Une digue de caissons géants en béton
En 2025, la principauté sera dotée d’un nouvel écoquartier de 6 hectares, baptisé l’Anse du Portier et entièrement bâti sur une extension de la ville en mer.
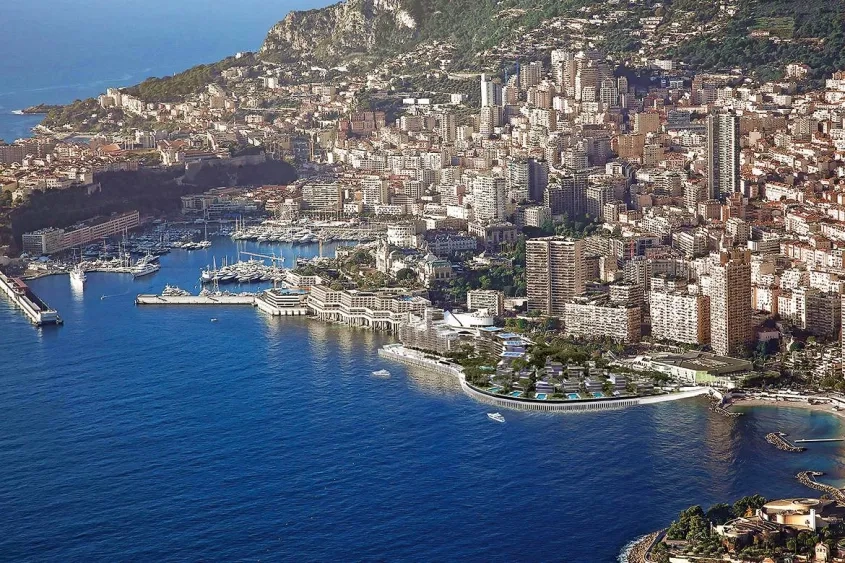
Résister à la houle, aux séismes et…aux tsunamis !
L’ensemble de ces programmes sera installé à la surface d’un gigantesque terre-plein gagné sur la mer. Pour protéger cet aménagement de grande ampleur des assauts de la houle et le confiner, il a été prévu de le ceinturer d’une ligne très robuste et épaisse de 18 caissons géants en béton armé. Ceux-ci prennent la forme de blocs de 10 000 tonnes aux dimensions d’un immeuble de 10 étages : 25 m de haut, 28 m de longueur et 30 m de large en moyenne.
« Les caissons sont répartis en sept types différents, mais chaque unité possède en réalité une géométrie unique, dessinant un trapèze dans une coupe en plan, une forme qui permet à l’ensemble de suivre la ligne courbe dessinée par la digue », décrit Éric Cheype, directeur travaux pour Bouygues Travaux Publics.
L’enveloppe extérieure des caissons constituée de quatre voiles de 70 cm d’épaisseur est contreventée par une grille de voiles intérieurs orthogonaux de 35 et 45 cm d’épaisseurs formant jusqu’à 24 cellules. « Ces contreventements sont destinés à reprendre les nombreuses sollicitations mécaniques que les caissons subiront une fois la ceinture en place, à savoir les efforts générés par la houle, les séismes et même les tsunamis ! », poursuit le directeur du chantier, précisant que les ouvrages ont été conçus en anticipant une élévation du niveau de la mer liée au réchauffement climatique. En partie haute de chaque caisson, dans la zone de marnage, une chambre d’atténuation – dite chambre Jarlan – est ménagée pour briser les vagues et atténuer leur énergie. Une « grille » – constituée d’une quinzaine de poteaux de 7,5 m de haut et de sections carrées de 0,9 m – marque l’entrée de cette cavité de béton.
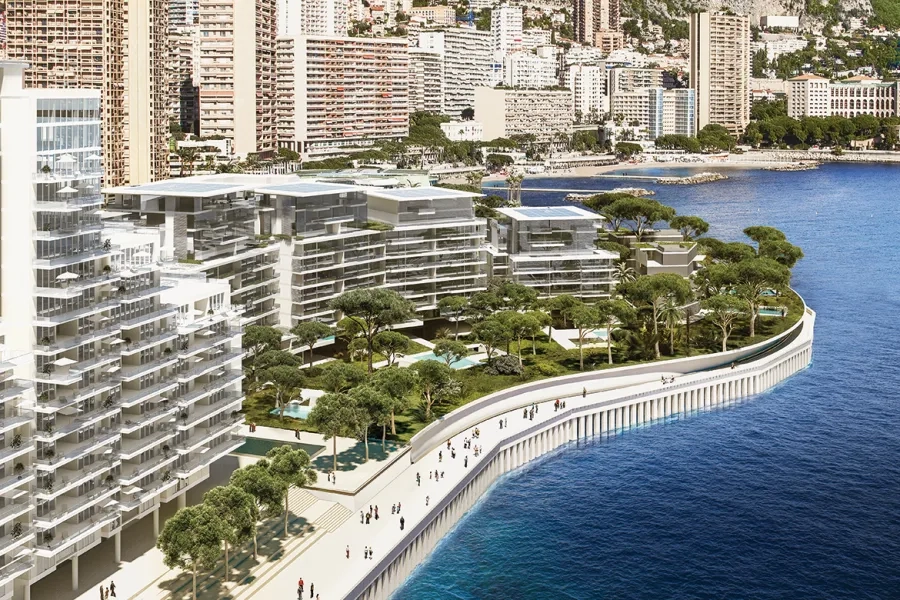
Un chantier principalement marin
Inédites, les méthodes constructives ont été conçues afin de maximiser la productivité du chantier et de minimiser son impact sur l’environnement. Par manque de place, il n’était pas envisageable d’accueillir le chantier de préfabrication des 18 caissons sur la Principauté de Monaco. Après avoir évalué les potentialités de plusieurs sites, c’est finalement au cœur du bassin est du Grand Port Maritime de Marseille que le consortium a décidé de l’installer. Il y occupe 8 ha de plans d’eau et plus de 2 ha de terre-pleins, dont 1 ha de surface destiné au façonnage des armatures et au montage des coffrages des caissons.
Le mode opératoire de construction, réalisé totalement depuis la mer, est inédit en France. Les caissons sont fabriqués l’un après l’autre dans un « caissonnier », une barge unique en son genre, à la conception très ingénieuse. Haute de 27 m, large de 50 m et longue de 56 m, cette usine flottante de 4 600 tonnes, baptisée Marco Polo, dispose d’un poste de commande qui permet de contrôler son niveau d’immersion, sa stabilité et son inclinaison afin qu’elle reste en permanence parfaitement horizontale.
Chaque caisson est construit au sein du caissonnier suivant un mode opératoire identique :
du bas vers le haut, à l’aide d’un coffrage glissant dont la cadence moyenne d’élévation a été fixée à 12 cm/heure. Particularité de cette opération : « Le coulage de béton est en continu et ne s’arrête que lorsque le sommet du caisson a été atteint, soit en moyenne au bout de 10 jours », explique Éric Cheype.
Pour assurer la continuité de coulage tout en satisfaisant à l’ensemble des contraintes de durabilité auxquelles l’ouvrage est soumis, une formule unique d’un béton adapté a été mise au point.
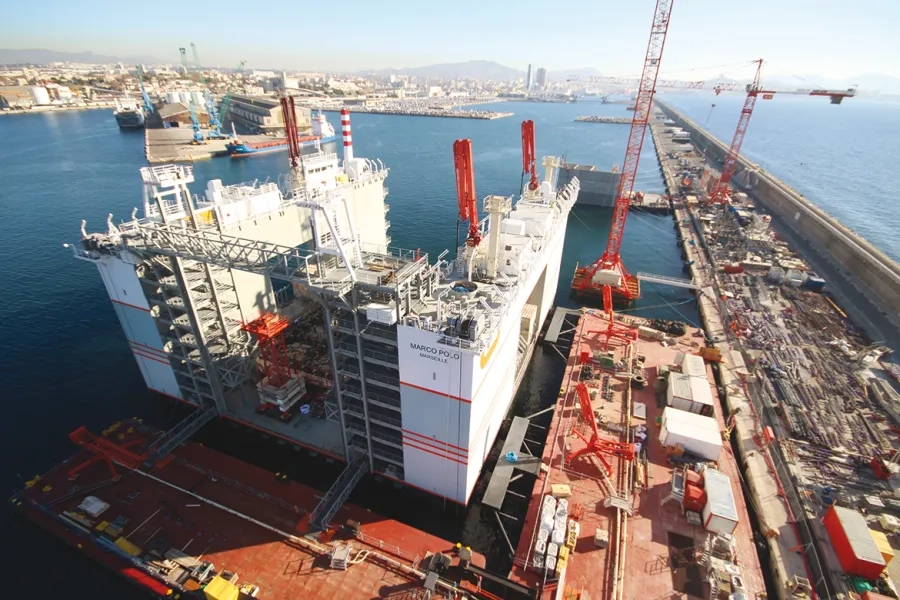
Quand le caisson s’alourdit, le caissonnier s’enfonce dans l’eau
La première étape de construction consiste à réaliser le radier du caisson (700 m2 et 80 cm d’épaisseur) sur le pont du caissonnier, alors hors d’eau. Puis le coffrage glissant est installé : sa géométrie est réglée avec précision en fonction de celle du caisson à réaliser. Il peut alors démarrer son ascension, grâce à la poussée coordonnée de 186 vérins hydrauliques, pour réaliser des passes de 1,2 m. Ce sont alors 250 à 300 m linéaires de voiles en béton armé qui sont coulés simultanément à chaque levée.
Au fur et à mesure que le caisson prend de la hauteur, il s’alourdit, ce qui a pour effet de faire progressivement « couler » le caissonnier sur lequel il est posé. Si bien qu’une fois le sommet du caisson atteint, sa « moitié » basse est immergée (tirant d’eau moyen de 13 m). « Le ballastage du caissonnier permet alors de “décoller” le caisson et de le mettre en flottaison », décrit le directeur du chantier. Il est alors déplacé jusqu’à un deuxième atelier, situé à quelques dizaines de mètres de là, où sont réalisés les poteaux en béton armé constituant la « grille » d’entrée de la chambre Jarlan.
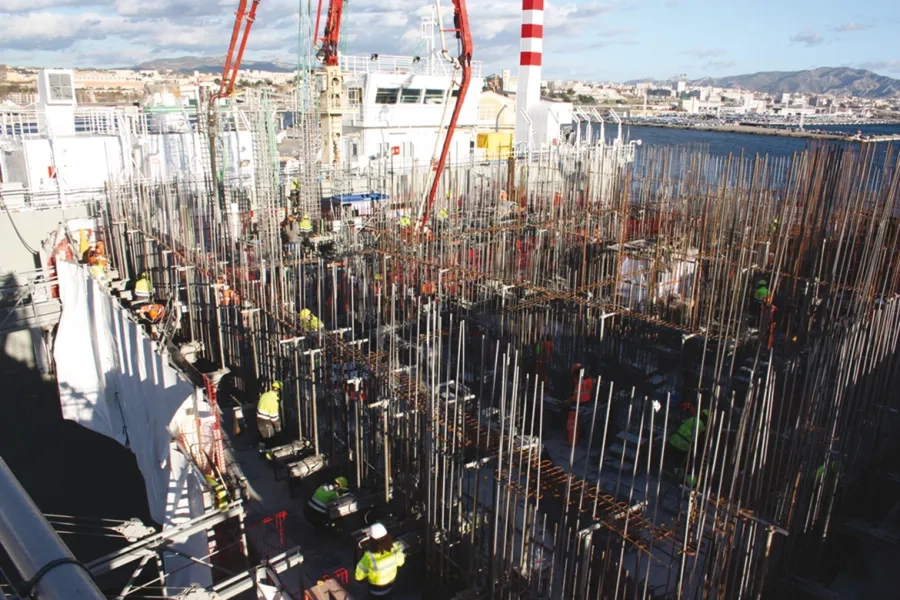
Les caissons convoyés, puis échoués à Monaco
Une fois cette étape finalisée, les caissons, toujours flottants, sont stockés sur un troisième site. Jusqu’à six caissons peuvent y être stockés avant d’être remorqués un par un jusqu’à Monaco au cours d’un périple marin d’une durée de 48 à 72 heures. Là, ils sont ballastés puis échoués sur un remblai d’assise préalablement préparé et vibro-compacté. Une fois le caisson positionné, l’eau utilisée pour le ballastage est remplacée par un matériau de lestage de granulométrie 0/20. Les travaux de finition des caissons – dalles de couverture et superstructures de protection de la future promenade – peuvent alors se dérouler.
Les opérations précédentes se répètent pour le caisson adjacent. Une fois mis en position sur le remblai d’assise, il est simplement jointoyé au caisson précédent, sans liaisonnement mécanique.

Fin 2019, la ceinture de caissons devrait être terminée. Les opérations de remblaiement du terre-plein par 600 000 m3 de sable marin en provenance de Sicile achèveront les travaux d’infrastructures. La plate-forme sera alors prête à accueillir le nouvel écoquartier.
Au final, depuis 2015, il faudra 56 mois aux équipes travaux pour mener à son terme ce chantier ambitieux, essentiellement réalisé depuis la mer.
Le tout en restant particulièrement attentif à la maîtrise des impacts écologiques du projet
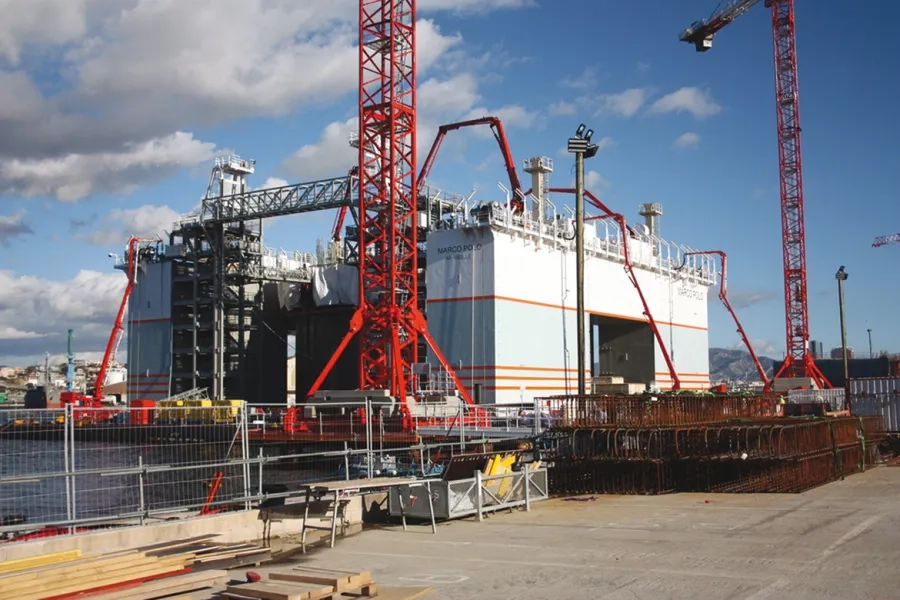
Un chantier au milieu de deux réserves marines
La future extension tangente deux réserves marines protégées, les réserves du Larvotto et des Spélugues. L’ensemble des travaux de construction à Monaco se déroule ainsi sous haute surveillance environnementale.
Des mesures de protection sont prises à chaque phase du chantier. En amont d’abord, des espèces protégées situées sur l’emprise du chantier ont été déplacées. 518 m2 d’herbiers de posidonie, 143 grandes nacres (30 à 40 cm de haut) et un ensemble de rochers colonisés par une algue protégée appelée Lithophyllum bissoïde ont ainsi été transférés dans les différentes réserves.
Des mesures sont également mises en œuvre durant le chantier. En remuant les sédiments du fond de la mer, les opérations de dragage préalables et de construction du remblai d’assise des caissons génèrent de la turbidité. Pour la limiter, un système de suivi continu a été mis en place : des bouées permettant de surveiller son niveau et de déclencher des alertes si nécessaire. Lorsque celui-ci est dépassé, des mesures d’adaptation sont déployées. Des écrans sous-marins de grande hauteur ont été installés tout autour du chantier afin de confiner les sédiments à l’intérieur de la zone. Cette barrière d’écrans antiturbidité installée du côté de la réserve du Larvotto mesure ainsi 300 m de long et couvre la quasi-totalité de la colonne d’eau.
Enfin, pour favoriser le retour de la faune et de la flore une fois le chantier terminé, les parois des caissons sont spécifiquement conçues : un rainurage vertical et régulier de 15 mm de profondeur y est creusé et des surfaces dédiées sont matricées pour créer des aspérités favorables à l’installation des écosystèmes.
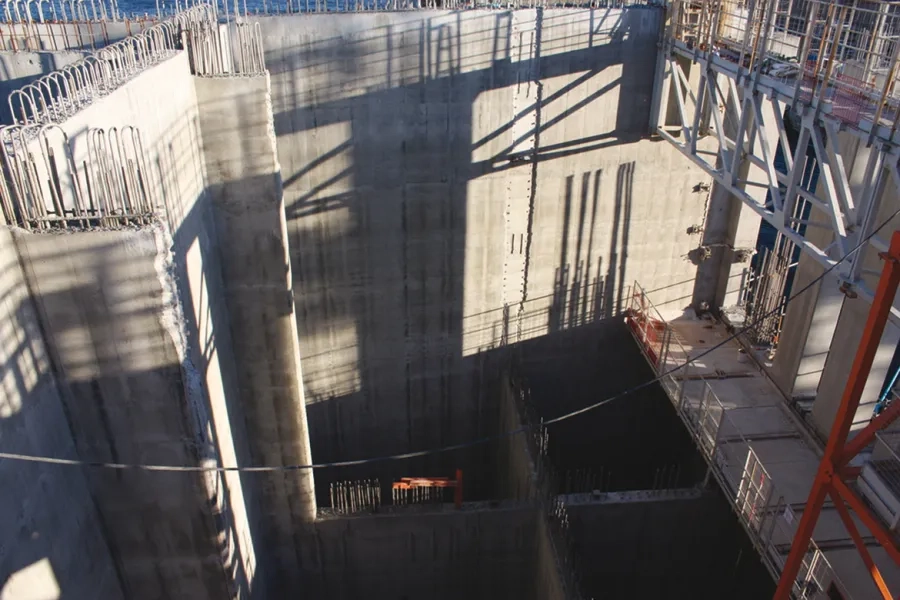
Un bétonnage 24 h/24 et 7 j/7 !
L’enjeu principal du chantier de fabrication des caissons est la productivité. « L’objectif est de réaliser un caisson tous les dix jours », explique Éric Cheype. Pour tenir ce rendement très soutenu, le coulage de béton est continu. Il s’effectue en travail posté de 3 équipes, 24 h/24 et 7 j/7, avec un objectif d’élévation moyenne de 12 cm/heure. Autant dire que la logistique d’approvisionnement et les équipes de travaux doivent être parfaitement rodées pour assurer cette continuité.
Le volume impressionnant de béton nécessaire à la fabrication de chaque caisson (3 600 m3 pour les treize plus gros, hors poteaux Jarlan) est ainsi coulé par l’intermédiaire de trois mâts de bétonnage, capables de placer le béton en tout point du coffrage glissant. Ces mâts sont reliés en contrebas à autant de pompes à béton, elles-mêmes alimentées en permanence par deux à trois camions toupies par heure, en provenance des deux centrales à béton des industriels Lafarge et Cemex, la première étant située sur le port de Marseille, l’autre à proximité. Pour sécuriser l’approvisionnement et la production, des pompes de secours et une troisième centrale à béton sont disponibles à tout moment.
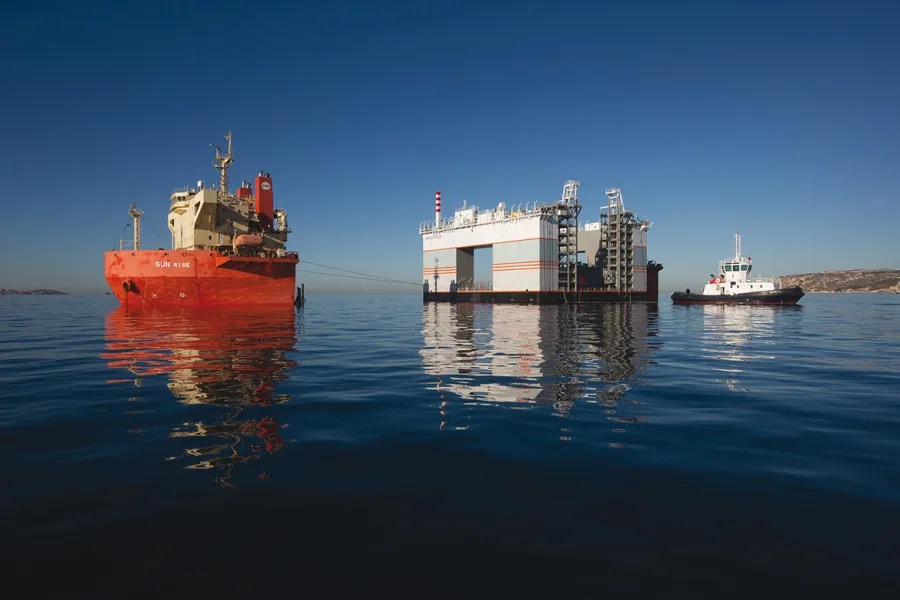
Une formule de béton unique pour tous les ouvrages
Afin de garantir un haut niveau de productivité, il a été décidé d’utiliser une formule de béton unique pour couler la totalité des structures des caissons. Celle-ci a été mise au point durant neuf mois par les experts béton de Bouygues Travaux Publics, en tenant compte de l’ensemble des contraintes – parfois antagonistes – auxquelles seront soumises les structures.
Le béton doit ainsi être durable dans le temps (ouvrage conçu pour une durée d’utilisation de 100 ans) et résister aux chlorures marins. Mais il doit simultanément présenter une excellente pompabilité, pour que les pompes de bétonnage puissent servir les zones les plus éloignées, situées à 200 m de là et à 25 m de haut, et faire prise suffisamment rapidement pour tenir le rythme des cadences imposé par le coffrage glissant. Pour cela, il a été fait appel à un béton de classe de résistance C35/45, très fermé puisqu’il dispose d’un rapport E/C très faible (0,39). Pour maintenir sa bonne ouvrabilité, plusieurs types d’adjuvants sont employés : des superplastifiants et des retardateurs de prise.
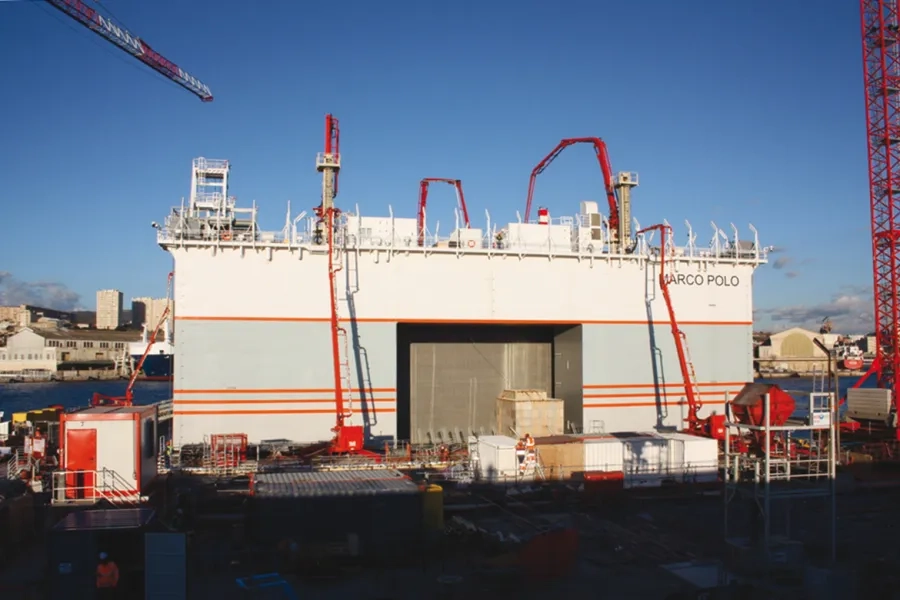
Le ciment est quant à lui de type CEM V PM/ES. « Ce ciment comporte une proportion importante de cendres volantes et de laitiers de hauts-fourneaux, ce qui limite la chaleur générée lors de la prise du béton, et donc les risques de fissuration », complète Éric Cheype.
Dans les caissons, la densité d’armatures est très importante, puisqu’elle atteint 250 à 350 kg/m3 de béton. Dans les poteaux Jarlan, elle est même de 450 kg/m3.
Pour garantir encore la durabilité structurelle des caissons, l’acier au carbone classique des armatures est remplacé par de l’acier inoxydable dans les zones immergées et de marnage. De plus, pour accroître « l’étanchéité » des bétons au jeune âge – une fois décoffrés, les voiles se retrouvent rapidement immergés – et empêcher la pénétration des ions chlorures, une résine Masterseal est appliquée au rouleau sur les parties immergées. Enfin, sur les parties des caissons qui resteront émergées, et donc visibles depuis la mer, la teinte est éclaircie pour des raisons esthétiques, par ajout de dioxyde de titane dans la formulation.
Chiffres clés
- Montant total des travaux d’infrastructures 842 M€ HT
- 56 mois de travaux
- 18 caissons : 86 000 m3 de béton
- 18 000 tonnes d’armatures, dont 3 500 tonnes en acier inoxydable : soit un total de 10 000 tonnes/caisson
Principaux intervenants
Reportage photos : Valode & Pistres Architectes ; Olivier Baumann ; Bouygues travaux publics – Andromède océanologie ; Helios Image
Autorité concédante : Principauté de Monaco – Groupement de concession pour la conception, la réalisation et la commercialisation de l’opération : Société Anonyme Monégasque « L’Anse du Portier » composée de : Constructeurs : Bouygues Travaux Publics, Bouygues Bâtiment Sud-Est, Bouygues SAS ; Engeco, JB Pastor & Fils ; Michel Pastor Group, Smetra – Satri Architectes, urbanistes, paysagistes : Alexandre Giraldi, Patrick Raymond ; Valode & Pistre Architectes ; Michel Desvigne ; Renzo Piano, Emmanuel et Olivier Deverini – Bureau d’études techniques, environnement : Egis, Oasis, Somibat, MBA (Amo), JB Pastor & SNEF, Creaplan, A9C – Contrôleur technique : Socotec, Cowi.
COMMENTAIRES
2 COMMENTAIRES