Une ombrière climatique inédite pour la gare TGV
Pour cette gare méditerranéenne, Marc Mimram a imaginé une gare-pont coiffée d’une ombrière inédite qui filtre la lumière. Grâce au BFUP, elle sert à la fois de structure et de couverture.
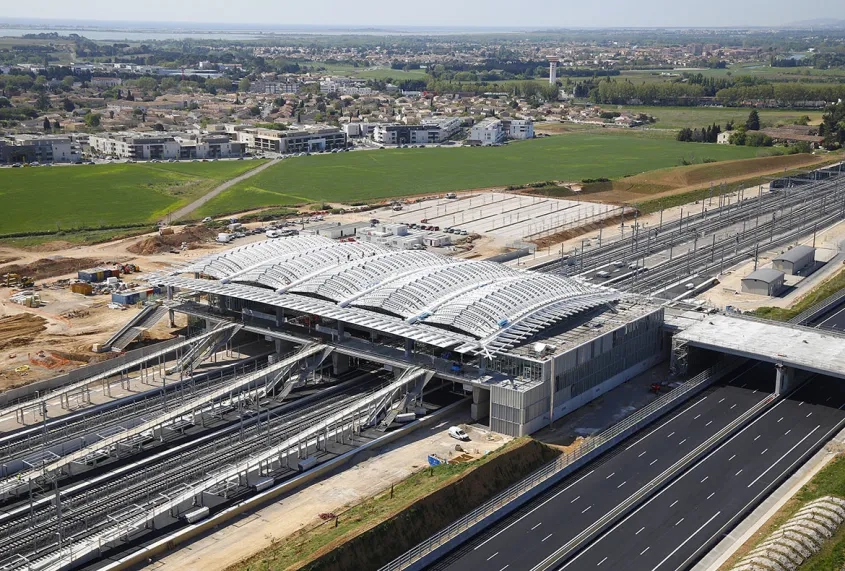
L’idée d’une ligne à grande vitesse de la vallée du Rhône jusqu’à Barcelone remonte aux années 1980. Après bien des aléas, un barreau du tracé ferroviaire est en cours de réalisation. Il s’inscrit dans le cadre du contournement de Nîmes et Montpellier, soit 60 km de ligne nouvelle mixte fret/voyageurs. Située au sud de l’agglomération montpelliéraine, la gare de la Mogère, proche d’Odysseum, est conçue comme un pont qui enjambe les voies de la nouvelle LGV, la rocade et l’autoroute A9. Conçu comme un pôle d’échange multimodal dans un secteur en devenir, l’équipement intègre les différentes modalités de transport : au sud, le « jardin » est dédié aux véhicules motorisés, avec la gare routière et les parkings ; à l’ouest, une gigantesque ouverture accueille les voyageurs du tramway.
Un bâtiment-pont
La gare se présente comme un « pont habité » qui franchit la voie ferrée au moyen d’une dalle de béton armé portée par 30 piles architectoniques en V (3,60 m de hauteur), des poutres primaires s’apparentant à des dalles autoportantes et 280 poutres secondaires. Plus impressionnant encore, le bâtiment voyageurs est abrité par une étonnante couverture, un grand « parasol » perforé, selon le mot de Marc Mimram, qui se déploie à l’extérieur (porte-à-faux de 7 m) pour couvrir les abords de la gare. Dans ce contexte méditerranéen, Marc Mimram Architecture & Ingénierie a préféré l’hypothèse d’une « ombrière climatique qui filtre la lumière » au vocabulaire de verre et d’acier des halles ferroviaires du xixe siècle. Climatique, parce que la forme aéraulique de la couverture permet, comme un spoiler de voiture, d’aspirer l’air pour accroître la ventilation naturelle, très importante à Montpellier. Filtrante, parce que les perforations, calculées en fonction de la course du soleil et de la distribution des efforts, filtrent les apports solaires avec de magnifiques jeux d’ombre et de lumière.
Hautes performances au pluriel
Point fort du projet, la couverture en BFUP se compose de trois types d’éléments : 115 longues « palmes » autoportantes qui franchissent les voies ; 480 coques d’habillage qui dissimulent la structure métallique porteuse ; 150 pièces qui forment une casquette périphérique en porte-à-faux de 7 m.
Cette couverture est tout à fait inédite : outre ses qualités esthétiques et la maîtrise des apports lumineux, sa singularité repose sur le fait qu’elle joue à la fois le rôle de structure et de couverture. Le secret ? Le recours au béton fibré à ultra hautes performances (BFUP) qui, grâce à son extrême résistance, lui permet d’assurer de grandes portées (18,30 m, correspondant à l’entraxe des voies ferrées) avec une grande délicatesse de forme. « Des hautes performances au pluriel, insiste l’ingénieur Romain Ricciotti, d’abord en termes de résistance mécanique qui autorise des longues portées avec des éléments d’une grande finesse, mais également en termes de durabilité car le BFUP est un béton parfaitement étanche et insensible aux agressions chimiques. » Formulé par le laboratoire de recherche de Lafarge, il s’agit d’un Ductal® blanc dosé à 1,75 % de fibres Inox, ces fibres remplaçant les armatures pour assurer la résistance en traction. La conception aura duré deux ans, au cours desquels Marc Mimram, l’entreprise François Fondeville, le bureau d’études Lamoureux & Ricciotti et Patrick Mazzacane, directeur de Méditerranée Préfabrication, ont travaillé de concert pour mettre au point les éléments de couverture et tous les accessoires.
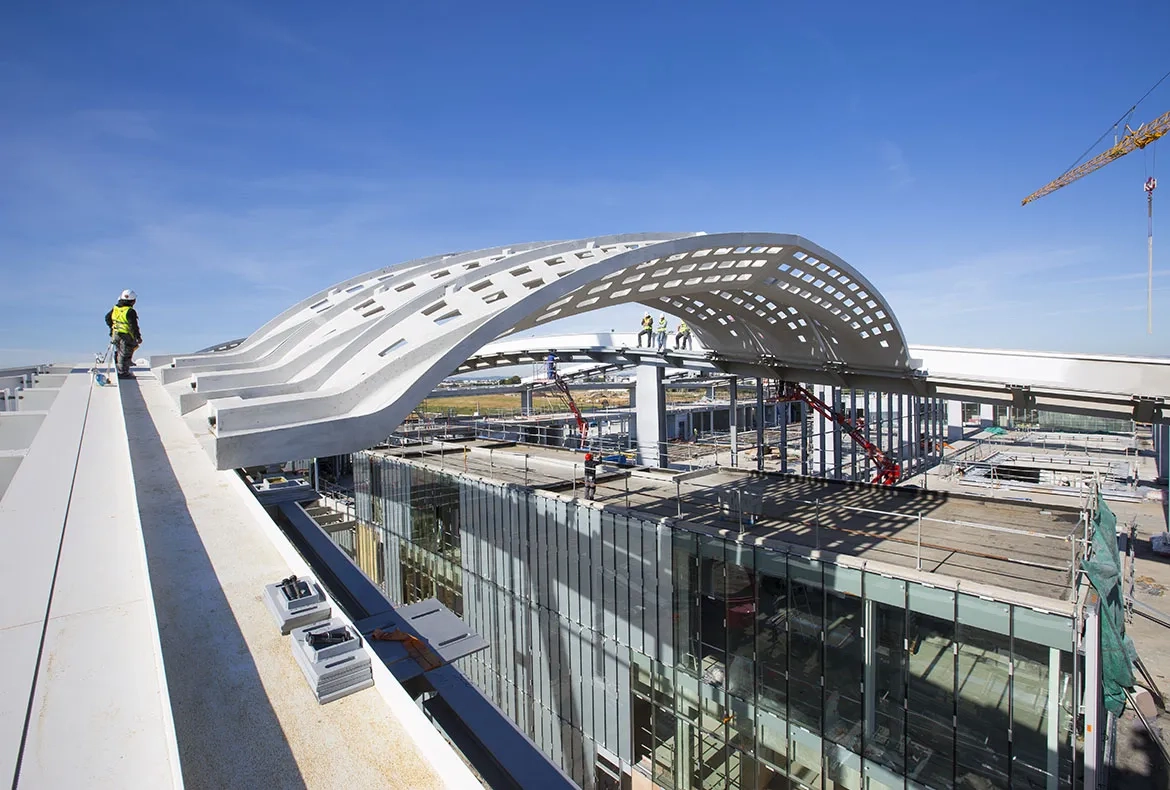
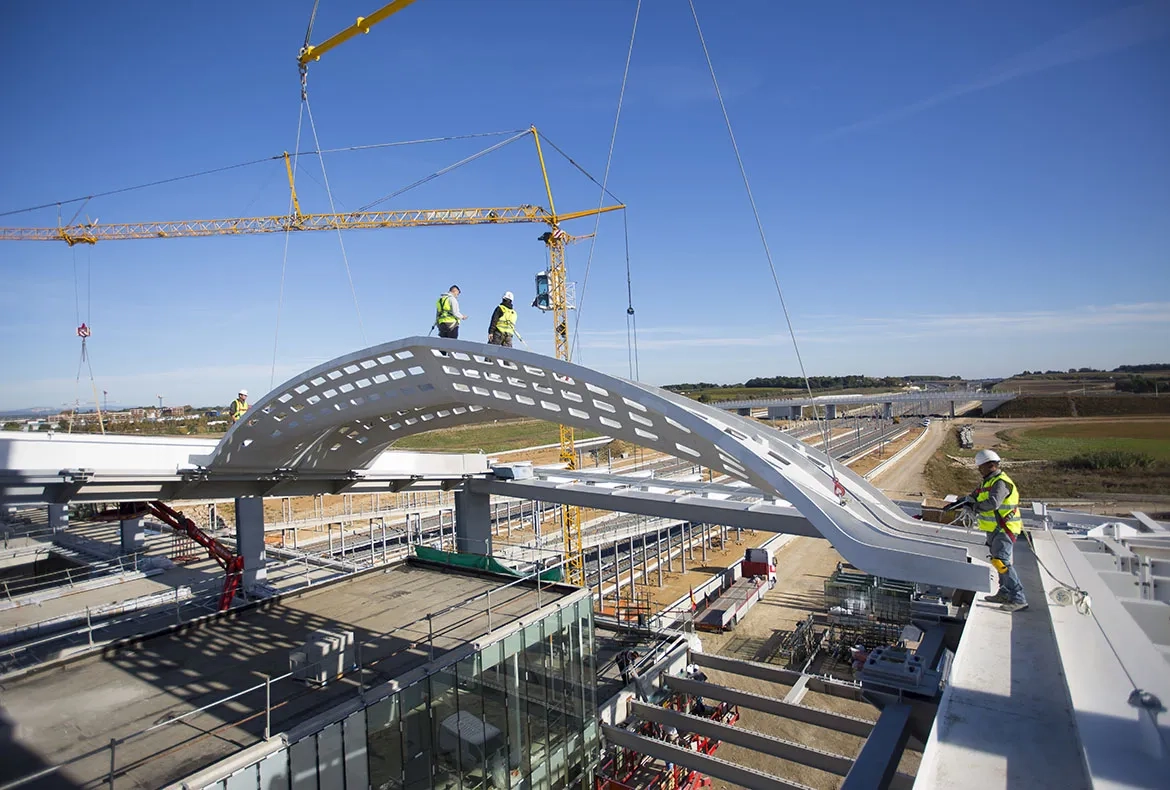
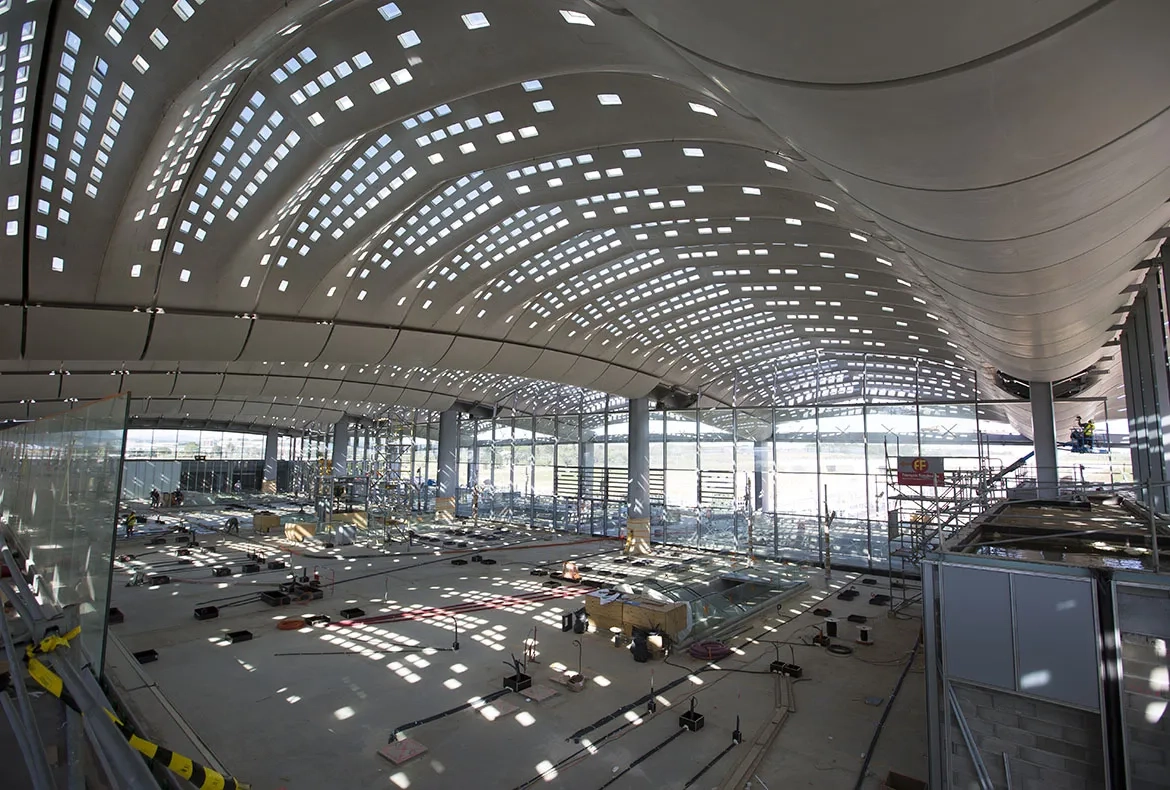
Plusieurs défis inédits
Si la couverture est inédite, les procédés de fabrication, le transport et la pose des palmes le sont aussi. « Parce qu’elles sont très élancées, d’une minceur extrême (4 cm en moyenne) et ajourées, il était impossible de les réaliser en deux parties. Le défi technologique a donc été de fabriquer des éléments monolithiques », résume Patrick Mazzacane. Cette option impliquait de préparer à l’avance la totalité du béton, soit 5,2 m3, pour garantir une parfaite homogénéité. Le process de fabrication n’a laissé aucune place à l’improvisation quant aux pesées, au temps de malaxage, au cycle de remplissage ou aux outils coffrants. « Dix gâchées, chacune prenant un peu moins de 20 min, étaient nécessaires pour réaliser une palme. L’opération se déroulant pendant les fortes chaleurs de l’été 2016, nous avons mis au point la fabrication en adaptant les températures ambiantes pour le malaxage et les différents temps d’attente et, en parallèle, avec les équipes de Lafarge Ductal, une adjuvantation qui tienne compte de ces contraintes.
Grâce au maintien de la bonne rhéologie, les conditions de moulage étaient excellentes. Le remplissage s’est effectué moule fermé par injection en des points judicieusement placés afin d’assurer la bonne répartition des fibres. » Les moules, au nombre de cinq, conformément au nombre de modules des palmes, ont été conçus en 3D par Méditerranée Préfabrication et ses partenaires moulistes, découpés au laser et assemblés sur gabarit. Une cage d’armatures passives située au centre de la palme reprend les efforts en torsion, telle la nervure d’une feuille à double courbure, à l’intérieur de laquelle sont positionnés les câbles de précontrainte (quatre torons gainés et graissés) : là encore, une opération délicate requérant une précision extrême.
Un chantier sensible
À pièces exceptionnelles, moyens de manutention hors du commun ! Les palmes fraîchement démoulées (48 h après leur fabrication),ont été acheminées sur le chantier par des semi-remorques à rallonge équipés d’un châssis sur mesure. Une fois sur site, restaient à réaliser la post-tension des « nervures », l’intégration des vitrages et des pavés acoustiques et, bien sûr, la pose des éléments de couverture sur la charpente. Un challenge pour l’entreprise Fondeville. « En raison du poids des éléments et de l’impossibilité de s’approcher, nous avons utilisé une grue de 1 200 tonnes et de 100 m de flèche », explique Georges Chammas, directeur des grands projets de Fondeville. « Pour couronner le tout, la pose ne pouvait se dérouler que de nuit, le chantier étant placé sous le cône de circulation de l’aéroport de Montpellier. »
Un choix sûr, efficace et pertinent
Pour la mise en œuvre de cette couverture, rien n’a été laissé au hasard : essais de convenance pour la formulation du béton et le coulage des monolithes, études en soufflerie au CSTB de Nantes pour évaluer les sollicitations de prise au vent et de secousses sismiques, test de chargement avec le CSTB et l’APAVE, appréciation technique d’expérimentation (ATEx) validée par le CSTB... Reste la question économique : « Il faut considérer cette solution dans sa globalité, assure Patrick Mazzacane, car elle résout plusieurs problématiques : la grande portée, la légèreté, l’esthétique, l’étanchéité et la durabilité. C’est pourquoi elle est tout à fait pertinente et compétitive au regard de l’économie de structure, de matière et de temps de réalisation. » « L’intérêt, conclut Romain Ricciotti, c’est d’avoir un seul composant pour la structure et l’étanchéité. La qualité du matériau et son association à une pièce monolithique, qui réduit considérablement le nombre d’interfaces et donc de points de faiblesse, sont les clés de la durabilité. »
Questions à Marc Mimram, architecte de la gare de la Mogère
Comment naît l’idée d’une telle couverture ?
J’ai été formé avec l’idée que l’on ne pouvait plus faire ce que faisaient hier Nervi, Torroja, Candela, Lafaille, Freyssinet… Les pièces moulées, les grandes coques en béton, les grands voiles minces, qui ont eu une grande résonance dans les années 50 ou 60, demandent beaucoup de main-d’œuvre. C’est devenu trop compliqué. Ce que j’essaie de démontrer ici, c’est qu’il est possible de faire à nouveau ce que nous pouvions faire hier. Avec le BFUP et la préfabrication, on parvient rapidement à créer une couverture étanche qui est en même temps une structure avec des finitions très soignées. C’est la première fois que l’on assure la mise hors d’eau à partir de la structure. C’est une vraie prouesse technique au service de l’architecture.
Est-ce l’occasion d’entrer dans une nouvelle ère ?
L’enjeu est de transformer l’infrastructure considérée comme un mal nécessaire en bien partagé. Nous sommes à un moment important où on peut l’envisager de manière positive, c’est-à-dire en la considérant non plus comme une contrainte mais comme une source de valeur intégrée dans une démarche globale de développement urbain où elle prendrait plusieurs formes : pont habité ou immeuble pont, comme cette gare, pont symbole, pont héritage historique, pont espace public, pont paysage, pont balcon, pont toit…
Chiffres clés
Gare : 10 000 m², dont une halle de 3 500 m² sur 11 m de hauteur dédiée aux voyageurs
Nombre de voyageurs par an en 2030 : 3,5 millions
Couverture : 7 500 m²
BFUP : 750 m3, 115 palmes, 480 coques, 150 éléments de casquette
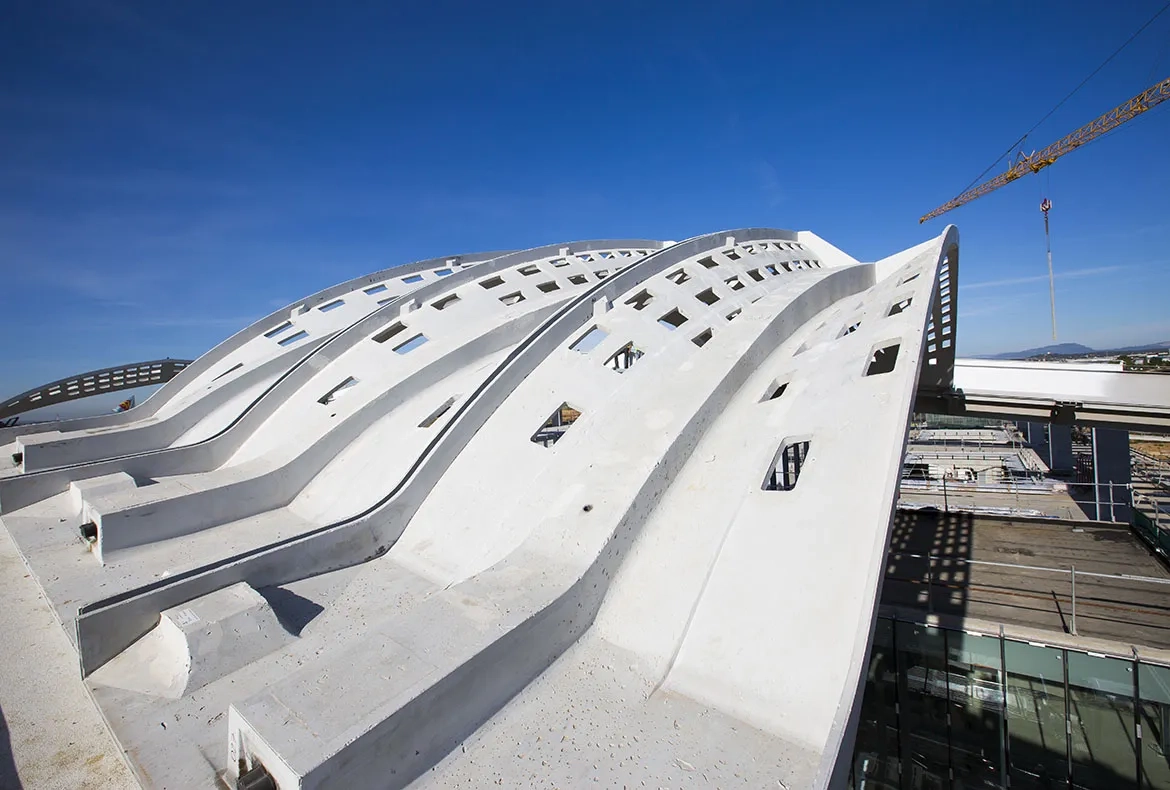
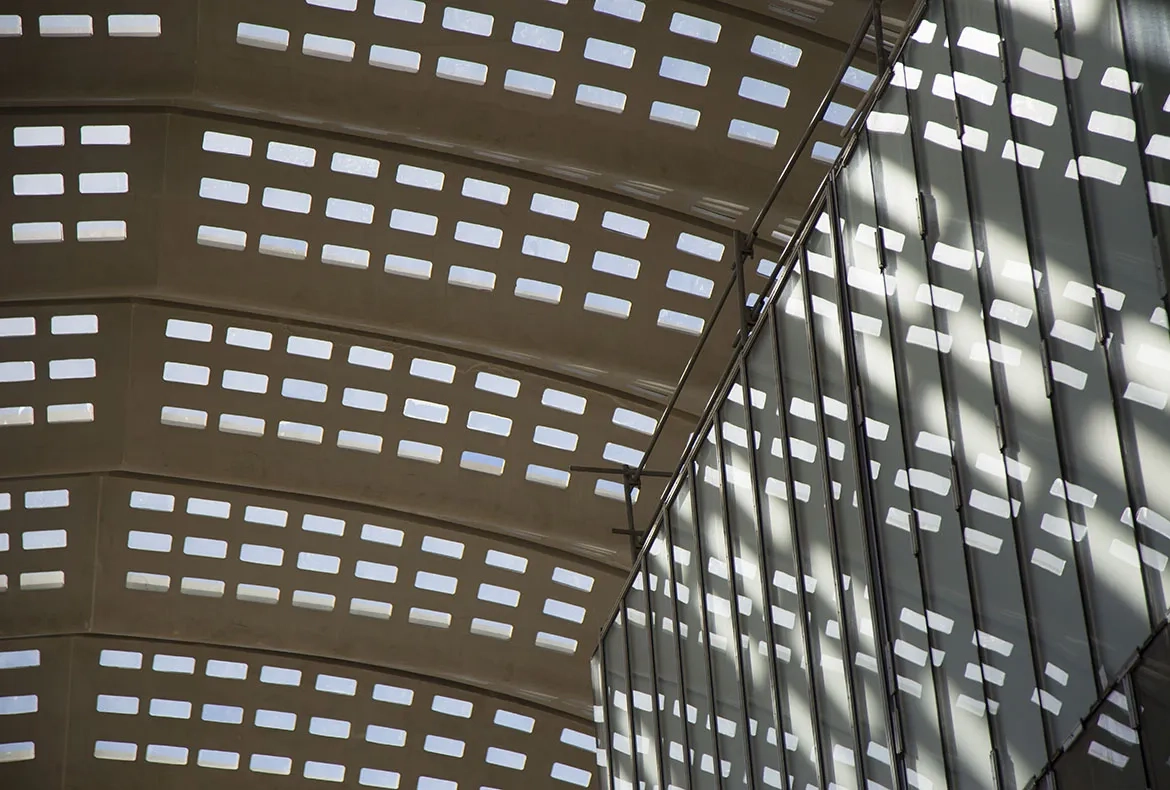
Reportage photos: Dronestudio pour François Fondeville; Mediterranée préfabrication
Maître d’ouvrage : SAS Gare de la Mogère – Maître d’œuvre : Marc Mimram Architecture & Associés, Marc Mimram Ingénierie ; Egis ; Atelier Nebout ; BET Lamoureux & Ricciotti ingénierie – Réalisation : François Fondeville – Fabrication palmes : Méditerranée Préfabrication – Fabrication coques et casquettes : Delta Préfabrication – Coût : 60 M€ HT.
COMMENTAIRES
LAISSER UN COMMENTAIRE