Fondations gravitaires XXL pour éoliennes en mer
Pour stabiliser les 71 éoliennes du futur parc éolien en mer de Fécamp, les équipes de Bouygues Travaux Publics ont érigé des fondations gravitaires géantes de 50 m de haut.
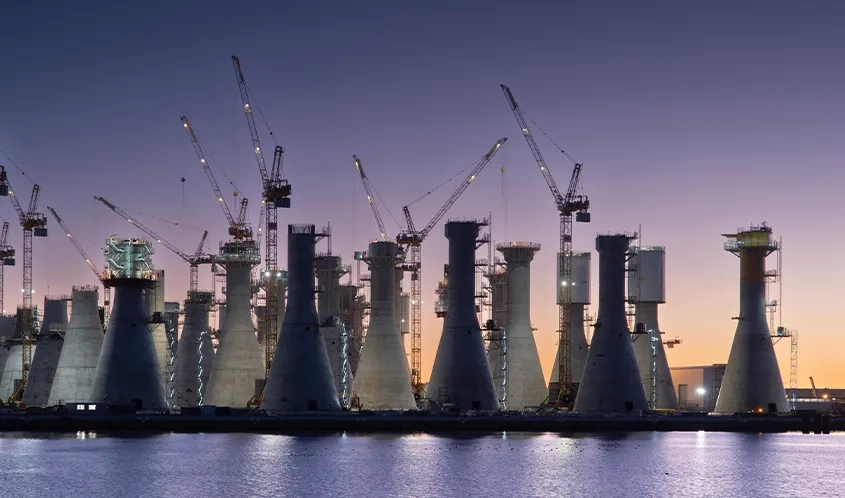
À l’horizon 2030, 17 parcs éoliens en mer devraient être exploités en France, pour une puissance cumulée de 10 GW. Il s’agit d’un véritable boom pour cette technologie, puisque aucun de ces parcs n’est encore opérationnel. En novembre 2023, l’un des premiers à être mis en service sera celui situé au large de Fécamp. Ses 71 éoliennes, installées entre 13 et 24 km des côtes normandes, déploieront une puissance totale de 500 MW. Chacune de ces géantes des mers, culminant en bout de pale à 180 m au-dessus des flots, devra être solidement maintenue au sol pour résister aux assauts répétés de la houle et du vent. Pour ce faire, le consortium de maîtrise d’ouvrage, mené par EDF Renouvelables, a étudié en phase préliminaire le type de fondations le mieux adapté pour garantir la stabilité de ces structures très élancées. « Nous avons examiné les trois typologies de fondations existantes – les monopieux, les “jackets” (tours à trois pieux) et les fondations gravitaires, simplement posées sur le sol – explique Bertrand Allanic, directeur du projet pour EDF Renouvelables. Les caractéristiques du sol, un calcaire très dur comprenant des zones de grès et de silex, ne se prêtaient pas bien à une solution forée ou battue. Si bien que nous nous sommes orientés rapidement vers la solution gravitaire. » En juin 2020, le maître d’ouvrage, après avoir validé le financement du projet, a donné l’ordre de démarrage à un groupement piloté par Bouygues Travaux Publics, aux côtés de Saipem et Boskalis, pour assurer la conception, la construction et l’installation de ces fondations.
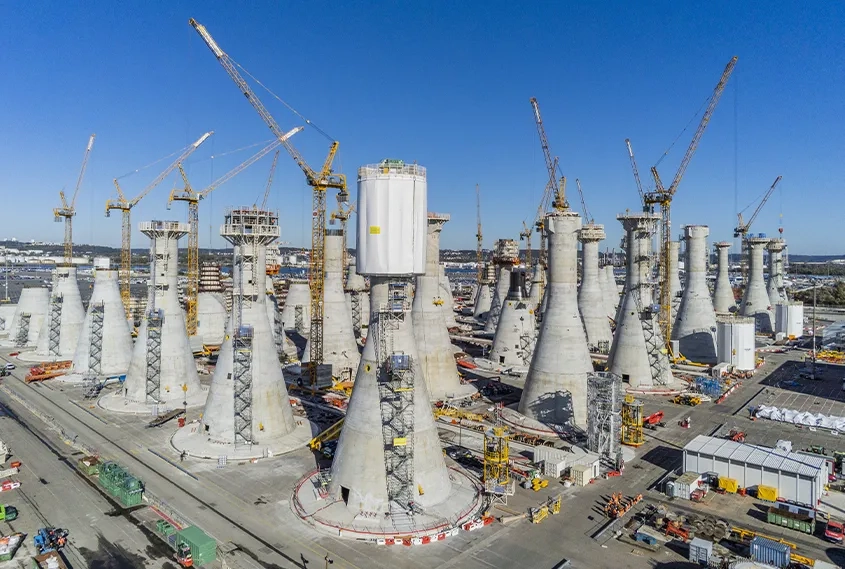
Une conception guidée par les charges de service et provisoires
L’élaboration de leur design précis pouvait commencer. De multiples paramètres entraient en ligne de compte : les charges de service, comme la résistance au vent et à la houle, ou la résistance à l’accostage des navires de transfert de personnel, mais aussi les charges provisoires, liées à la méthodologie d’installation et aux différentes phases de levage – levage à terre par le bas de la structure, transport sur des chariots multi-roues, et levage en mer par le haut de la structure. « La somme de ces contraintes a conduit à un design commun à toutes les fondations », synthétise Jean-Claude Gandolfini, directeur technique du projet pour le groupement. Soit une structure en béton armé de près de 5 000 t disposant d’un large fût conique en partie basse – le radier circulaire présentant un diamètre de 31 m – s’effilant progressivement pour devenir cylindrique en partie haute, la hauteur de l’ensemble s’échelonnant entre 48 et 54 m en fonction de la bathymétrie. « Le fût est renforcé par l’intermédiaire de 18 câbles de précontrainte », précise Jean-Claude Gandolfini.
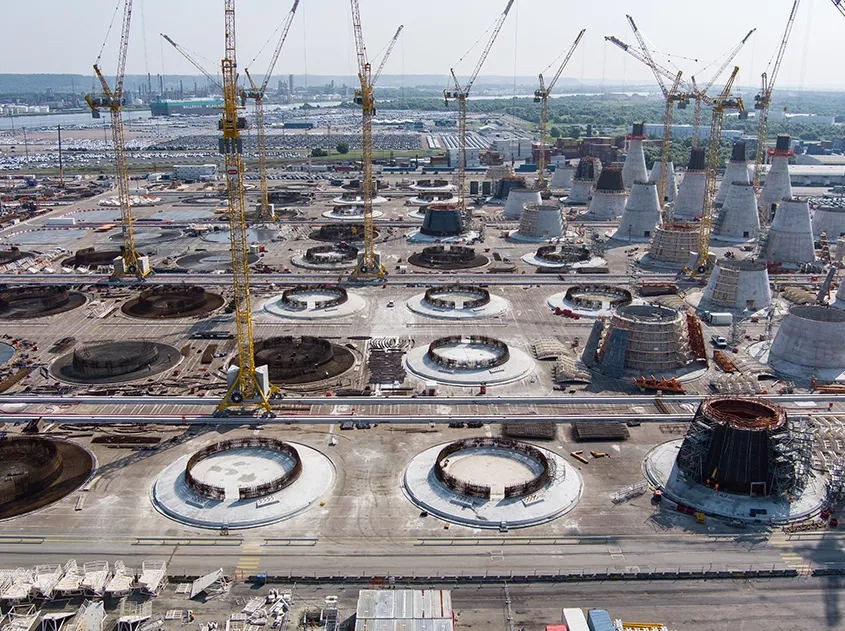
Une usine de production à ciel ouvert
Pour le chantier de Génie Civil – l’un des plus importants de France – Bouygues Travaux Publics a fait le choix de l’efficacité. Le grand port maritime du Havre a ainsi mis à disposition du groupement une enceinte bord à quai de 27 ha, suffisamment vaste pour pouvoir ériger toutes les fondations en parallèle. Cet atelier industriel à ciel ouvert comprenait quatre lignes de production, chacune d’elles disposant de quatre grues à tour de forte capacité à flèche relevable pour alimenter les différents postes, et de jeux complets de coffrages intérieurs et extérieurs. « Afin d’optimiser l’utilisation et la rotation des matériels, les embases étaient réalisées en décalage de phases », illustre Claire Couderc, ingénieur méthodes chez Bouygues Travaux Publics. Ainsi, en février 2022, alors que le Génie Civil d’une première embase était achevé, les 70 autres étaient toujours en cours de construction, à différentes étapes de leur achèvement.
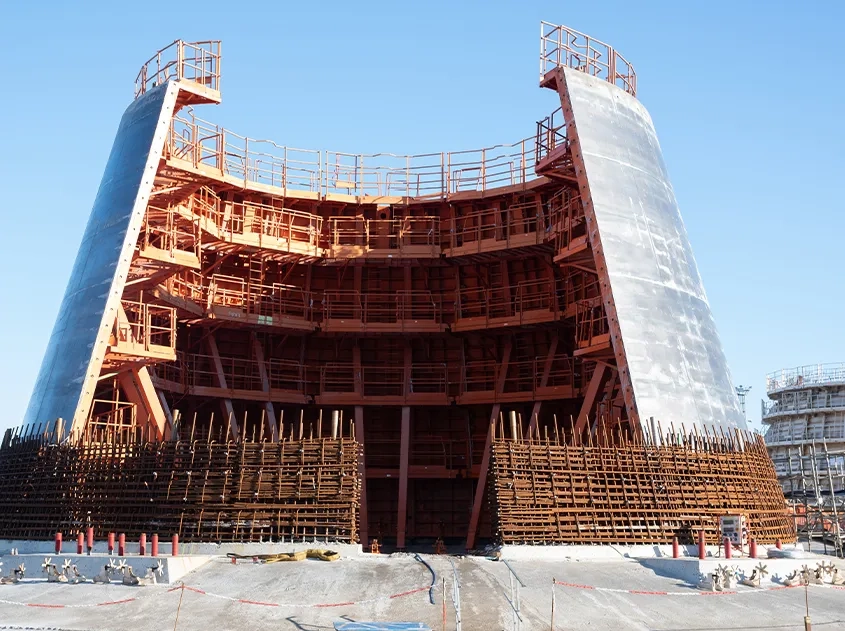
Une dizaine d’étapes de construction pour chaque fondation
Toutes suivaient néanmoins une unique méthodologie de construction, comprenant une dizaine d’étapes. Après le coulage des 800 m3 de béton du radier, les parties coniques du fût étaient réalisées en deux levées successives de 11 m, à l’aide de coffrages façonnés selon la forme de la structure. Les cages d’armatures, préfabriquées sur une aire dédiée de 2,5 ha, étaient acheminées sur place par semi-remorque et mises en place à la grue. « À chaque fin de coulage, nous démontions successivement les peaux intérieures et extérieures des coffrages pour les transférer à l’atelier suivant, selon des périodes de rotation de dix jours en moyenne », précise Claire Couderc. Suivait la zone de transition entre la partie conique et la partie cylindrique du fût. « Cette levée était particulièrement compliquée à couler du fait de la géométrie complexe des coffrages. » La cinquième étape était celle du coulage de la partie cylindrique des fûts, grâce à un coffrage autogrimpant. « Ce matériel spécifique nous permettait de limiter l’utilisation de la grue, le coffrage s’élevant le long du fût grâce à ses propres vérins », poursuit David Borel, ingénieur méthodes chez Bouygues Travaux Publics.
Des bétons résistant aux agressions des chlorures marins
Les 122 000 m3 de béton de structure ont été réalisés avec deux formulations se distinguant par leur classe d’exposition aux risques de corrosion par les chlorures marins. Les bétons immergés sont ainsi de classe XS2 et les bétons émergés de classe XS3. « Les essais sur maquette ont montré que les embruns pouvaient atteindre le sommet des fûts. La classe XS3 a été retenue sur toute la hauteur émergée, alors qu’elle est habituellement réservée aux zones de marnage », précise Claire Couderc. Les bétons, acheminés depuis deux centrales situées à 7 km du chantier, ont été mis en œuvre par pompage, hormis pour les parties hautes de fût et les têtes de couronnement, coulés à la benne.
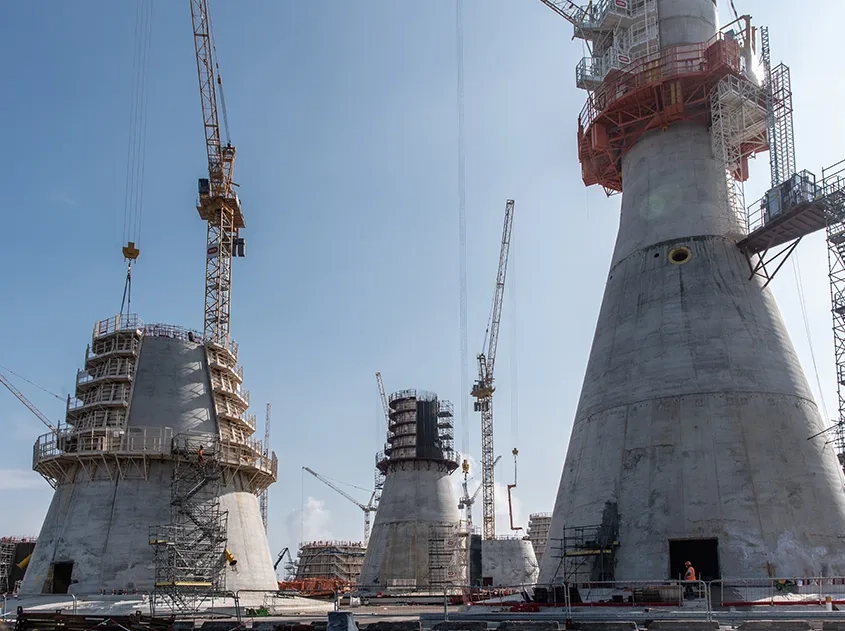
La délicate tête de couronnement, contrôlée au millimètre près
La sixième étape était peut-être la plus complexe à mener à bien. À l’interface entre le sommet du fût et la base du mât métallique des éoliennes, la tête de couronnement intégrait tout à la fois les ancrages hauts des 18 câbles de précontrainte, les 24 tiges de levage hautes et les 108 tiges verticales de fixation des mâts. « Dans cette zone très dense, l’installation des tiges de fixation dans les cages d’armatures devait être réalisée au millimètre près, raison pour laquelle nous effectuions des contrôles par photogrammétrie, une technique permettant de valider précisément leur positionnement », détaille David Borel. Une fois cette délicate opération menée à bien, restait à tendre les câbles de précontrainte, à peindre en jaune – couleur conforme aux règles de signalisation – le fût sur 13,5 m de haut, à installer au niveau de la tête de couronnement les plateformes définitives de maintenance, aux planchers constitués de dalles préfabriquées en béton armé, puis enfin de finaliser la pose des structures métalliques et le câblage des équipements électriques de chaque fondation.
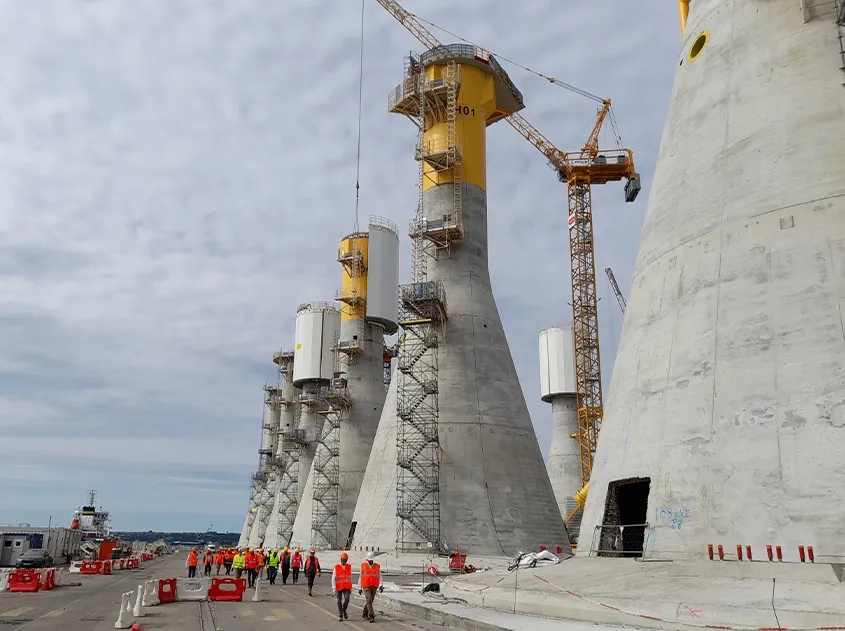
5 000 t délicatement soulevées, transportées en mer puis descendues dans le fond marin
Alors que le chantier de Génie Civil s’est achevé courant de l’été 2022, les opérations d’équipement des fondations gravitaires sont en cours et le transport et l’installation en mer prendront le relais à l’été 2022. Chaque fondation sera d’abord soulevée à 1,5 m du sol par deux portiques positionnés de part et d’autre de celle-ci. Ceux-ci la déposeront délicatement sur des chariots multi-roues, qui la transporteront sur une barge spéciale postée à quai, remorquée jusqu’au site du parc éolien au large de Fécamp.
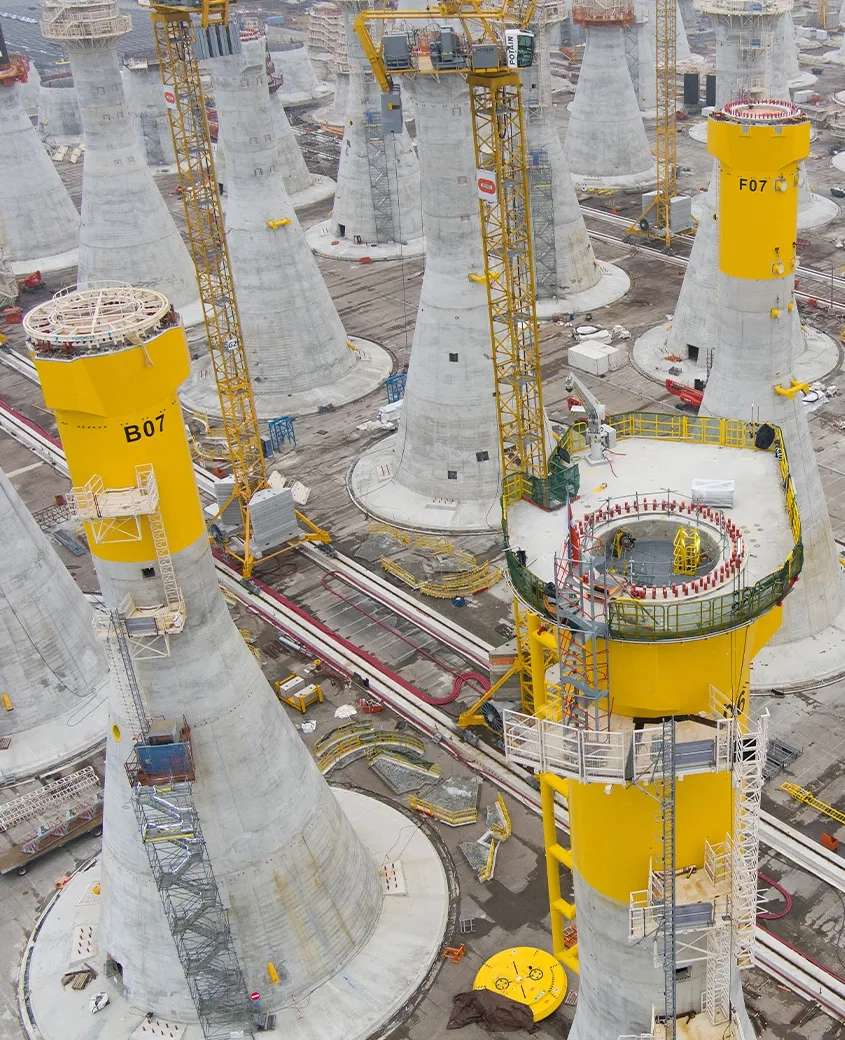
La barge rejoindra alors un Heavy Lift Vessel qui sera chargé de saisir la tête de chaque fondation depuis la barge pour la descendre doucement entre 30 et 40 m de fond jusqu’à son emplacement final, l’eau s’engouffrant dans la structure par l’intermédiaire d’ouvertures ménagées sous le radier. Une fois posé sur son lit de gravier préalablement nivelé, et muni de sa protection anti-affouillement, le volume conique de la fondation sera rempli par 3 000 m3 de matériaux de ballast. L’embase, lestée de manière optimale, sera alors fin prête pour accueillir le mât de l’éolienne et assurer sa stabilité pour des décennies.
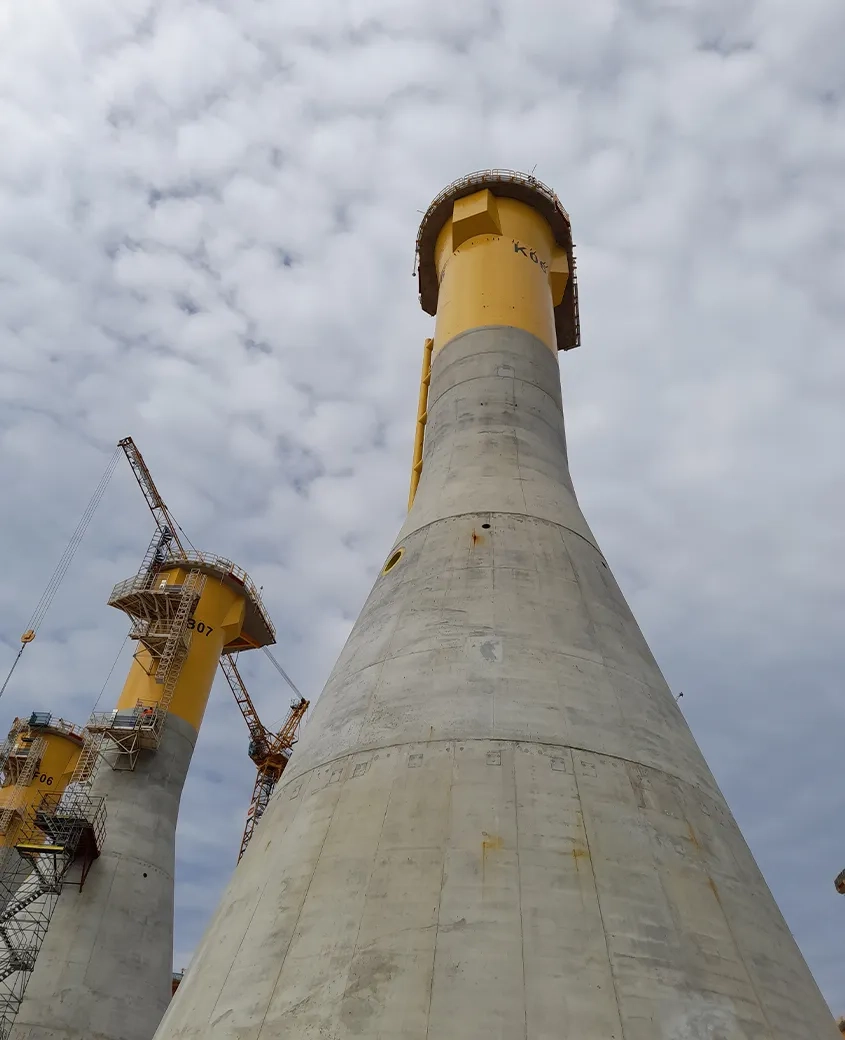
Localiser la réalisation
Fiche technique
Reportage photos : © Parc éolien en mer de Fécamp – Laurent Critot ; Nedim Imre ; Marie Berneval
- Maître d’ouvrage : EDF Renouvelables/Enbridge Inc & CPP Investments/WPD Offshore
- Conception, construction et installation des fondations : groupement Bouygues Travaux Publics, Saipem et Boskalis
- Fournisseur ciment et béton : LafargeHolcim
- Coût de l’investissement : 2 Mds€, pour le projet parc éolien en mer de Fécamp.
Chiffres clés
- Fondations gravitaires : 71
- Béton structurel : 122 000 m3
- Pour chaque fondation (hors ballast) : 5 000 t
- Armatures : 32 000 t
- Armatures de précontrainte : 1 600 t
COMMENTAIRES
3 COMMENTAIRES