Un viaduc conçu pour affronter les cyclones
L’île de la Réunion, son volcan, ses randonnées nature et… ses ponts ! Après la route des Tamarins, le viaduc du Littoral vient compléter cette véritable vitrine du savoir-faire français en termes d’ouvrages d’art.
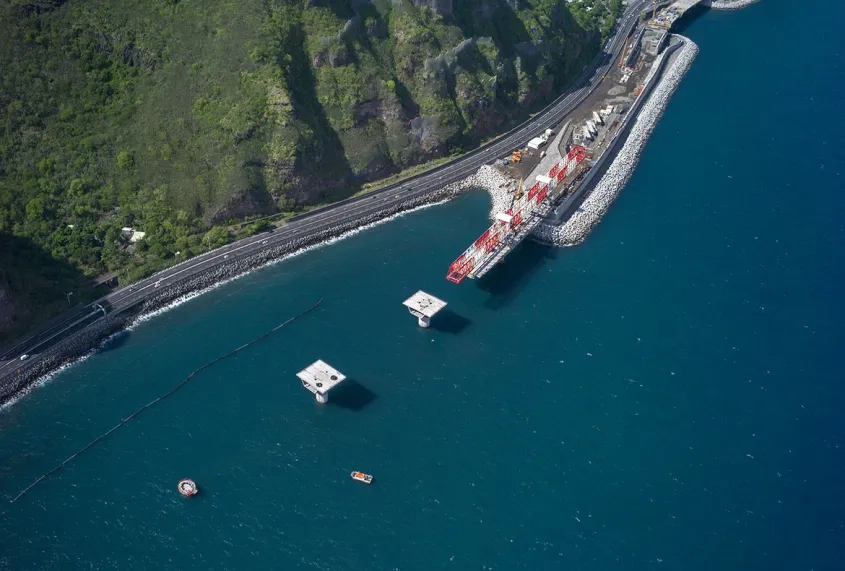
Les plus de 60 000 automobilistes qui la parcourent chaque jour l’empruntent avec angoisse. Axe routier majeur de l’île de la Réunion, reliant Saint-Denis à La Possession, l’actuelle route du littoral est menacée à tout instant de voir s’effondrer sur elle un pan de la falaise qui la surplombe. Les nombreux dispositifs anti-chutes de pierres installés au fil des ans ont contribué à contenir les éboulements mais n’ont jamais réussi à les maîtriser totalement. Et ceux-ci restent fréquents et malheureusement parfois mortels.
La route s’affranchit des éboulements et des cyclones
Pour sécuriser totalement le site, les experts qui se sont penchés à son chevet étaient unanimes : le risque d’effondrement n’étant pas maîtrisable, c’était la route qu’il fallait déplacer. Si bien qu’en octobre 2010, un protocole d’accord entre l’État et le maître d’ouvrage, la région Réunion, lançait le projet de construction de la nouvelle route du littoral, en pleine mer. « Des études de trajectographie ont été menées pour dessiner une route suffisamment écartée de la falaise pour que les blocs rocheux, même en rebondissant, ne puissent pas l’atteindre », expose Alain Gagey, directeur du projet pour Egis, maître d’œuvre du viaduc de la nouvelle infrastructure. Il fallait aussi que la route s’élève à un niveau supérieur à celui des houles centennales cycloniques, très puissantes aux abords de cette île située en plein océan Indien. L’ensemble de ces contraintes a permis de déterminer un tracé et un profil en long : la route sera implantée entre 60 et 300 m du rivage et 20 à 30 m au-dessus du niveau de la mer, « dont un mètre pour tenir compte de l’élévation à venir liée au réchauffement climatique », précise Alain Gagey.
Digues ou viaducs ?
Restait à décider si la nouvelle route s’appuierait sur des digues ou des viaducs. Les considérations techniques (construction et exploitation) et socio-économiques amenèrent le maître d’ouvrage à opter pour une infrastructure mixte. Longue de 12,3 km, l’ample chaussée (2 x 2 voies routières, 2 voies pour un transport en commun en site propre – bus ou tram – et 1 voie vélos) comprend finalement 6,7 km de sections sur digues et 5,6 km sur viaducs. Digues ou viaducs, les ouvrages construits sont ceux de tous les records. Les digues géantes, hautes de 25 m et larges de 100 m, sont dimensionnées pour absorber l’énergie cinétique de la houle. Elles sont constituées d’une série de dispositifs de protection, dont un mur chasse-mer et une carapace externe anti-houle constituée de 38 500 blocs préfabriqués en béton à protubérances tronconiques (des accropodes) et 4,2 millions de m3 d’enrochements. Les viaducs, eux, sont au nombre de deux : le viaduc de la Grande Chaloupe (240 m de long) et le viaduc du Littoral. Avec ses 5 400 m de long, ce dernier pulvérise le record du plus long viaduc de France, détenu jusqu’ici par le pont de l’île de Ré (2 927 m), lui aussi en site maritime.
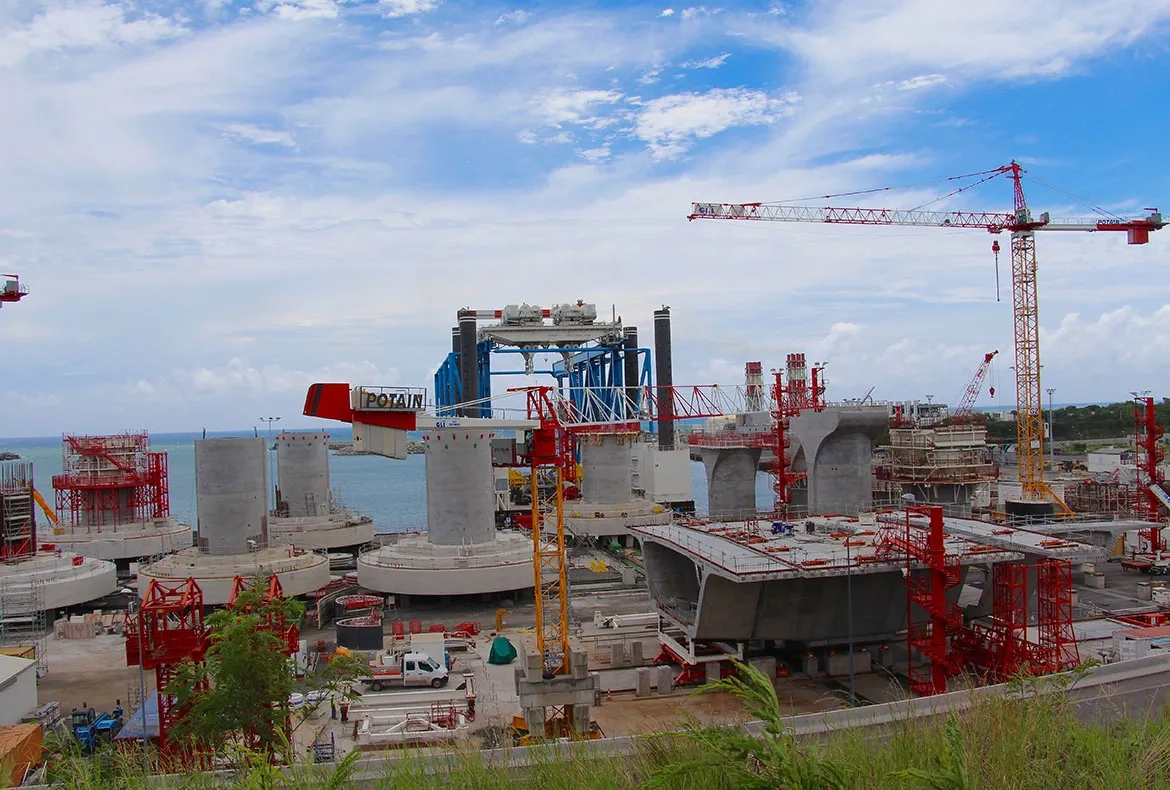
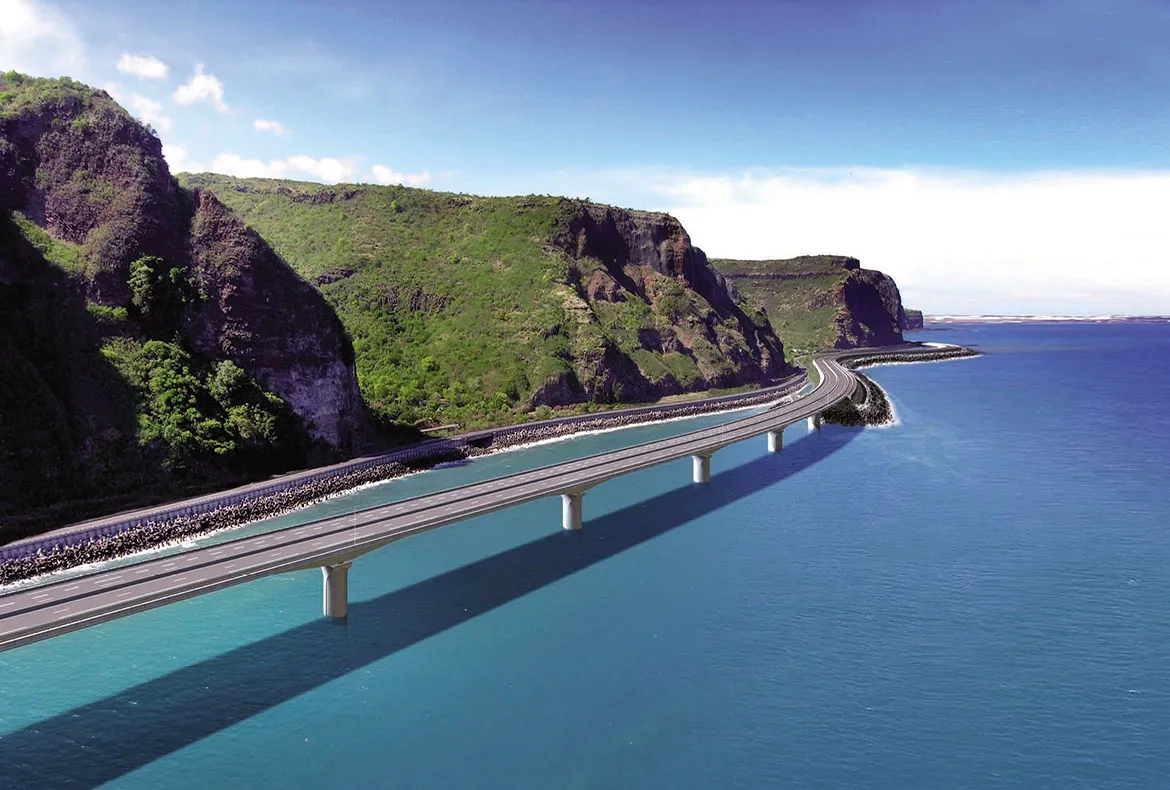
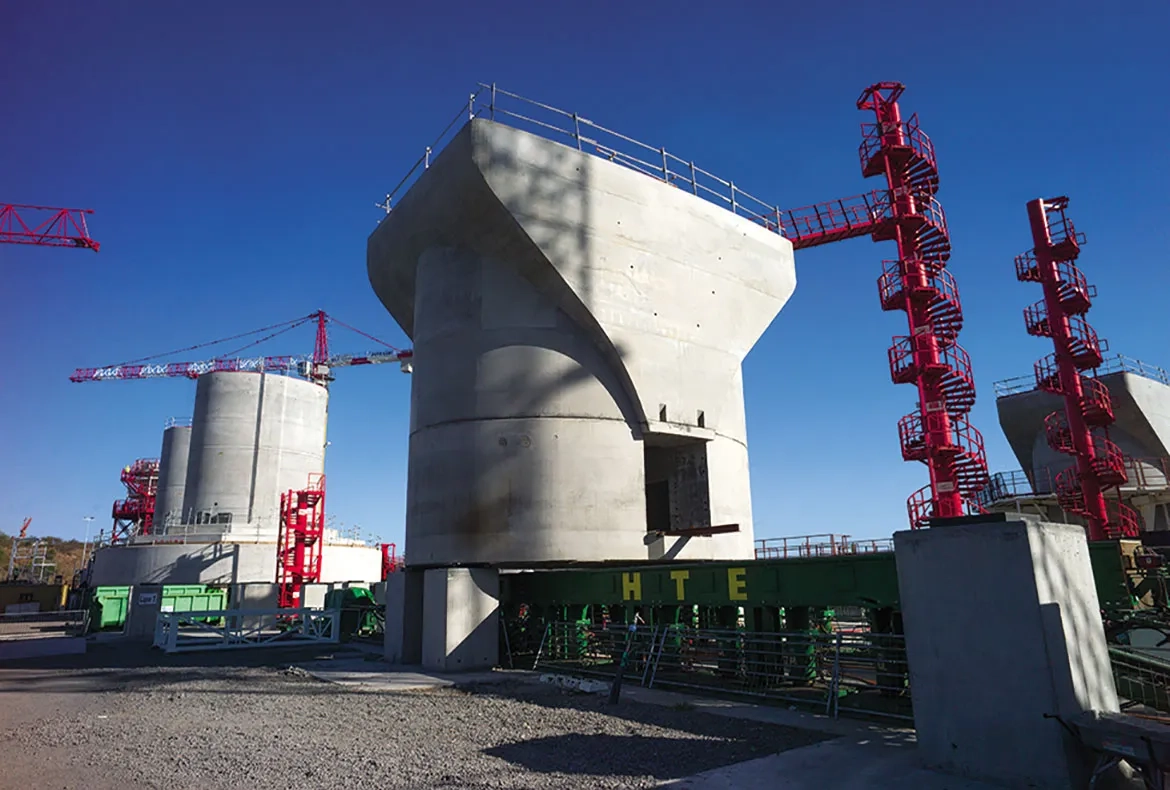
Un viaduc aux dimensions XXL
Cet ouvrage exceptionnel dispose d’un tablier monocaisson extralarge de 29,8 m constitué de l’assemblage de 1 386 voussoirs en béton précontraint formant des travées courantes de 120 m de portée, à inertie variable (entre 7,3 m de hauteur sur pile à 3,8 m à la clé). Le béton comme matériau constitutif du tablier s’est imposé naturellement. « En milieu marin, l’atmosphère saline, combinée aux embruns, a conduit à le préférer à l’acier, dont les coûts d’entretien et de maintenance auraient été beaucoup plus importants », décrit Alain Gagey. Ce tablier imposant, divisé en 7 tronçons indépendants de 770 m, repose sur 50 appuis, dont 48 piles en mer et 2 culées. Dimensionnées pour encaisser la houle et les vents cycloniques, les secousses sismiques et les chocs de bateaux, ces piles de forme elliptique – « une géométrie favorable à la diffusion de l’énergie de la houle », selon Alain Gagey – sont dotées d’immenses semelles de fondation cylindriques (20 à 23 m de diamètre et 4 m d’épaisseur) posées sur le sol marin, à une profondeur variable de 8 à 11 m.
Un ouvrage en mer construit à terre
L’édification de ce géant des mers nécessite des moyens de mise en œuvre à sa mesure. C’est au groupement d’entreprise, qu’est revenue la tâche de les inventer. Tout comme pour l’ouvrage en phase d’exploitation, le premier objectif pour le chantier était de pouvoir s’affranchir au maximum des conditions de houles et de vents cycloniques, qui peuvent souffler à plus de 250 km/h. « Les grands ouvrages maritimes construits dans l’Hexagone bénéficient du plateau continental qui limite ou casse les houles océaniques. Ici, la mer est ouverte, sans protection possible contre la violence de l’océan », expose Francis Guinchard, directeur du projet pour le groupement constructeur.
Alors, pour limiter les interventions en mer, le groupement a fait le choix de fabriquer l’ensemble des éléments structurels de l’ouvrage à terre, y compris les semelles de fondation. Une industrialisation totale rendue possible par une standardisation des fondations superficielles. « Initialement, environ la moitié des piles devait être fondée sur des pieux, détaille Francis Guinchard, mais en menant des analyses supplémentaires sur la nature géologique du sol marin, nous sommes arrivés à la conclusion qu’en terrassant le sol sur 4 à 8 m au droit de chaque pile et en le renforçant dès que nécessaire, il était possible d’étendre les semelles superficielles à la totalité des piles. »
Deux aires de préfabrication ont ainsi été installées à l’extrémité sud du viaduc, sur la commune du Port. L’une, située dans l’enceinte portuaire, est dédiée sur 3 ha à la préfabrication des piles. L’autre, à 1 km en retrait de la zone portuaire, est consacrée sur 9 ha à la réalisation des 1 386 voussoirs. Elle comprend en outre trois centrales à béton (dont une de secours) destinées à fabriquer la totalité des des bétons de l’ouvrage.
Des usines géantes à voussoirs et à piles
Le site de préfabrication des voussoirs s’apparente à une véritable usine. Il dispose de 10 cellules de coffrage : 6 pour la production des 14 géométries de voussoirs courants et 4 pour les voussoirs sur piles et autres voussoirs spéciaux. Les outils coffrants sont desservis par 4 grues à tour et 2 portiques de manutention et de stockage des voussoirs courants. En rythme de croisière, 3 voussoirs sont produits chaque jour. La préfabrication des piles répond elle aussi à un impressionnant processus d’industrialisation.
Pour limiter le poids des colis à transporter en mer, elles sont préfabriquées en deux tronçons : l’embase, constituée de la semelle de fondation et de l’amorce du fût de pile, et la tête de pile, composée quant à elle de la partie supérieure du fût de pile et du chevêtre. Embases et têtes de piles disposent chacune de deux lignes de production sur l’aire de préfabrication. Au cours de leur fabrication, ces pièces massives, d’un poids maximum de 2 000 t pour les têtes de piles et 4 800 t pour les embases, vont être déplacées le long de la ligne de production selon 4 positions successives (3 pour les têtes de piles) constituant autant d’ateliers : préparation des cages d’armatures, bétonnage, finitions, stockage, puis chargement. Sur l’aire de fabrication sont également assemblés des colis spéciaux, les « méga-voussoirs sur pile », qui correspondent à l’amorce du tablier sur chaque pile. Ces pièces de 2 400 t sont constituées de l’assemblage de 7 voussoirs.
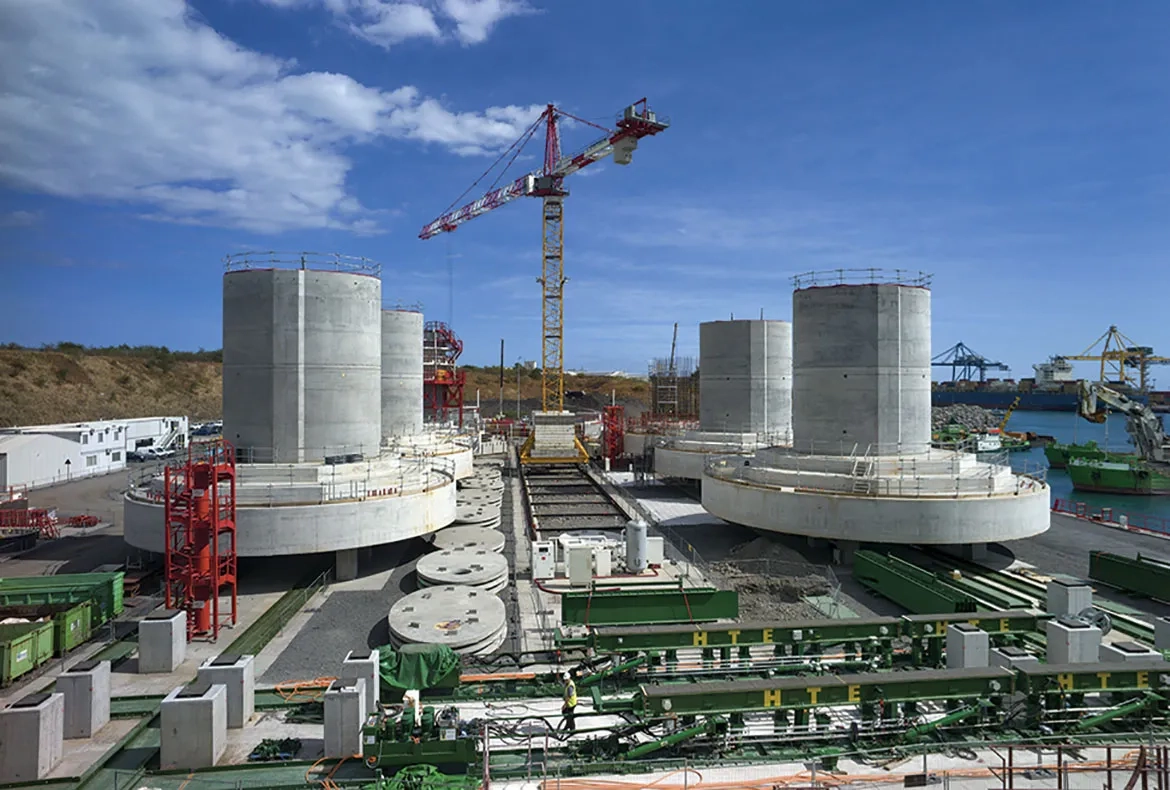
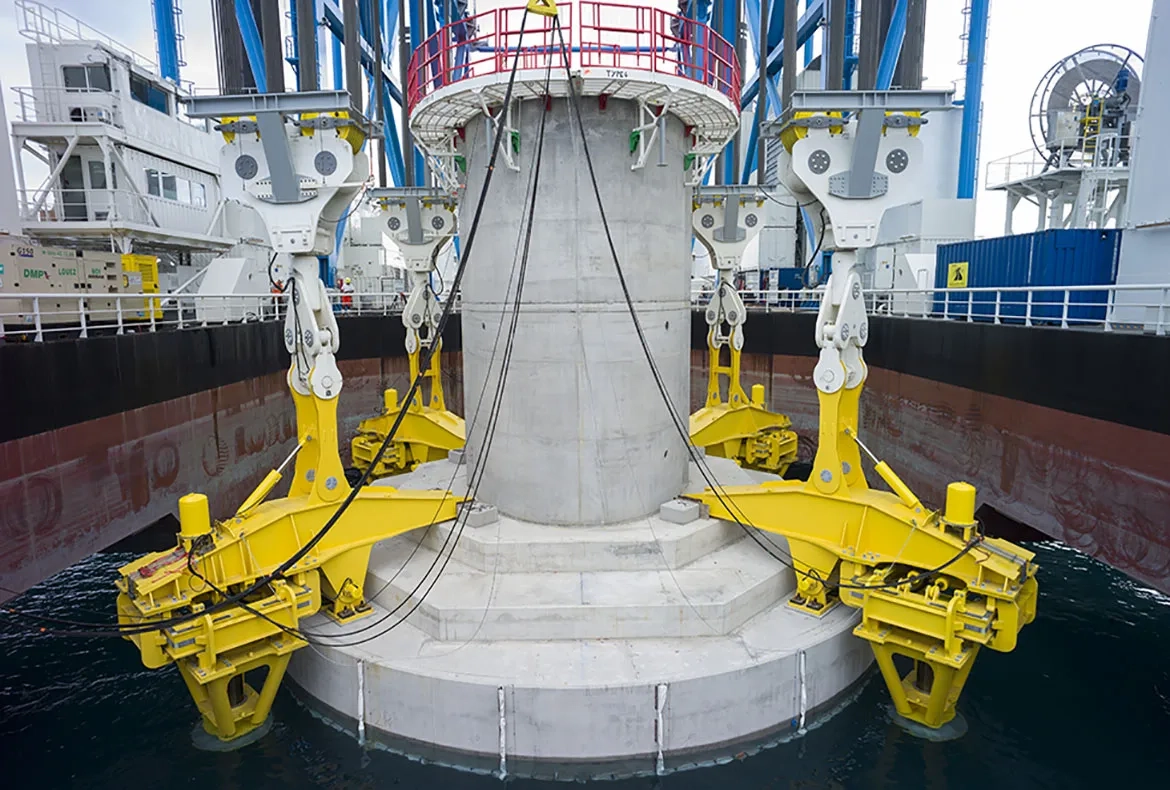
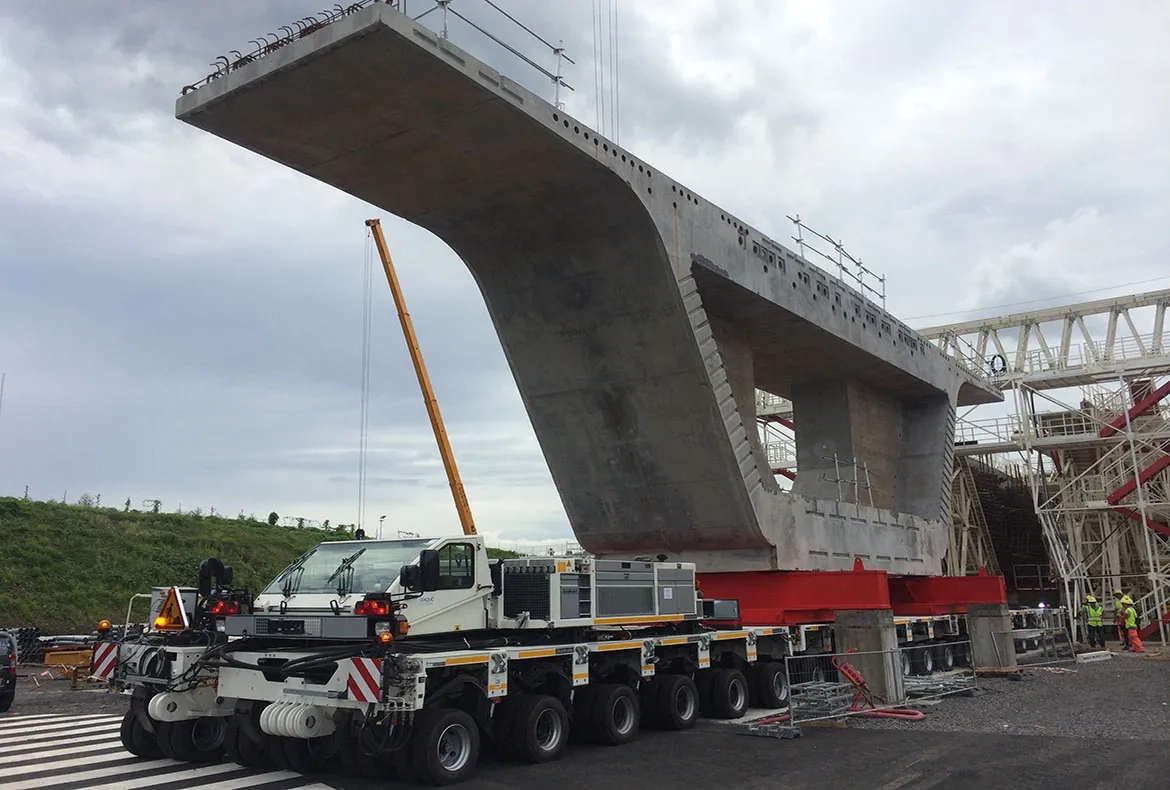
Les piles empruntent la voie maritime...
Une fois la phase de maturation des piles et des voussoirs terminée, ces éléments structurels sont pris en charge pour être acheminés jusqu’à leur lieu de pose. Leurs destins se séparent alors. Les piles sont embarquées directement depuis le quai de l’aire de préfabrication sur une barge géante baptisée Zourite, spécialement fabriquée pour le chantier et disposant d’une capacité de 4 800 t (voir encadré). Pour chaque pile, Zourite effectue deux voyages aux chargements optimisés : un premier pour le transport et la pose de l’embase (jusqu’à 4 800 t), le second pour le transport et la pose de la tête de pile et du mégavoussoir sur pile (d’un poids cumulé atteignant également la capacité maximale de la barge, soit 4 800 t).

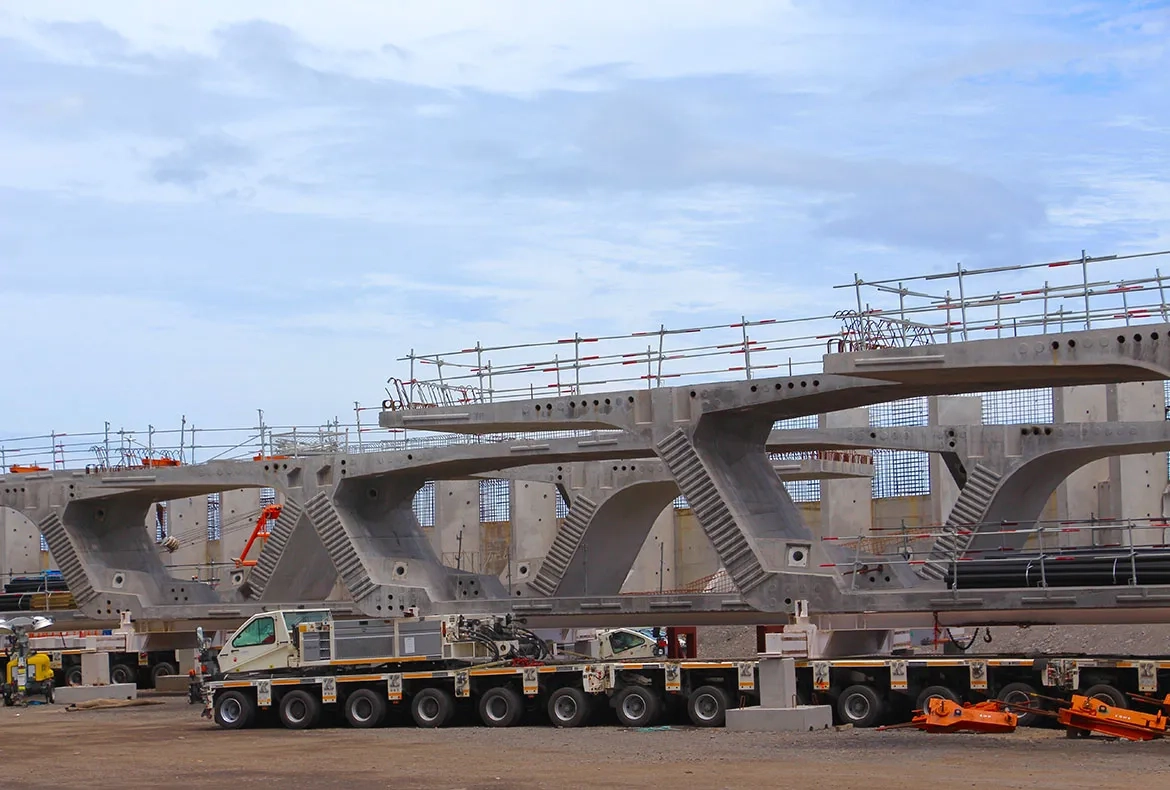
... et les voussoirs la voie terrestre
Contrairement aux piles, les voussoirs sont acheminés par voie terrestre. Des fardiers (plates-formes automotrices) de 35 m de long munis de 216 roues les convoient depuis l’aire de stockage pour les transporter jusqu’à leur lieu de pose, en empruntant de nuit les routes réunionnaises et les portions de tablier déjà construites. Une fois l’extrémité du tablier atteinte, les voussoirs sont alors pris en charge par une poutre de lancement. Cette structure métallique mécanisée de 280 m de long et 28 m de haut permet d’assembler un fléau complet en prenant appui sur les piles déjà en place. Chaque voussoir est d’abord soulevé par un pont roulant qui le transfère au droit de sa position finale. Là, le voussoir est descendu et connecté au voussoir précédent. Le tablier est ainsi construit par encorbellements successifs de part et d’autre de chaque pile. Une fois le fléau posé et clavé au fléau précédent, la poutre de lancement est avancée jusqu’à sa position suivante, et le cycle recommence.
Aires de préfabrication s’étendant sur près de 12 ha, barge géante, poutre de lancement XXL... les superlatifs sont de mise pour évoquer la chaîne logistique du chantier du viaduc du Littoral. Mais ces moyens étaient indispensables à la tenue des délais du chantier. « L’ensemble a été dimensionné pour atteindre une cadence de deux travées complètes fabriquées, transportées et posées par mois (y compris les piles) », précise Francis Guinchard.
Tout au long du chantier, des mesures concrètes visant à préserver la qualité environnementale du site sont prises. Entre autres dispositions, 6 des piles du viaduc seront équipées de modules préfabriqués en Composite Ciment Verre destinés à accueillir et favoriser la faune sous-marine. La structure « nid d’abeille » de ces récifs artificiels protégera ses habitants des attaques des prédateurs. Une autre mesure veille à préserver la tranquillité des espèces aquatiques. Les travaux sous-marins potentiellement bruyants ne peuvent ainsi pas démarrer tant que l’absence de mammifères marins à proximité n’a pas été confirmée par un contrôle visuel effectué par un ULM.
Le chantier du viaduc, dont l’ordre de service de démarrage a été donné en janvier 2014, devrait être livré en juillet 2018 au bout de 54 mois de travaux. La mise en service de la Nouvelle Route du Littoral (NRL), dépendante de l’avancement du chantier de la digue, est quant à elle toujours prévue à l’horizon 2020.
Chiffres clés
Viaduc : longueur 5 409 m, largeur 29,80 m, élévation de 20 à 30 m au-dessus de la mer
1 386 voussoirs préfabriqués : formant 7 tabliers successifs de 770 m
48 piles en mer
9 300 tonnes de précontrainte
300 000 m3 de béton de structure
Une mégabarge autoélévatrice : de 4 800 t de capacité
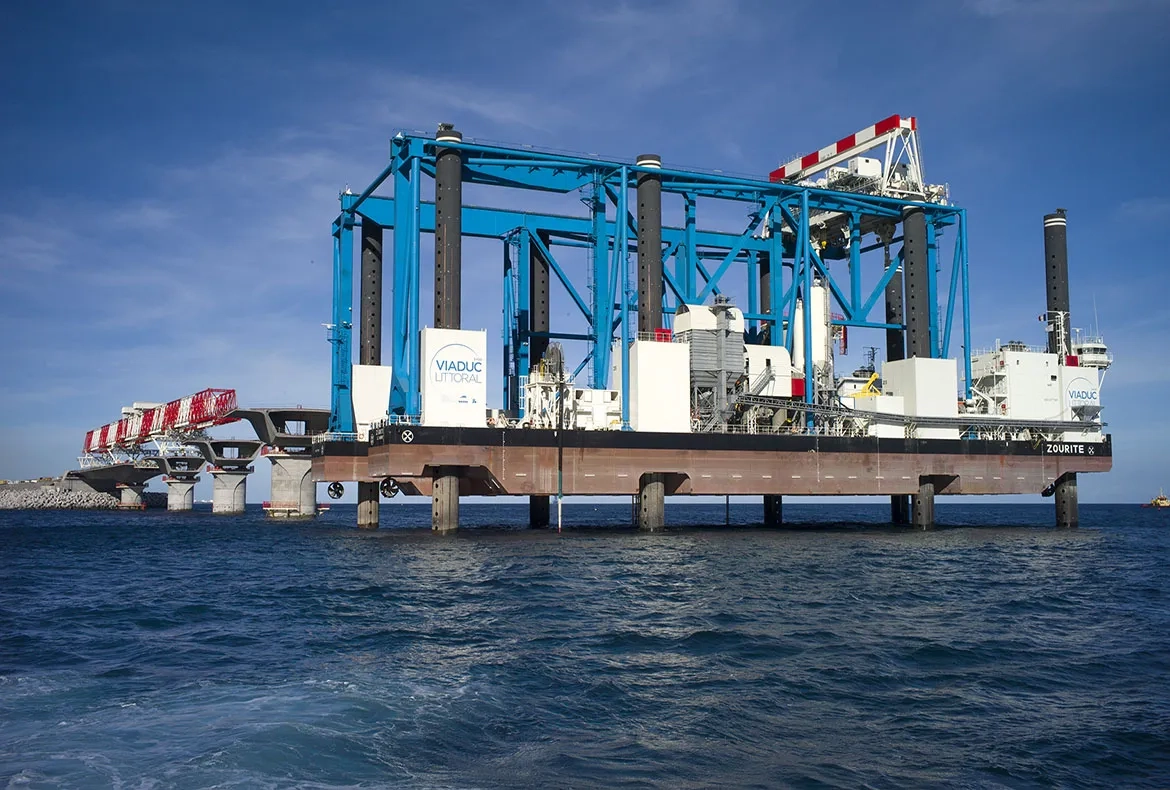
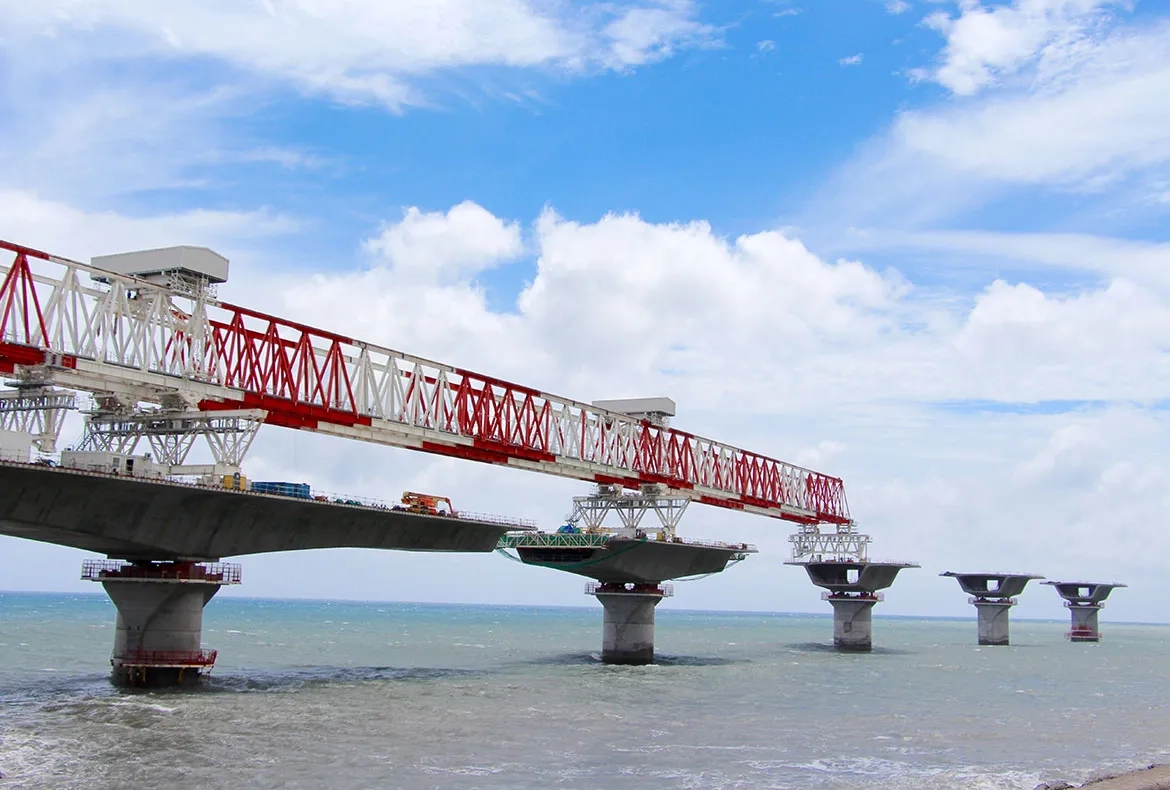
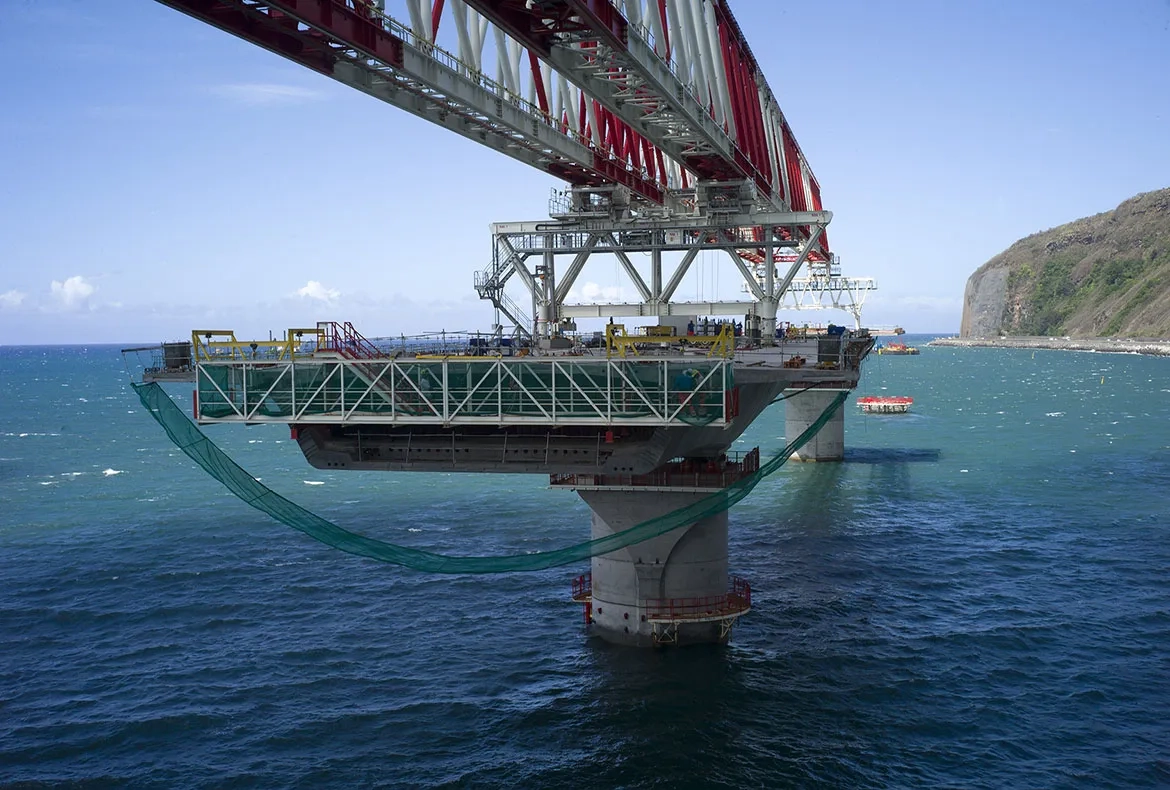
Zourite, la barge pieuvre
Comment transporter des têtes de piles et des embases géantes (jusqu’à 4 800 t) et les poser avec précision dans un océan exposé aux cyclones ? Aucun moyen conventionnel n’étant dimensionné pour réaliser une telle tâche, le groupement d’entreprises a dû concevoir une machine unique en son genre. Zourite, qui signifie « poulpe ou pieuvre » en créole, est une mégabarge flottante automotrice et autoélévatrice. De la dimension d’un terrain de football (longueur 107 m, largeur 44 m) et d’un poids équivalent à celui de deux tours Eiffel, elle a été fabriquée en Pologne avant d’être acheminée à la Réunion, où elle arrive en mai 2016 après un périple de 50 jours. Après l’embarquement des « colis » de béton depuis Le Port, elle navigue jusqu’au lieu d’implantation des piles, pilotée par un équipage de 6 personnes. Elle se hisse alors sur ses 8 « jambes » en acier, ce qui stabilise totalement la plate-forme et permet de travailler dans des conditions équivalentes à celles de la terre ferme.
Un portique de 4 800 t soulève ensuite les éléments de piles, les positionne et les descend avec toute la précision nécessaire. Une centrale à béton embarquée permet de finaliser l’opération en clavant les parties hautes et basses des fûts. En cas de houle cyclonique, le système d’élévation de la barge lui permet de stationner en toute sécurité à plus de 11 m au-dessus du niveau de la mer en se mettant à l’abri au Port. En s’accommodant des conditions cycloniques de la Réunion, Zourite optimise le rendement de l’installation des piles du viaduc et assure la sécurité du personnel.
Maître d’ouvrage : région Réunion – Maître d’œuvre : Egis – Groupement d’entreprises : Vinci Construction Grands Projets (mandataire), Dodin Campenon Bernard (Vinci Construction), Bouygues Travaux Publics (Bouygues Construction), Demathieu Bard Construction – Fournisseur du béton : béton produit par le groupement avec 3 centrales dédiées sur le site de préfabrication des voussoirs Fournisseurs du ciment et des agrégats : Teralta – Coût : 715 M€ TTC, financés par l’État (49 %), la région Réunion (42 %) et des fonds européens (9 %).
COMMENTAIRES
LAISSER UN COMMENTAIRE