Réaménagement du carrefour RD33-RD926-RD6015 au poteau d’Allouville
Le département de la Seine-Maritime et la région Normandie viennent d’achever l’aménagement d’un carrefour giratoire au droit de l’échangeur entre la RD6015 et les RD926 et RD33, au lieu-dit du Poteau d’Allouville, sur la commune d’Allouville-Bellefosse. Cet aménagement sécurisera tous les déplacements des usagers de ce carrefour complexe et confortera la desserte du territoire.
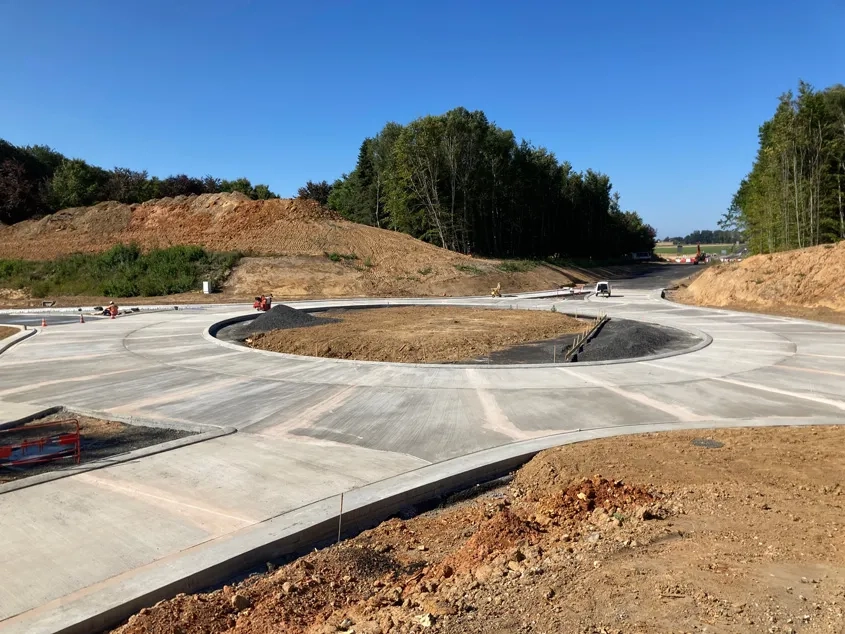
Sur les recommandations du bureau d’études Rincent BTP Services Matériaux, le conseil départemental a retenu, pour cet aménagement, une structure composite constituée d’un revêtement en béton goujonné, mis en œuvre sur une fondation en grave-bitume. Cette structure est réalisée sur une plate-forme support traitée avec un liant hydraulique routier (LHR). Les travaux ont été confiés à Colas, qui a fait appel à EQIOM pour la fourniture du LHR, à Unibéton pour la fourniture du béton et à Socotras pour la réalisation des joints.
Après le carrefour giratoire RD925-RD485 de Dieppe, en service depuis 1995, cette solution durable et 100 % locale a fait son chemin en Seine-Maritime.
Au carrefour de 3 axes départementaux
Le projet se situe au carrefour entre trois axes départementaux fréquentés :
• La RD6015, route structurante de 1re catégorie, relie Rouen au Havre et supporte plus de 11 900 véhicules par jour à l’est de l’échangeur, dont 10,8 % de poids lourds, et 9 200 véhicules par jour à l’ouest, dont 10,6 % de poids lourds. C’est également un itinéraire destiné au passage de transports exceptionnels.
• La RD926, route structurante de 1re catégorie, relie la RD6015 à l’A29 et à la Côte d’Albâtre, en traversant de nombreuses communes du plateau de Caux. Elle supporte un trafic de près de 6 800 véhicules par jour, dont 14,7 % de poids lourds. C’est également un itinéraire utilisé par les transports exceptionnels.
• La RD33 dessert la commune d’Allouville-Bellefosse et rejoint l’itinéraire Yvetot-pont de Brotonne. Elle supporte 2 200 véhicules par jour, dont 2 % de poids lourds.
État des lieux : poids lourds et carrefour difficile
De nombreux poids lourds
Le nombre de poids lourds empruntant ce carrefour est particulièrement élevé. Ceux-ci sont issus :
• Du trafic en transit lié à la desserte de la zone industrielle de Port-Jérôme (via RD 6015, RD 926 et A 29) générant d’importants mouvements tournants sur le site ;
• Du trafic local de 200 poids lourds généré quotidiennement par l’activité de l’entreprise Linex, dont 30 % quittent le site et 70 % y accèdent.
Un carrefour difficilement lisible
Avant l’opération, un ouvrage d’art supportait la RD6015 et permettait son passage au-dessus de la RD926 au nord pour rejoindre la RD33 au sud. Les échanges entre la RD6015 et ces deux autres routes départementales se faisaient par des voies dénivelées qui les connectaient, sans avoir les caractéristiques de réelles bretelles. Les intersections, gérées par des successions de panneaux stops ou cédez-le-passage, étaient complexes, peu lisibles et présentaient de mauvaises conditions de visibilité, en particulier la voie de sortie de la RD6015 depuis Le Havre. Ces bretelles et multiples intersections participaient à la mauvaise perception de l’ensemble du carrefour, dont le fonctionnement global était insatisfaisant.
Les intersections, gérées par des successions de panneaux stops ou cédez-le-passage, étaient complexes, peu lisibles et présentaient de mauvaises conditions de visibilité
Une insertion difficile sur l’axe de la RD6015
La voie d’entrée sur la RD6015 en direction du Havre était gérée par un stop. De ce fait, auparavant, l’insertion sur la RD6015 était difficile, notamment pour les nombreux poids lourds qui empruntent quotidiennement l’échangeur.
Un dysfonctionnement sur la bretelle vers Yvetot
Linex, située au sud-est du carrefour, possédait son accès pour poids lourds sur la bretelle d’accès à la RD6015 (vers Yvetot). La présence de véhicules stationnant le long de cette bretelle posait des problèmes de fluidité et de sécurité routière.
Un carrefour accidentogène
Si aucun accident grave n’a été recensé au carrefour des RD6015-RD926-RD33 depuis 2009, de nombreux accidents ont été signalés et deux accidents, en 2018, ont entraîné des blessés légers.
Projet : aménagement de l'échangeur
Ce projet s’est inscrit dans le programme de requalification de la RD6015, itinéraire stratégique de la Seine-Maritime reliant Le Havre à Rouen, qui vise à redonner une fonction locale à l’itinéraire en incitant le trafic de transit à se reporter sur l’itinéraire autoroutier, améliorant ainsi la sécurité et réduisant les nuisances pour les riverains. Cet axe fait également l’objet de la démarche d’aménagement « Route Autrement pour une Conduite Apaisée (RACA) »
Ce projet d’aménagement de l’échangeur, voté par le Département de la Seine-Maritime le 30 septembre 2021, a été défini en concertation avec la commune d’Allouville-Bellefosse et la Communauté de Communes Yvetot Normandie.
Objectifs de l’aménagement
L’échangeur entre la RD6015, la RD926 et la RD33 était peu lisible, avec une insertion difficile sur l’axe de la RD6015, un dysfonctionnement sur la bretelle qui mène vers Yvetot et un carrefour accidentogène. « Simplifier la géométrie de l’ouvrage, améliorer la lisibilité de la signalisation et sécuriser ce carrefour pour tous les usagers, tels étaient les souhaits du conseil départemental de la Seine-Maritime », commente Marylène Redouani, chef du service Études et travaux de Rouen à la direction des routes du conseil départemental de la Seine-Maritime.
Le projet d’aménagement de ce carrefour devait donc permettre de :
• Garantir de bonnes conditions d’échange aux nombreux usagers, dont les poids lourds qui empruntent quotidiennement ce carrefour ;
• Simplifier et sécuriser les échanges entre ces trois routes départementales et améliorer les conditions d’accès à l’entreprise Linex ;
• Contribuer à la cohérence du parti d’aménagement de l’itinéraire de la RD6015 en faveur d’une conduite apaisée ;
• Avoir une durabilité la plus longue possible (vingt ans au minimum) ;
• Limiter l’impact sur l’environnement.
En 2021, pour répondre à ce besoin de simplification et de sécurisation, le conseil départemental de la Seine-Maritime a lancé des études : plusieurs solutions d’aménagement du carrefour au droit de l’échangeur ont été examinées pour en retenir deux répondant le mieux aux objectifs du projet :
• Un double giratoire au pied de l’échangeur ;
• Un giratoire central à la place du pont.
La comparaison des deux solutions, selon différents critères, a conduit le Département à retenir celle d’un giratoire central à l’emplacement du passage supérieur de la RD6015 sur la RD926.
« Le département de la Seine-Maritime a étudié plusieurs solutions d’aménagement afin d’optimiser le fonctionnement actuel de l’échangeur. La comparaison des différentes solutions nous a conduits à retenir celle d’un giratoire central à l’emplacement du passage supérieur de la RD6015 sur la RD926. Cette solution permet de répondre au mieux au parti d’aménagement de la RD6015 et d’être la plus avantageuse », ajoute Marylène Redouani.
En 2018 et 2019, le projet d’aménagement a été mis à l’étude et les différentes solutions d’aménagement pressenties ont été présentées au fur et à mesure au comité de pilotage constitué par le conseil départemental et les collectivités locales concernées. « Cela faisait un moment que les élus locaux et le Département souhaitaient améliorer les conditions de circulation au niveau de l’échangeur », commente Gaëlle Benoît, adjointe au chef du service Études et travaux de Rouen à la direction des routes du conseil départemental de Seine-Maritime.
« Le département de la Seine-Maritime a étudié plusieurs solutions d’aménagement afin d’optimiser le fonctionnement actuel de l’échangeur. La comparaison des différentes solutions nous a conduits à retenir celle d’un giratoire central à l’emplacement du passage supérieur de la RD6015 sur la RD926 »
Conception
Description de la géométrie retenue
Le carrefour giratoire est construit à la place de l’ouvrage d’art. Sa chaussée se situe à environ 1,80 m au-dessus de la chaussée actuelle de la RD926. Les quatre branches axées sur le giratoire remplacent les nombreuses intersections complexes et peu lisibles du carrefour existant. Les échanges entre la RD6015 et les RD926 et RD33 ne se font plus par des voies dénivelées, mais bel et bien dans le même plan. L’actuelle voie d’accès vers la RD6015, en direction d’Yvetot, est devenue une voie privée pour l’entrée de Linex, réglant ainsi les difficultés liées au stationnement de poids lourds le long de la voirie. Cette solution a entraîné la réalisation d’importants travaux de remblai afin de mettre au même niveau le giratoire et ses quatre bretelles d’accès.
Le carrefour giratoire a un rayon interne de 12 m et un rayon externe de 20 m. Son îlot central est équipé de surlargeurs franchissables par les poids lourds pour favoriser le passage des transports exceptionnels. Afin de faciliter l’évacuation des eaux pluviales, l’anneau du carrefour giratoire est conçu avec un dévers unique de 1,5 %, orienté vers les bordures extérieures où les eaux pluviales sont récupérées et traitées. La RD6015 est aménagée avec une chaussée de 6,50 m de large, avec une voie dans chaque sens, et bordée de part et d’autre par des bandes multifonctionnelles de 1,50 m de large. Il y a quatre bretelles d’accès en béton d’une longueur de 25 m. Chaque bretelle d’accès est équipée d’une dalle de transition positionnée entre la structure composite et la structure bitumineuse des routes départementales.
Principes d’intégration dans l’environnement
Une étude faune-flore a été lancée en 2020 pour évaluer la qualité écologique du site. Elle a notamment révélé la présence de potentiels arbres-gîtes pour les chiroptères et la fréquentation importante d’avifaune nicheuse. Le phasage de l’opération a été conçu pour limiter au mieux les impacts sur ces espèces pendant le chantier. Les études d’assainissement ont conduit à récupérer et à traiter l’ensemble des eaux de chaussée du giratoire. Un bassin a été réalisé pour traiter les eaux routières avant leur rejet régulé dans le milieu naturel. La commune d’Allouville-Bellefosse n’ayant pas souhaité d’aménagement paysager spécifique, l’îlot central du giratoire a été simplement enherbé. Les bretelles déconstruites ainsi que les espaces dégagés dans le cadre du projet sont revégétalisés dans une logique de gain de biodiversité.
Choix du matériau de surface
« À partir du moment où la décision d’aménager l’échangeur a été prise, le département de la Seine-Maritime s’est interrogé sur les matériaux et sur les structures à utiliser », précise Marylène Redouani.
En 2021, pour lever ces interrogations, « le conseil départemental de la Seine-Maritime a fait appel au bureau d’études Rincent BTP Services Matériaux pour trouver un concept et une structure de chaussée adaptés à ce projet ainsi qu’une étude de dimensionnement du carrefour giratoire et des bretelles d’accès », ajoute Marylène Redouani.
Pour un carrefour giratoire dont le trafic de poids lourds est élevé, il était impératif de rechercher un matériau de revêtement de chaussée susceptible de :
• Résister durablement à la canalisation des charges, aux charges lourdes roulant à vitesse lente, aux efforts tangentiels et aux efforts résultant de la force centrifuge (surcharge sur les roues extérieures par suite du déport latéral des charges des véhicules) ;
• En conséquence, réduire les opérations de maintenance ;
• Contribuer à l’amélioration de la sécurité des usagers (changement d’aspect et/ou de couleur pour attirer l’attention du conducteur) ;
• Minimiser ses impacts sur l’environnement (facilité de recyclage ultérieur).
« Compte tenu du niveau de sollicitations, sur le plan technique, le béton l’emporte largement, grâce à son endurance et à sa très grande résistance à l’orniérage », précise Pascal Oger, directeur de Rincent BTP.
« Le conseil départemental de la Seine-Maritime a fait appel au bureau d’études Rincent BTP Services Matériaux pour trouver un concept et une structure de chaussée adaptés à ce projet ainsi qu’une étude de dimensionnement du carrefour giratoire et des bretelles d’accès »
Une solution de mise en site propre du chantier a donc été étudiée, afin de valider la faisabilité d’une chaussée béton. La transformation de l’échangeur en « grand giratoire losange » préalablement aux travaux, en réaménageant les carrefours existants, a permis de maintenir l’ensemble des circulations et des échanges, tout en offrant de bonnes conditions de réalisation du futur giratoire.
C’est ainsi que pour le carrefour giratoire de l’échangeur du Poteau d’Allouville-Bellefosse, le conseil départemental, maître d’ouvrage, et Rincent BTP, maître d’œuvre, ont pu faire le choix du béton comme matériau de surface.
« Le béton est incontournable sur ce type d’ouvrage. Par sa résistance au poinçonnement et aux agressions chimiques causées par les chutes accidentelles de kérosène, le béton est bien plus approprié qu’une couche de surface en enrobé », commente Pascal Oger.
« Le béton est incontournable sur ce type d’ouvrage. Par sa résistance au poinçonnement et aux agressions chimiques causées par les chutes accidentelles de kérosène, le béton est bien plus approprié qu’une couche de surface en enrobé »
En outre, compte tenu du trafic élevé et des charges lourdes qui allaient circuler sur ce revêtement, Rincent BTP a recommandé un revêtement en béton non armé mais à joints goujonnés de type BC5g. « Nous avons choisi une chaussée en dalles de béton à joints goujonnés, car ce type de revêtement présente une durée de vie très élevée, ce qui – en termes de coût global – est important », poursuit Pascal Oger.
Choix de la chaussée composite comme structure de chaussée
La grande originalité de ce chantier résidait aussi dans le type de structure de chaussée utilisée. En effet, plutôt que de faire appel à une structure traditionnelle en béton (constituée d’un revêtement en béton non armé et à joints goujonnés BC5g et d’une couche de fondation en béton maigre BC3), structure conçue avec un décollement à l’interface entre le revêtement et la fondation, Pascal Oger a décidé d’utiliser en fondation une couche de grave-bitume au lieu du béton maigre. « Cette structure combine les qualités du béton en tant que matériau antiorniérant, les qualités de la grave-bitume en tant que matériau acceptant les déformations sans se rompre et la durabilité du collage observée à l’interface entre le béton et la grave-bitume. Éprouvé depuis vingt ans, ce concept autorise à retenir l’hypothèse d’un semi-collage à l’interface revêtement-fondation, synonyme d’une optimisation de la structure (réduction de l’épaisseur de celle-ci d’environ 25 %) et, par conséquent, d’une réduction de la consommation des matériaux nobles dans la chaussée. Par ailleurs, elle présente l’avantage d’une construction plus rapide », ajoute Pascal Oger.
« Cette structure combine les qualités du béton en tant que matériau antiorniérant, les qualités de la grave-bitume en tant que matériau acceptant les déformations sans se rompre et la durabilité du collage observée à l’interface entre le béton et la grave-bitume »
Choisir de réaliser un giratoire en béton dans ce département ne relève pas de l’aventure, puisque la première référence a été réalisée à Dieppe en 1995, ouvrage en parfait état et qui continue de remplir son rôle aujourd’hui. L’argument de la durabilité, associée à la solidité éprouvée de la structure composite, a conforté le choix de la direction des routes du conseil départemental. « Un carrefour giratoire en béton a sûrement une durée de vie plus longue que celle d’un ouvrage en enrobé. Dans le cas d’un trafic de poids lourds élevé, le choix d’une structure en béton permet à l’exploitant de faire l’économie des travaux d’entretien réguliers durant la période de service », précise, de son côté, Gaëlle Benoît.
« À terme, le béton de ciment nous garantissait une plus grande longévité qu’une solution classique en béton bitumineux. Certes, l’investissement s’est révélé légèrement plus important. Mais nous avons aussi tenu compte du fait que ce carrefour sensible, situé à l’entrée de l’agglomération et au croisement de deux axes fréquentés, ne serait pas affecté par des travaux d’entretien récurrents, tous les six à huit ans, comme avec une solution à base de matériaux bitumineux. Nous avons choisi un dimensionnement qui nous permet en principe de ne pas intervenir sur l’ouvrage avant une vingtaine d’années », argumente Marylène Redouani.
« La solution en béton peut sembler un peu plus chère à première vue mais, en raisonnant en coût global, on est finalement gagnant, car les coûts d’exploitation sont très faibles. De plus, sur le plan de la sécurité, le béton du giratoire, grâce à sa teinte plus claire que le noir de la chaussée des trois routes départementales qui y convergent, permet d’identifier immédiatement le point singulier que constitue le carrefour », ajoute Pascal Oger.
Arase et couche de forme
En dessous des couches de roulement et de fondation et sur toute la surface du carrefour giratoire, la plate-forme support a été conçue avec un complexe arase de terrassement-couche de forme de haut niveau (PF3) avec les matériaux du site, traités avec des dosages et des épaisseurs à déterminer lors des études. Grâce au traitement en place des sols, on a minimisé l’apport de matériaux nobles, d’où un bénéfice écologique certain : moins d’extraction de granulats de carrières ; moins de nuisances dues au transport des granulats en camion. Par ses avantages économiques et environnementaux, qui ne sont plus à démontrer, la technique de traitement des sols en place au LHR se prête parfaitement à ce type de chantier et s’impose d’elle-même. Compte tenu de l’utilisation d’une chaussée composite BC5g/GB3, la plate-forme support devait avoir une portance minimale PF2qs.
Études géotechniques, de traitement et solution retenue
Le contexte géotechnique
Le projet prévoyait d’équilibrer autant que possible les déblais et les remblais en réutilisant sur place les matériaux issus du décaissement de la RD6015 ainsi que les matériaux issus de la démolition de l’ouvrage d’art. Après des analyses géotechniques, les matériaux du site ont été déclarés inappropriés pour un emploi en couche de forme (CDF). Le maître d’œuvre a autorisé l’utilisation, dans le corps des remblais, des matériaux recyclés (déblais excédentaires ou autres) traités aux LHR, la classe mécanique 5 ayant été retenue afin d’élargir le spectre des matériaux possibles. In fine, pour la CDF, l’entreprise a trouvé une solution d’emprunt sur un gisement de sol proche.
Les reconnaissances géotechniques
Le sol du gisement d’emprunt est un limon de classe géotechnique A1, conformément au Guide des terrassements routiers (GTR) et à la norme NF P 11 300 « Classification des sols ».
Les études de traitement
Le matériau limoneux a été approvisionné pour la CDF. Il a fait l’objet d’une série d’essais pour :
• Vérifier l’aptitude du matériau au traitement, conformément à la norme NF P 94 100 ;
• Déterminer les performances mécaniques obtenues par un traitement au LHR.
L’objectif était de trouver un liant adapté au sol afin de garantir à la fois les performances mécaniques visées (résistance mécanique et tenue au gel) et les contraintes spécifiques de mise en œuvre du chantier. Pour cela, une étude géotechnique de niveau 1 a été menée avec l’objectif d’obtenir :
• Une plate-forme support de classe PF3 ;
• Un matériau traité de classe mécanique 5 (zone 4 du diagramme de classification des sols traités).
La solution retenue pour la plate-forme support de chaussée
Les études ont permis de caractériser le matériau traité, de définir les dosages en vue d’atteindre les performances souhaitées et d’établir un dimensionnement de la plate-forme support de chaussée. Sachant que le carrefour giratoire serait construit sur un remblai et que la plate-forme support d’une structure composite doit être de bonne qualité avec une portance au moins égale à PF2qs (80 ≤ EV2 < 120 MPa), le bureau d’études Rincent BTP a proposé une structure composite associée à une plate-forme support de classe PF3 (120 ≤ EV2 < 200 MPa).
Pour atteindre cet objectif, il a été choisi de réaliser le traitement du sol en place en deux couches successives : traitement de l’arase et traitement de la CDF.
Traitement de l’arase
L’arase (en déblais ou en remblais) a été traitée à la chaux (dosage : 1,5 %) sur une épaisseur de 50 cm (zone en déblais) et de 60 cm (zone en remblais) afin, d’une part, d’assécher et de figer le matériau et, d’autre part, d’améliorer sa portance. L’objectif de portance sur l’arase traitée a été fixé à 50 MPa au minimum (arase AR2).
- Objectifs :
• Densification : q3.
- Critères de réception :
• Compacité conforme à densification q3.
• Portance EV2 ≥ 50 MPa.
Traitement de la couche de forme
Au-dessus de l’arase traitée, la CDF est conçue par un traitement du matériau d’emprunt avec un LHR. L’objectif de portance sur la CDF traitée est fixé à PF3. Le matériau est traité au LHR ROC VDS (dosage : 6 %) et sur une épaisseur de 35 cm.
- Objectifs :
• Matériau non gélif (Rtb ≥ 0,25 MPa).
• Densification : q3.
• Matériau de classe mécanique 5 (zone 4).
- Critères de réception :
• Compacité conforme à densification q3.
• Portance : 120 ≤ EV2 < 200 MPa.
• Déflexion : d ≤ 60 /100 mm.
• Déflexion caractéristique à 8 jours mesurée au FWD : 50 /100.
Dimensionnement de la structure composite
Le dimensionnement de la structure a été établi pour un trafic estimé à la mise en service (1 112 PL/j), la qualité du support en place (plate-forme support PF3), la durée de service (vingt ans) et un taux de croissance annuelle du trafic de 1 %. Il s’établit comme suit :
• Revêtement en béton de classe BC5, non armé et à joints goujonnés, de granulométrie 0/20 et d’épaisseur 19 cm ;
• Couche de fondation en grave-bitume GB3, de granulométrie 0/14 et d’épaisseur 10 cm ;
• Enduit bicouche clouté qui assure à la fois la protection de la CDF traitée et le collage à l’interface entre la CDF et la structure de chaussée ;
• Plate-forme support de portance PF3 (120 ≤ EV2 < 200 MPa), constituée d’une arase traitée à la chaux (classe AR2), d’épaisseur 50 cm (zone en déblais) et 60 cm (zone en remblais), surmontée d’une CDF traitée avec le LHR ROC VDS, d’épaisseur 35 cm.
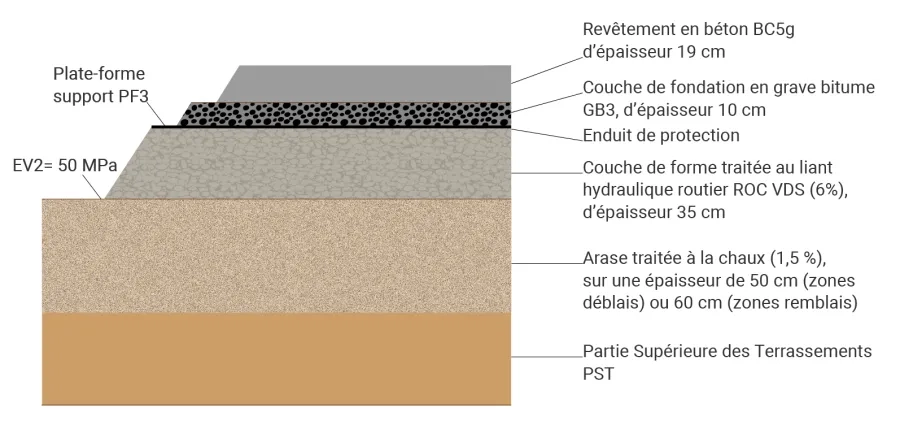
Plan de calepinage des joints
Un des points essentiels d’un projet de giratoire en béton reste l’élaboration du plan de calepinage des joints des dalles.
Ce plan doit faire l’objet d’une validation formelle au regard des dispositions constructives retenues pour la technique avant toute poursuite du projet.
Travaux en 3 phases
Le chantier a été réalisé par deux entreprises : Colas, mandataire pour les terrassements, les travaux relatifs à la grave-bitume et l’assainissement ; et l’agence Colas Grands Travaux, membre du Specbea, pour la mise en œuvre du béton. L’entreprise était particulièrement motivée par la technicité du chantier et par la validation de son savoir-faire sur un tel ouvrage.
Trois phases de travaux à partir du printemps 2022
Le chantier a débuté en 2022 et s’est déroulé en trois étapes afin de limiter la gêne pour les usagers et assurer les échanges durant toute la durée des travaux.
• Phase 1 (printemps 2022) : installation des quatre carrefours provisoires assurant la continuité des échanges durant la construction du giratoire.
• Phase 2 (du printemps à la fin de l’été 2022) : terrassements et réalisation des chaussées du giratoire.
• Phase 3 (de la fin de l’été au mois de décembre 2022) : démontage des carrefours provisoires, mise en service du giratoire et travaux de finition.
Pour les travaux impactant le plus la circulation et nécessitant des déviations, des interventions de nuit ont été réalisées. Par ailleurs, en octobre-novembre 2021, les zones nécessaires à la construction du giratoire ont été déboisées par anticipation pour éviter la période de nidification.
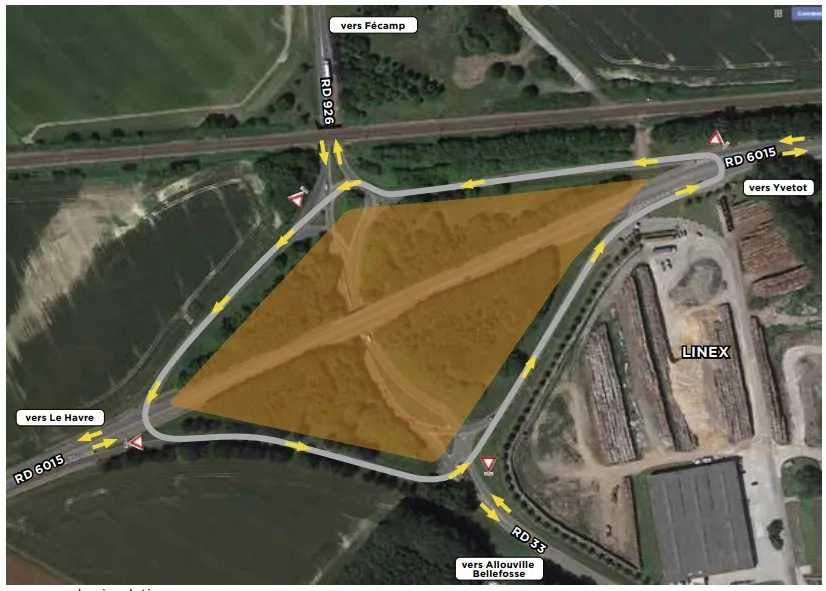
Les différentes opérations
Le chantier a nécessité d’effectuer successivement les opérations suivantes :
• Travaux de terrassement généraux et d’assainissement ;
• Traitement de l’arase à la chaux vive sur 50 cm (zone de déblais) et 60 cm (zone de remblais) ;
• Réalisation de la couche de forme traitée avec le ROC VDS, d’épaisseur 35 cm ;
• Réalisation de l’enduit de protection ;
• Mise en œuvre de la couche de fondation en grave-bitume, d’épaisseur 10 cm ;
• Réalisation des bordures-caniveaux de 25 cm de hauteur, en béton coulé en place ;
• Mise en place des coffrages et des armatures ;
• Réalisation du revêtement en béton non armé et à joints goujonnés BC5g, de granulométrie 0/20 et d’épaisseur 19 cm.
Travaux de terrassement et d’assainissement
Les travaux de terrassement et d’assainissement ont été conduits par Colas. Comme l’objectif du maître d’ouvrage était d’équilibrer autant que possible les déblais et les remblais du site, l’entreprise a procédé aux travaux de démolition de l’ouvrage d’art et au décaissement de la RD6015 et a réutilisé ces derniers matériaux dans la construction du corps du remblai du carrefour giratoire, par couches successives d’épaisseur 35 cm au maximum, nivelées puis compactées.
L’entreprise a ensuite procédé au traitement des matériaux en place afin de leur conférer les performances mécaniques requises. « Le traitement de sol a été réalisé en deux phases. Nous avons d’abord traité à la chaux vive (1,5 %) la partie supérieure des terrassements sur une épaisseur de 50 ou 60 cm (selon les zones), puis rapporté le matériau d’emprunt et traité au LHR ROC VDS (6 %) la couche de forme sur une épaisseur de 35 cm », précise Bruno Barberot, conducteur de travaux en charge des travaux de terrassement de l’entreprise Colas.
Travaux de l’arase traitée à la chaux
Le traitement de la partie supérieure des terrassements a été fait selon la technique habituelle : préparation du sol ; ajustement de l’état hydrique ; épandage du liant ; malaxage ; premier compactage ; réglage puis compactage final. Après la scarification de l’arase, la chaux vive a été épandue à l’aide d’un épandeur asservi Panien PR306-15, à raison de 15 kg/m2. Le malaxage du sol et de la chaux a été réalisé sur une épaisseur de 55 à 65 cm (pour une épaisseur finale, après compactage et découpe, de 50 à 60 cm), à l’aide d’un pulvimixeur Caterpillar RM500. Un réglage avec une niveleuse a ensuite été effectué, puis un compactage à l’aide d’un compacteur VP5 pour garantir l’obtention de la compacité visée.
Travaux de mise en œuvre de la CDF traitée avec un LHR
Une fois effectué le traitement à la chaux, la portance de l’arase s’élevait à 50 MPa au minimum. Ensuite, pour réaliser la CDF, il a fallu, dans un premier temps, acheminer les matériaux d’emprunt, ce qui a été suivi de l’opération de mise en œuvre du matériau sur 40 cm pour une épaisseur finale de 35 cm, afin de tenir compte du compactage et de la recoupe finale. Un préréglage avec une niveleuse asservie a été ensuite réalisé de façon que l’épaisseur soit homogène avant traitement. Cette phase est très importante, car un bon réglage ne peut être garanti que s’il y a une recoupe de la couche après traitement, afin d’éviter le phénomène de feuilletage de surface.
Aucun apport n’est possible dans la phase de réglage. « Une étape clé a été la parfaite humidification du matériau. Pour obtenir une teneur en eau optimale, nous avons pré-humidifié le matériau jusqu’à l’obtention de la teneur optimale en eau et ce préalablement aux opérations de traitement de la couche de forme », explique Bruno Barberot. Le traitement proprement dit a été réalisé en deux opérations successives :
• Un épandage du LHR ROC VDS, à raison de 6 % (soit 40 kg/m2), à la surface du matériau, à l’aide d’un épandeur Panien PR306-15 ;
• Un malaxage à l’aide d’un pulvimixeur moderne Caterpillar RM500. Les derniers ajustements en teneur en eau jusqu’à l’obtention de la teneur optimale se font par une arroseuse-enfouisseuse.
Le matériau a été ensuite remis en forme à l’aide d’une niveleuse. Deux types de compacteurs se sont chargés du matériau traité afin d’atteindre l’objectif q3 fixé : un compacteur monocylindre à bille lisse Dynapac CA402 (pour bien compacter en fond de couche) puis compacteur à pneus Lebrero CNL 824 (pour donner un bel uni). Une niveleuse assistée par GPS a effectué le réglage par recoupe de la couche traitée pour obtenir un résultat au centimètre près. On parvient ainsi à un très bon uni et à un profil en long très régulier.
Enduit de protection
Un enduit de cure bicouche clouté a été appliqué pour, d’une part, protéger la CDF et assurer la bonne prise hydraulique du mélange et, d’autre part, garantir un bon collage à l’interface entre la CDF et la couche de fondation en GB3. À noter que la circulation des véhicules a été neutralisée pendant un délai de 28 jours, pour ne pas rompre la prise hydraulique.
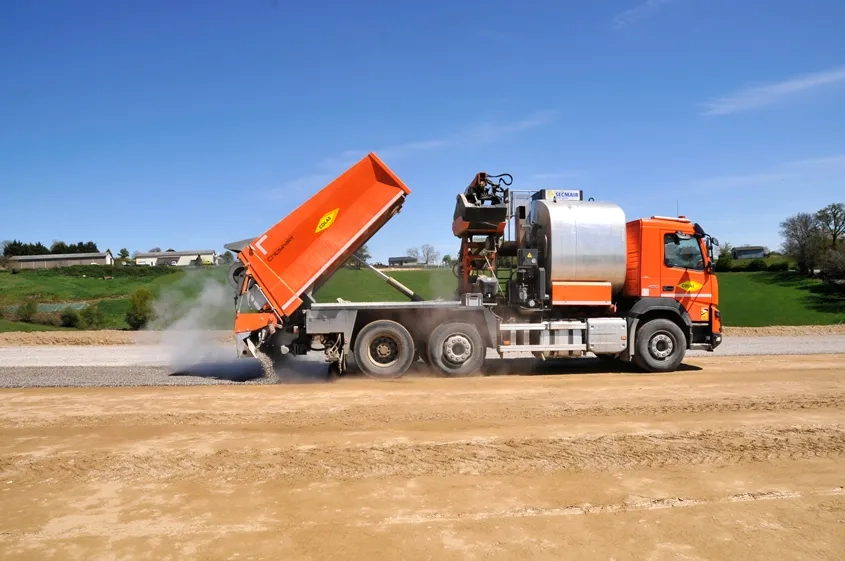
Contrôles
De nombreux contrôles ont été effectués au cours de la réalisation du chantier de terrassement afin de s’assurer de l’obtention des caractéristiques mécaniques visées. Des contrôles de l’épandage des liants (chaux et LHR) à l’aide de la méthode à la bâche et des contrôles de portance ont été réalisés pour l’arase traitée à la chaux vive afin de garantir la portance minimale visée de 50 MPa. Pour la CDF traitée au LHR, la classe de portance a été validée par des contrôles de déflexion au Falling Weight Deflectometer FWD. Cette méthode a été préférée aux mesures de portance in situ, car elle était mieux adaptée aux matériaux traités aux LHR. Pour l’ensemble des couches, la qualité de compactage (q3) a été validée par des essais fréquents de densité en place mesurée à l’aide d’un gamma-densimètre. Au cours de l’ensemble du chantier, des analyses en laboratoire et des contrôles ont été pratiqués quotidiennement afin de maîtriser la teneur en eau des matériaux.
ROC VDS : un liant polyvalent et performant
« Nous avons une large gamme de liants hydrauliques routiers avec une palette d’utilisations étendue à beaucoup de sols différents », commente, de son côté, Jérôme Pincemail, directeur des ventes d’EQIOM 2SG. Dans le cadre spécifique du chantier de l’échangeur du Poteau d’Allouville, Colas a utilisé le ROC VDS pour le traitement du matériau de la CDF. « Ce liant, fabriqué dans notre usine de Dannes, a une excellente réputation et donne pleine satisfaction à ceux qui l’utilisent. Il s’agit d’un liant hydraulique routier à base laitier, polyvalent et à forte activation », ajoute Jérôme Pincemail.
« Ce liant, fabriqué dans notre usine de Dannes, a une excellente réputation et donne pleine satisfaction à ceux qui l’utilisent. Il s’agit d’un liant hydraulique routier à base laitier, polyvalent et à forte activation »
« Environ 300 tonnes ont été nécessaires pour traiter la couche de forme du carrefour giratoire d’Allouville-Bellefosse. Nous avons livré ces 300 tonnes sur une période relativement courte, ce qui a exigé une bonne synchronisation des livraisons et une bonne coordination avec Colas », indique Dominique Leroy, responsable de marché Routes région Nord. « Ces quantités s’expliquent aussi par le fait que le carrefour giratoire est construit sur un remblai et qu’il est amené à supporter tout au long de l’année un trafic poids lourds très intense. Nous visons des portances minimales de 120 MPa pour l’ensemble des 2 000 m2 de plate-forme support de chaussée », précise Bruno Barberot.
« Nous avons livré ces 300 tonnes sur une période relativement courte, ce qui a exigé une bonne synchronisation des livraisons et une bonne coordination avec Colas »
Réalisation de la couche de fondation en GB3
La couche de fondation, constituée de 10 cm de grave-bitume GB3, a été réalisée par Colas à l’aide d’un finisseur et d’un atelier de compactage. L’objectif est d’obtenir une compacité minimale de 92 %, conformément aux exigences de la norme NF EN 13 108-1 « Enrobés bitumineux » et aux spécifications données dans le Catalogue des structures types de chaussées neuves (Sétra-LCPC, 1998). La mise en œuvre de la grave-bitume a été effectuée par bandes de largeur variable, sur une épaisseur de 12 cm puis ramenée à 10 cm par rabotage dans le but d’obtenir :
• Une bonne planéité de la grave-bitume (exigée pour la réalisation d’un revêtement en béton d’épaisseur constante) ;
• Une bonne rugosité (exigée pour l’adhérence entre le béton et la grave-bitume).
Mise en œuvre des bordures-caniveaux en béton coulé en place
L’entreprise Colas a réalisé, sur le pourtour de l’îlot central, sur le pourtour extérieur du carrefour giratoire et sur les îlots de séparation des voies d’accès, des bordures et des bordures-caniveaux en béton coulé en place, dont la hauteur de 25 cm leur donne de la stabilité contre les chocs causés par les pneus des véhicules. « Nous souhaitons que la durabilité des bordures soit en phase avec l’espérance de vie de l’ouvrage en béton », précise Stéphanie Dubuisson, adjointe au chef du service Études et travaux de Rouen à la direction des routes du conseil départemental de Seine-Maritime.
Une machine à coffrages glissants a été employée pour réaliser la bordure intérieure, puis la bordure-caniveau extérieure du carrefour giratoire. « Leur altimétrie est parfaitement contrôlée, ce qui permet de les utiliser comme guides pour le coulage du revêtement en béton. Elles servent également de coffrage, d’où un gain de temps non négligeable », signale Quentin Hognon, conducteur de travaux de l’agence Grands Travaux de Colas.
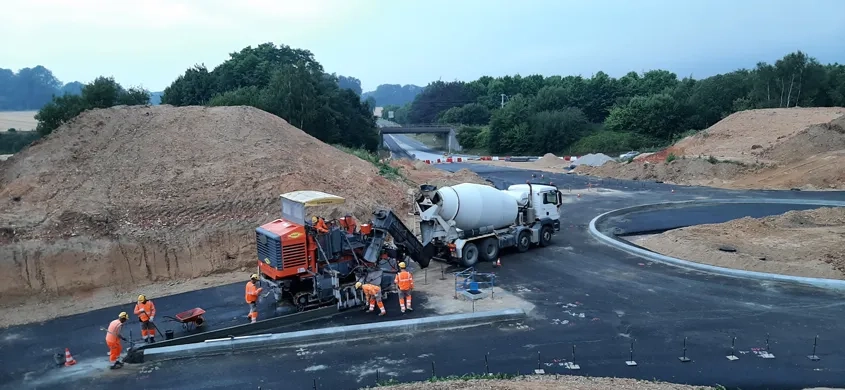
Réalisation du revêtement en béton
« Avant le démarrage des travaux, nous avons remis au conseil départemental, pour validation, un plan précisant l’organisation de la mise en œuvre des revêtements en béton », précise Quentin Hognon. Ce plan définit le phasage ; la mise en place du matériau (sens de bétonnage, longueur et largeur des bandes, etc.) ; la validation du plan de calepinage des joints et l’emplacement des joints de construction et de dilatation. « L’objectif, pour nous, est d’assurer une mise en œuvre continue, de maîtriser les délais d’exécution et de minimiser les joints de construction », ajoute Quentin Hognon.

Fabrication et transport du béton
Le béton a été fabriqué par la société Unibéton à l’unité de production de Barentin 2. Pour les besoins de ce chantier, deux types de bétons ont été spécifiquement formulés et livrés : l’un pour les bordures et les bordures-caniveaux et l’autre pour le revêtement en béton. Il s’agit de bétons dont la composition et la formulation ont été adaptées à l’usage. Ils ont été développés en collaboration avec Colas.
Le béton destiné au revêtement est référencé MANUVIA BC5 (C35/45) XF2 S2.7 MG S3 CL 0.40. Le ciment est : CEM II/A LL 42,5 R PM CP2 RANVILLE.
Le béton a été ensuite acheminé depuis la centrale jusqu’au chantier par camions-toupies, qui ont déversé le béton devant le matériel de mise en œuvre.
Outre le classique autocontrôle quotidien, Unibéton a réalisé six éprouvettes de béton : remises au conseil départemental puis stockées dans des conditions bien définies de température et d’hygrométrie, elles serviront à d’éventuels contrôles des performances mécaniques du béton.
« La fourniture des 488 m3 de béton (400 m3 pour la couche de roulement et 88 m3 pour les bordures et les bordures-caniveaux) s’est étendue sur plusieurs semaines. Le planning de livraison était fixé à la semaine, puis éventuellement ajusté la veille pour le lendemain, selon l’avancement du chantier et les conditions météorologiques. Ce type de chantier, étalé dans le temps, demande une bonne organisation interne et une bonne coordination avec l’entreprise, notamment au niveau des livraisons », explique Frédéric Lieffroy, responsable commercial chez Unibéton.
Mise en œuvre du béton
Après nettoyage de la surface de la couche de grave-bitume – en vue d’obtenir une interface semi-collée entre le revêtement en béton et la fondation en grave-bitume –, le bétonnage a été conduit de façon manuelle, selon le phasage suivant :
• Bétonnage des trois bretelles est, nord et ouest. La bretelle sud, réservée aux approvisionnements du chantier, sera bétonnée à la fin du phasage ;
• Bétonnage de l’anneau intérieur du carrefour giratoire ;
• Bétonnage de l’anneau extérieur ;
• Bétonnage de la bretelle sud.
La mise en œuvre du revêtement en béton comprend plusieurs opérations : réalisation des coffrages ; mise en place des armatures (goujons, fers de liaison, chaînage en bord de dalles) ; bétonnage ; talochage ; traitement de surface ; cure ; exécution des joints de retrait et contrôles.
Réalisation des coffrages
Conformément au phasage du chantier, l’entreprise se doit de réaliser l’anneau du carrefour giratoire en deux temps (en deux anneaux concentriques de 4 m de large chacun). Le coffrage se constitue donc, d’un côté, de la bordure en béton déjà réalisée et, de l’autre côté, d’un coffrage intermédiaire exécuté de façon traditionnelle, à l’aide de planches en bois dont l’altimétrie est déterminée par la mise en place de fils tendus entre les bordures intérieure et extérieure.
Mise en place des armatures (goujons, fers de liaison et chaînage sur les bords de dalles)
L’entreprise a mis en place, au droit de chaque joint de retrait transversal et de chaque joint de dilatation, un système de transfert de charge : celui-ci est constitué de goujons de 25 mm de diamètre et de 45 cm de longueur. Ils sont positionnés à mi-hauteur du revêtement en béton et à cheval sur le joint, à l’aide de paniers, à raison d’un goujon tous les 30 cm.
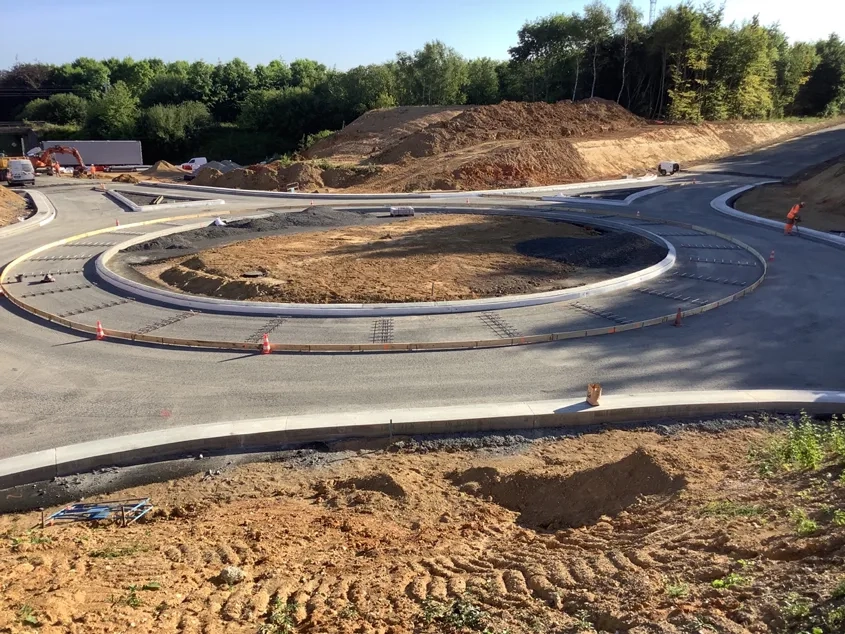
Ces paniers, stockés sur le chantier, seront positionnés avec un espacement bien défini (entre 4 et 5 m) et fixés sur la fondation en grave-bitume au droit des joints, repérés par une marque en dehors de l’emprise de la chaussée, juste à l’avant de la règle vibrante. « Et ce ne sont pas moins de 150 paniers porte-goujons, soit un total de 1 500 goujons, qui ont été ainsi utilisés sur ce chantier », précise Quentin Hognon.
En outre, l’entreprise a équipé le joint de construction longitudinal (entre les deux bandes de l’anneau du carrefour giratoire) de fers de liaison. Ce sont des armatures haute adhérence HA, de 10 mm de diamètre et de 80 cm de longueur. Ils sont disposés à mi-hauteur du revêtement en béton à cheval sur le joint de construction. Placés tous les mètres, ils assurent la couture de ce joint longitudinal de construction qui sera ultérieurement scié et garni par un élastomère à chaud.
Enfin, pour renforcer les extrémités des dalles, des chaînages de section carrée (5 x 5 cm), constitués de 4 barres d’acier haute adhérence de diamètre 12 mm, ont été mis en place par l’entreprise aux endroits les plus sollicités et en particulier sur :
• Les bords de dalles près des joints de dilatation transversaux, sur l’anneau central et autour des émergences (chambres de tirage et regards de visite) ;
• Les bords de dalles en béton situés au droit des entrées et des sorties du carrefour giratoire ;
• Les bords extérieurs de l’anneau central, soumis au trafic provisoire de chantier ou routier pendant les travaux du giratoire ;
• Tout le bord intérieur de l’anneau central pour pallier la circulation occasionnelle en phase définitive.
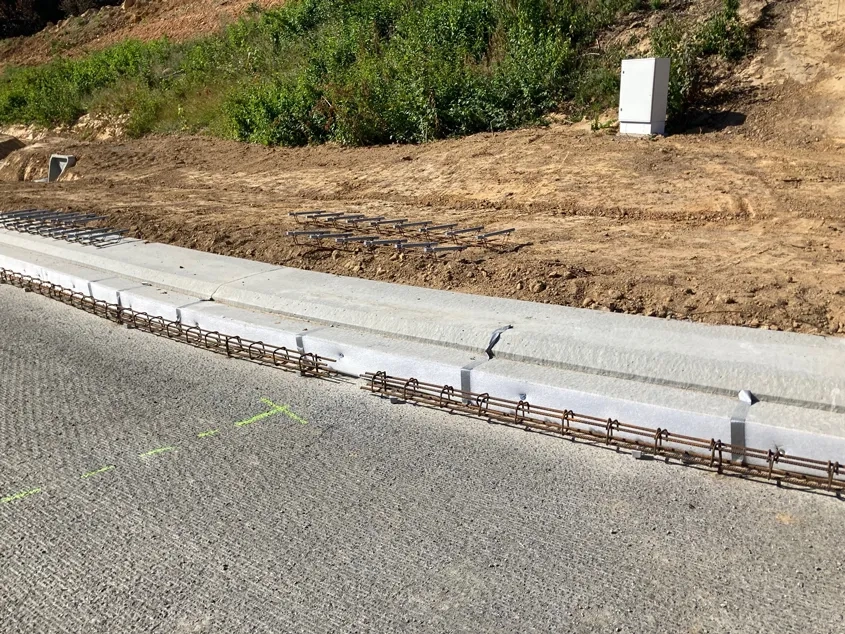
Mise en œuvre de la couche de roulement en béton BC5g
Le premier demi-anneau intérieur a été réalisé à la règle vibrante, en s’appuyant sur les bordures comme référentiel et sur le coffrage en bois. Le principe est le même pour l’anneau extérieur.
Livré à l’avant de la règle vibrante, le béton a été mis en forme et vibré en une seule opération, sur une épaisseur de 19 cm. « Une fois le béton déversé, nous l’avons travaillé par vibration externe à la règle vibrante pour bien le fermer et assurer ainsi la résistance et la classe d’exposition », précise encore Quentin Hognon. Il n’a été fait que très peu de vibrations internes à l’aiguille vibrante, sauf dans les endroits difficiles, comme les pieds de coffrage. Si l’on pervibre trop avec une formule de consistance S3, le risque est de provoquer la ségrégation du béton.
« Nous n’avons pas eu besoin d’utiliser du très gros matériel : la règle vibrante classique et l’aiguille vibrante se sont révélées une bonne méthode. Le savoir-faire de nos hommes a permis le reste. Le nivellement et la planéité ont été parfaitement assurés, l’écoulement des eaux s’effectuant sur les exutoires », ajoute Quentin Hognon.
Talochage
Immédiatement après le bétonnage, les opérations manuelles de talochage et de lissage ont été réalisées par des équipes de maçons experts pour conférer au revêtement en béton un état de surface plan et d’aspect fermé (exempt de cavités ou de trous).
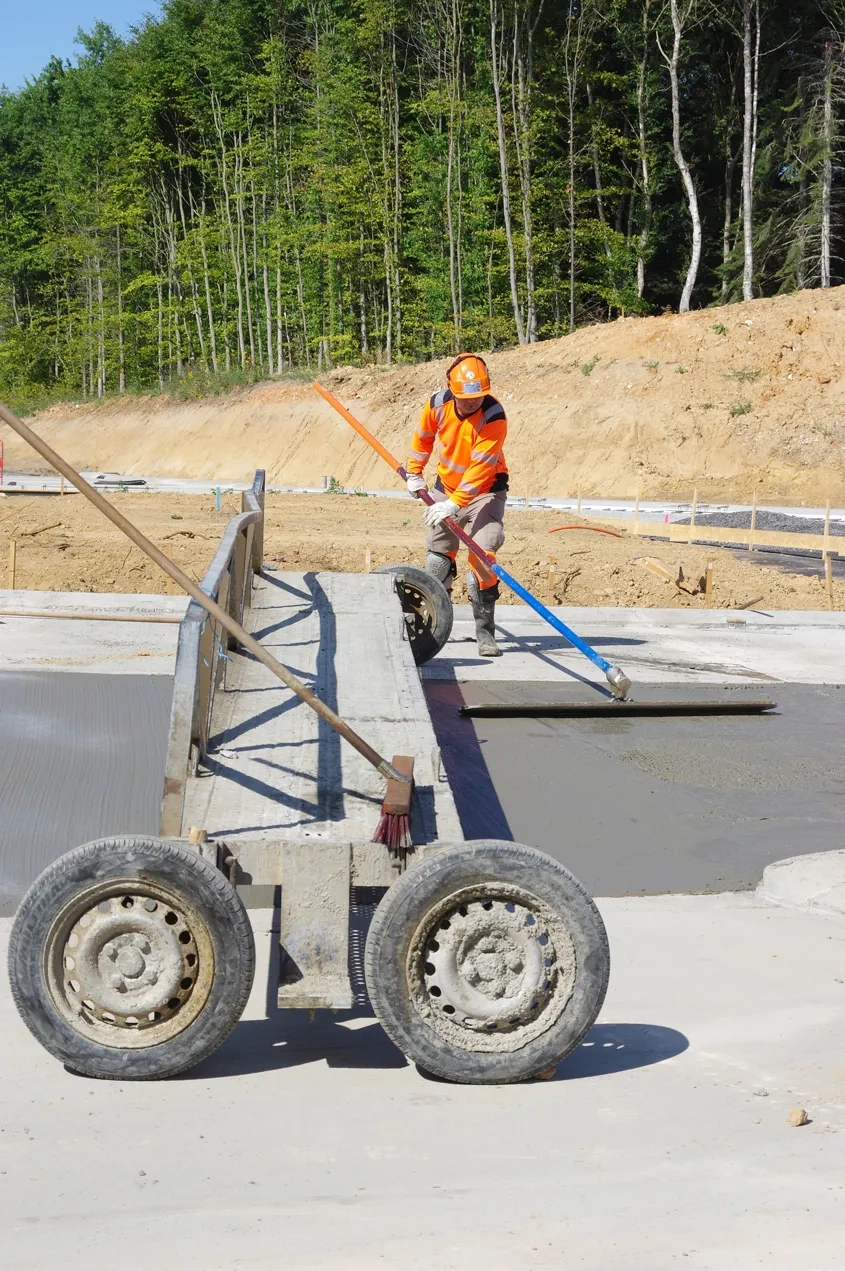
Traitement de surface
Destiné à donner au revêtement en béton les caractéristiques d’adhérence exigées par le cahier des charges, le traitement de surface a été réalisé par balayage. « Le niveau d’adhérence souhaité a été obtenu grâce à un balayage transversal réalisé manuellement », confirme Marylène Redouani.
Cure du béton
L’opération de balayage a été immédiatement suivie de la protection du béton, réalisée en pulvérisant manuellement à la surface du revêtement un produit de cure, à raison de 200 g/m2 (au minimum).
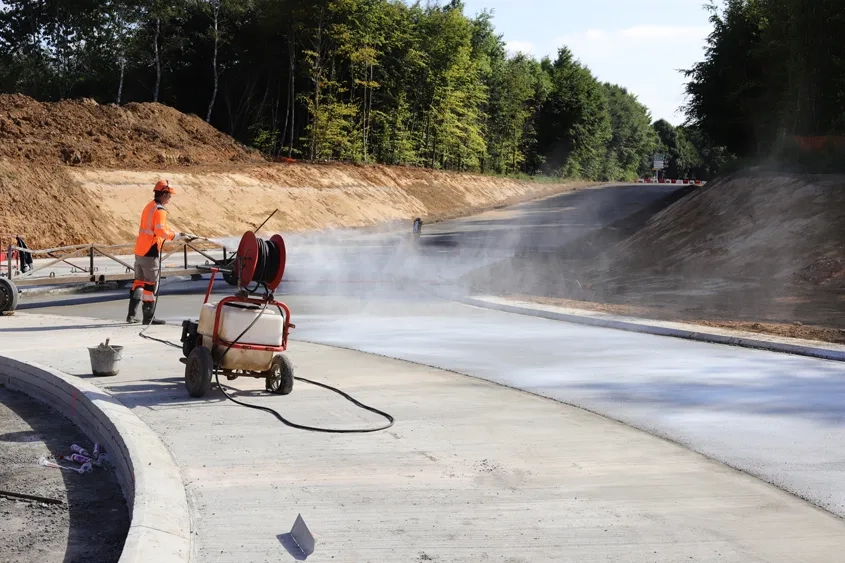
Joints
Trois types de joints ont été pratiqués sur le nouveau giratoire d’Allouville-Bellefosse, conformément au schéma de calepinage :
• 130 ml de joints de construction sur la hauteur totale du béton.
• 500 ml de joints de retrait sur 6 cm de profondeur (soit un tiers du dallage). Il s’agit d’un présciage.
• 50 ml de joints de dilatation et goujonnés.
Six à huit heures après le coulage du béton, Socotras est venue réaliser les joints dans le revêtement en béton. Compte tenu de la largeur limitée des bandes de béton (4 m), seuls des joints de retrait-flexion transversaux ont été prévus dans le plan de calepinage. Ces derniers ont pour but de localiser la fissuration de retrait du béton de manière précise et déterminée à l’avance et de réduire ainsi les sollicitations dues au retrait et au gradient thermique. « Ces joints sont réalisés en créant dans le revêtement une saignée ou une entaille qui matérialise un plan de faiblesse, selon lequel le béton est amené à se fissurer sous l’action des contraintes de traction par flexion. Cette entaille doit avoir une profondeur comprise entre un quart et un tiers de l’épaisseur du revêtement et une largeur (souffle du joint) comprise entre 3 et 5 mm. Les joints de retrait-flexion transversaux doivent être réalisés à intervalles réguliers. Leur espacement est déterminé en fonction de l’épaisseur du revêtement (au maximum 25 fois l’épaisseur), soit environ 4,5 m. Les joints de retrait transversaux des bandes adjacentes doivent être alignés », précise Edwin Constans, directeur général de Socotras.
Socotras a procédé de la manière suivante :
• Repérage des joints par le géomètre de l’entreprise de bétonnage.
• Traçage des joints à la peinture indélébile.
• En fonction des paramètres liés à la météo, à la nature des agrégats, à la nature et au dosage du ciment, enfin au mode de bétonnage, une amorce de fissuration dans le béton frais a été réalisée dans des délais appropriés après le bétonnage (compris entre six et trente-six heures), sur une profondeur de l’ordre de 6 cm.
• Au bout d’un délai fixé par Socotras (de plusieurs jours), l’élargissement aux dimensions de 10 x 35 mm x mm par sciage de l’amorce de fissuration et du joint de construction a été réalisé.
• Chanfreinage à 45 ° et sur 5 mm environ des lèvres supérieures de la réserve.
• Enlèvement des laitances de sciage par aspiration ou lavage.
• Éventuellement, séchage des lèvres du joint à la lance thermique afin d’éliminer les traces d’humidité.
• Mise en place d’un fond de joint qui doit permettre le réglage de la hauteur du produit de garnissage.
• Si le produit de garnissage le nécessite, application par pulvérisation d’un primaire d’accrochage sur les lèvres et le fond de joint.
• Préparation et application du produit de garnissage.
Contrôles
« Chaque plan de coulage a été validé par le conseil départemental. Nous avons également vérifié systématiquement la consistance du béton à l’aide de l’essai d’affaissement au cône d’Abrams et réalisé des éprouvettes et des contrôles de résistance en fendage comme en compression », ajoute Quentin Hognon.
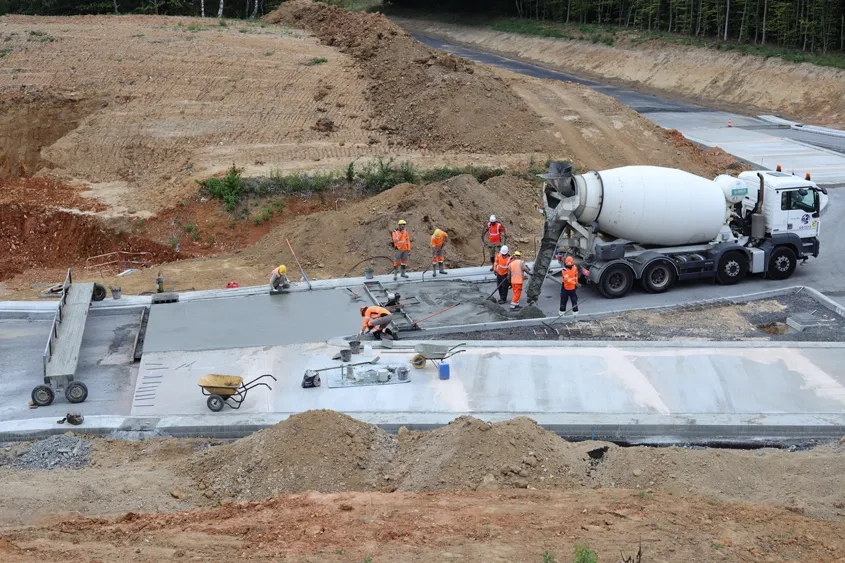
Dalles de transition
Le carrefour giratoire d’Allouville-Bellefosse comporte quatre bretelles d’accès. Au niveau des raccordements entre les chaussées souples et les bretelles d’accès en béton, une dalle de transition (également en béton goujonné) a été réalisée. « Il s’agissait d’un des points de vigilance les plus importants du chantier », souligne Quentin Hognon.
D’une longueur totale de 1,30 m, ces dalles de transition ont chacune une épaisseur qui décroît de 19 à 10 cm pour former un talon. Destinées à être recouvertes par une couche bitumineuse, comme le prolongement de la chaussée, elles assurent un raccordement robuste qui transfère progressivement les efforts exercés par les poids lourds. Cela réduit ainsi les risques de déformation de l’enrobé en limite de béton, laquelle conduirait à l’apparition d’une marche et d’épaufrures.
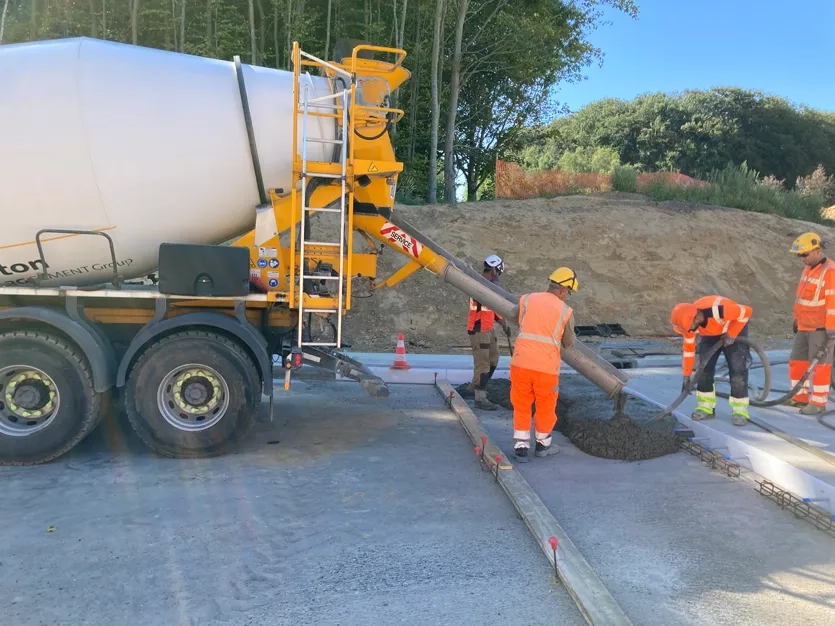
Fin des travaux
« La réalisation du carrefour giratoire en béton constitue une expérienc majeure pour le territoire Colas Ile-de-France Normandie, commente Bruno Barberot. Je tiens à souligner la très bonne coordination entre tous les intervenants, du département de la Seine-Maritime, en tant que maître d’ouvrage et maître d’œuvre, à Rincent BTP en tant que bureau d’études, à Unibéton, fournisseur du béton, et à l’agence Grands Travaux de Colas. Cela a permis une très bonne synchronisation au service d’un bel ouvrage. » Même satisfaction pour Frédéric Lieffroy, responsable commercial chez Unibéton : « Nous sommes toujours heureux et fiers de pouvoir démontrer l’intérêt du béton dans le domaine des infrastructures routières. Nous sommes friands de ce genre d’expérience. »
Bilan
« Le chantier a été achevé dans les délais. L’ouvrage a été mis en service le 23 septembre 2022 et le chantier terminé en novembre. Il sera officiellement inauguré en 2023, une fois les plantations faites », précise Marylène Redouani.
« La cadence a été soutenue à certaines périodes, sachant que le rendement d’un chantier béton en mode manuel est de l’ordre de 500 m2 par jour, avec des performances atteignant parfois les 650 m2 par jour », conclut Quentin Hognon.
Le conseil départemental de la Seine-Maritime a utilisé le béton pour la réalisation des revêtements du carrefour giratoire d’Allouville-Bellefosse. Compte tenu des risques accrus d’inondations et d’épisodes caniculaires pour cause de réchauffement climatique, ce choix se révèle pertinent sur le plan technique et économique et particulièrement judicieux du point de vue environnemental.
Localiser la réalisation
Principaux intervenants
• Maîtrise d’ouvrage et maîtrise d’œuvre : Département de la Seine-Maritime
• Assistance technique et contrôle extérieur : Rincent BTP Services Matériaux
• Entreprises
- Entreprise générale : Colas
- Mise en œuvre du béton : Colas – agence Grands Travaux
- Réalisation des joints : Socotras
• Fournisseur du béton : Unibéton (centrale de Barentin 2)
• Fournisseur du ciment : Ciments Calcia
• Fournisseur du LHR : EQIOM
En quelques chiffres
• 2 000 m2, soit 400 m3 de béton BC5g représentant 12 jours de mise en œuvre (y compris le coffrage, la préparation et la mise en place des aciers et des dalles de transition)
• 770 ml de joints
• 1 800 goujons
• 100 fers de liaison
• 500 ml de chaînage
• 300 ml de bordures
• 500 t de grave-bitume
• 300 t de LHR ROC VDS
Liens utiles
• Conseil départemental de Seine-Maritime
• Rincent BTP
• Entreprise Colas
• Entreprise Socotras
• Unibéton
• Ciments Calcia
• EQIOM
• CIMbéton
COMMENTAIRES
LAISSER UN COMMENTAIRE