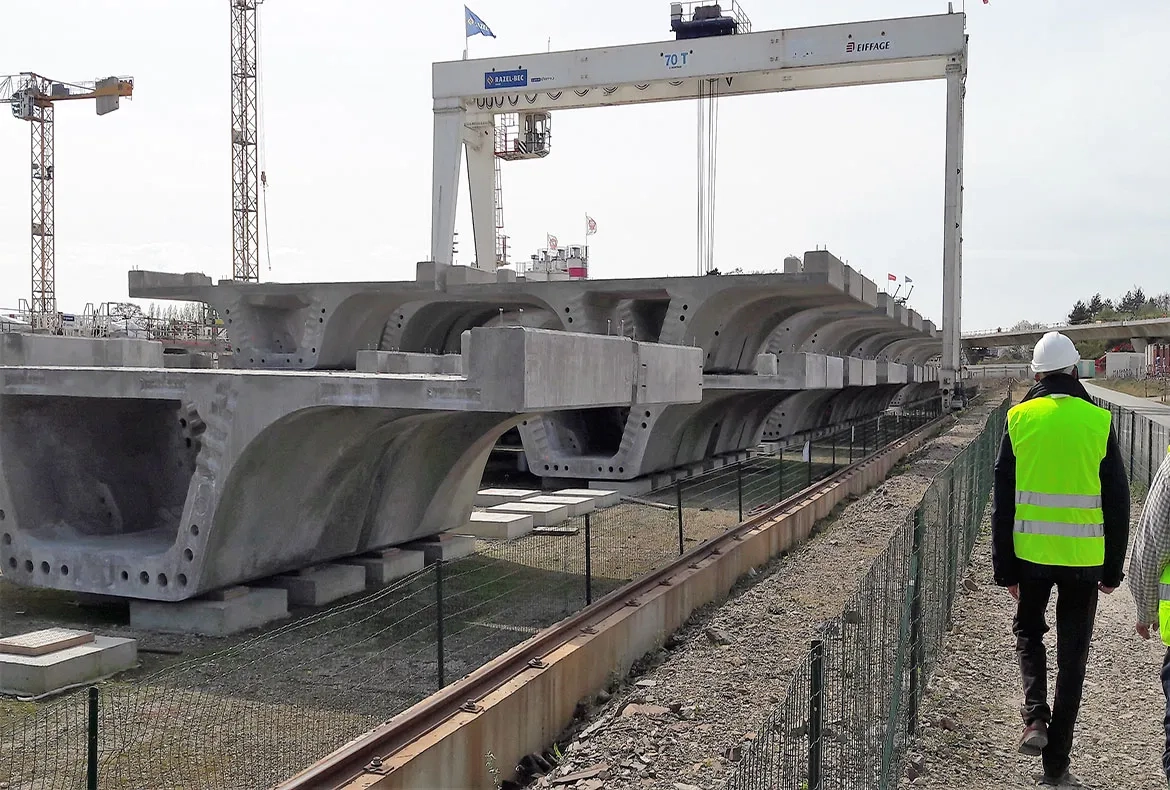
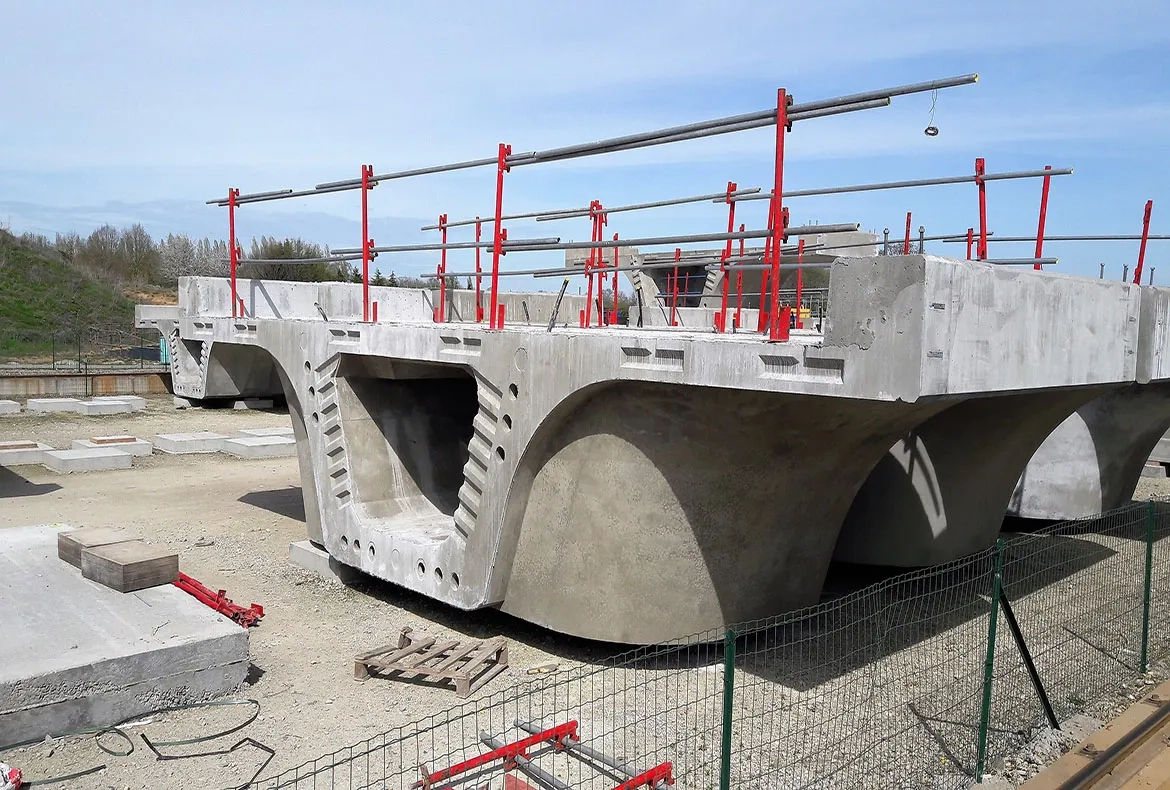
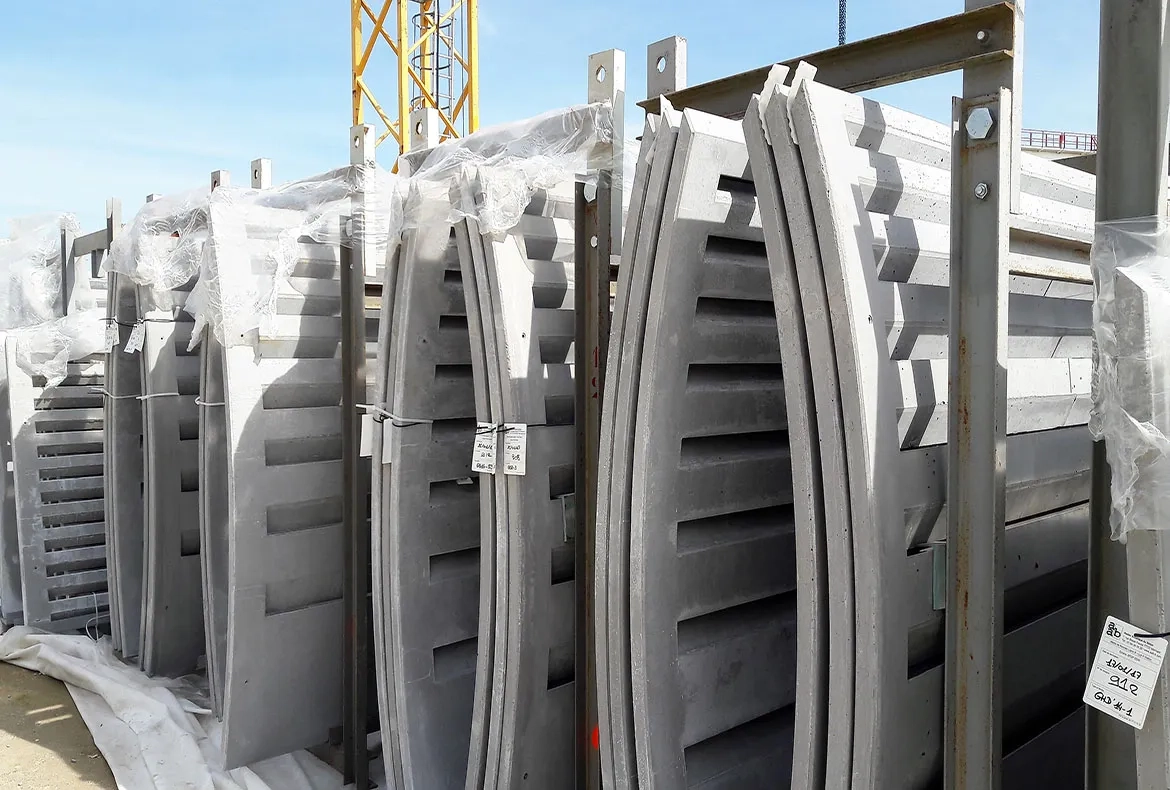
Reportage photos: © Lavigne Chéron Architectes ; Eiffage et Razel Bec ; Olivier Baumann
VIADUC – Maître d’ouvrage : Rennes Métropole – Mandataire du maître d’ouvrage : SEMTCAR – Maître d’œuvre : Egis Rail, Egis Bâtiment Centre Ouest, Arcadis, L’Heudé & L’Heudé – Architecte viaduc : Lavigne et Chéron – Groupement d’entreprises : Razel-Bec (groupe Fayat, mandataire), Eiffage Génie Civil – Contrôle technique : Socotec – Fournisseur ciment : Lafarge – Coût : 50 M€ HT.Stations aériennes – Architectes : Anthracite/AMA – Groupements d’entreprises : Angevin entreprise générale (mandataire)/Angevin SAS pour les stations Atalante et Beaulieu Université ; Cardinal Edifice pour la station « Cesson-Viasilva ».
COMMENTAIRES
LAISSER UN COMMENTAIRE