Une aire de repos innovante associant valorisation des sols en place et chaussée composite BC5g/GB3
C’est grâce à l’aménagement à 2x2 voies de la RN 10 entre Reignac et Chevanceaux que le projet de réalisation de l’aire de repos de la Grolle a vu le jour. D’une surface de 20 000 m2, les usagers de la RN 10 vont désormais pouvoir y faire une halte et apprécier les qualités de confort et de durabilité de cet aménagement. Pour réaliser cette aire, le maître d’ouvrage a opté, pour réaliser les travaux de terrassements, pour la technique de valorisation des matériaux en place aux liants hydrauliques, et pour la typologie de la structure, il a misé sur le concept de chaussée composite associant un revêtement en béton et une couche de fondation en grave-bitume. Une technique en phase avec le développement durable et qui n’avait encore jamais été utilisée à une telle échelle par la DIR Atlantique.
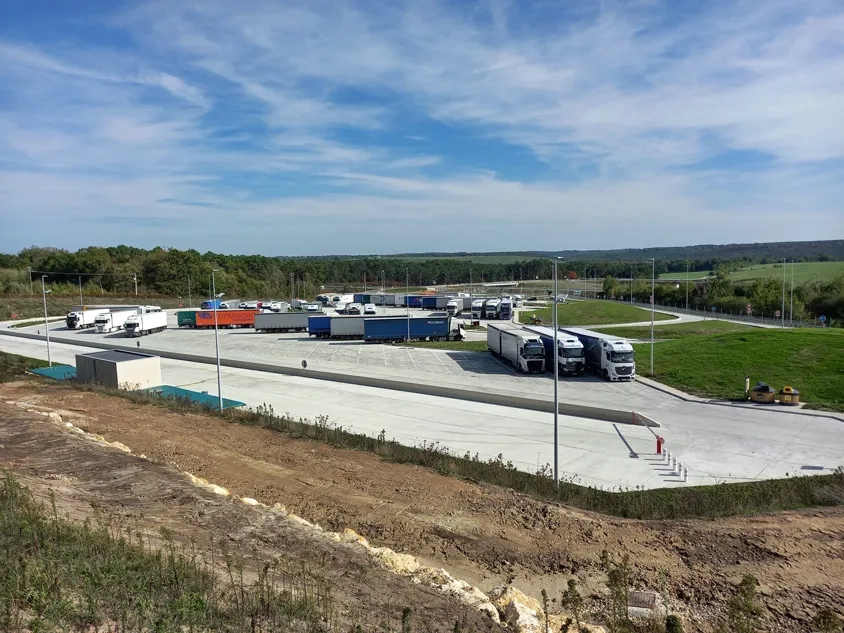
Situation
L’aire de repos de la Grolle se situe sur l’aménagement à 2 x 2 voies de la section Reignac-Chevanceaux de la route nationale RN10 (liaison Poitiers-Angoulême-Bordeaux). Le projet d’aménagement d’une aire de repos fait partie intégrante du projet routier et il est inscrit dans la déclaration d’utilité publique (DUP) du 21 avril 1999 (prorogée le 20 avril 2009).
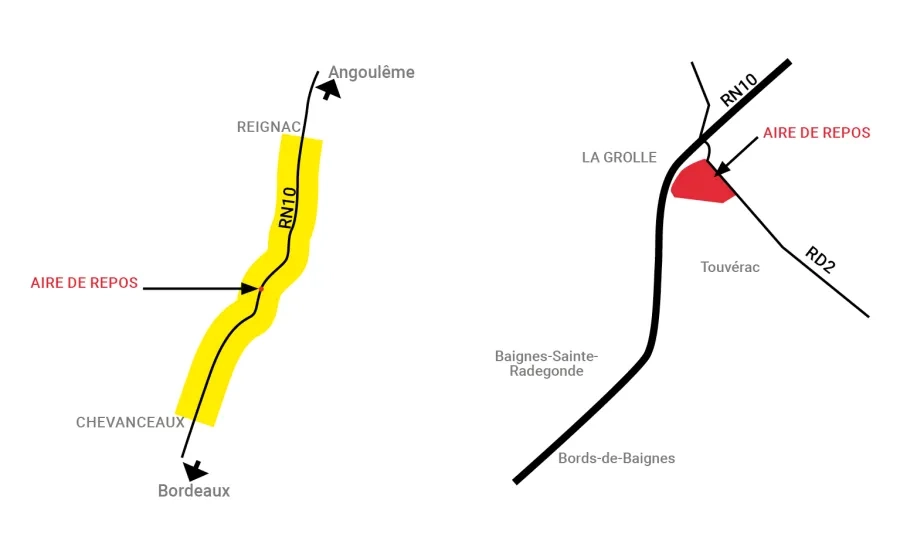
Dans le projet initial soumis à la DUP, l’aménagement était conçu sous la forme d’une aire bilatérale située au lieu-dit des Landes-de-Cossade, à proximité d’un site qui est devenu plus tard le site Natura 2000 des carrières de Touvérac. Au cours des études, l’impact a été jugé trop important. L’aire a finalement trouvé place sur du foncier appartenant à l’État : elle se situe au lieu-dit de La Loge, entre la nouvelle RN10 à 2 x 2 voies, l’ancienne RN10 reclassée dans la voirie de la commune de Touvérac (Charente) et la RD2 qui dessert Baignes-Sainte-Radegonde et Touvérac.
L’aire est directement accessible, depuis la 2 x 2 voies, par le giratoire ouest de l’échangeur complet n° 73 avec la RD2 et dans les deux sens de circulation.
État des lieux
Entre Poitiers et Bordeaux, la RN10 constitue un axe routier majeur supportant un trafic national et international de l’ordre de 25 000 véhicules par jour, dont plus de 40 % de poids lourds (environ 10 000 PL/j) sur la section Angoulême-Bordeaux (source DIRA/TMJA 2021). La mise à 2 x 2 voies de la RN10 entre Poitiers et Bordeaux a été déclarée d’utilité publique par décret en Conseil d’État du 21 avril 1999, prorogée par décret le 20 avril 2009.
Le projet inclut la création d’une aire, accessible depuis la nouvelle infrastructure, destinée à :
• Offrir aux usagers des possibilités d’arrêt pour des raisons de sécurité et de confort.
• Accueillir tous types d’usagers avec une aire de repos offrant un large éventail de services.
• Reconstituer une offre de stationnement, en particulier pour les poids lourds.
L’aire est donc conçue pour gérer, contrôler et permettre le stationnement d’un nombre important de poids lourds dans des conditions satisfaisantes. On constate en effet, sur cet axe très fortement chargé, un déficit d’équipements pour que ceux-ci respectent la réglementation en matière de temps de repos obligatoire.
Projet
Conception
L’aire de repos de la Grolle est conçue avec les objectifs recherchés pour toute aire de repos, à savoir permettre aux usagers de la route d’effectuer un arrêt programmé pour des motifs de sécurité et de confort (cf. « Aménagement des aires de repos », Sétra, 1996). Selon ce document, la satisfaction des besoins immédiats de l’usager et de son véhicule porte sur :
• Stationner aisément et en toute sécurité ;
• Manger, boire ;
• Commodités (toilettes) ;
• Détente, repos ;
• Informations routières et touristiques.
« La distribution de carburant n’est pas incluse dans ces besoins, puisqu’il ne s’agit pas d’une aire de service (contrairement à celles de Bédenac et au Centre routier de Plaisance, situés de part et d’autre de celle-ci) », précise Gilles Petit, chef de projet à la direction interdépartementale des routes Atlantique (DIRA). Il n’est pas non plus prévu de service de restauration. L’aire de repos de la Grolle comprendra donc :
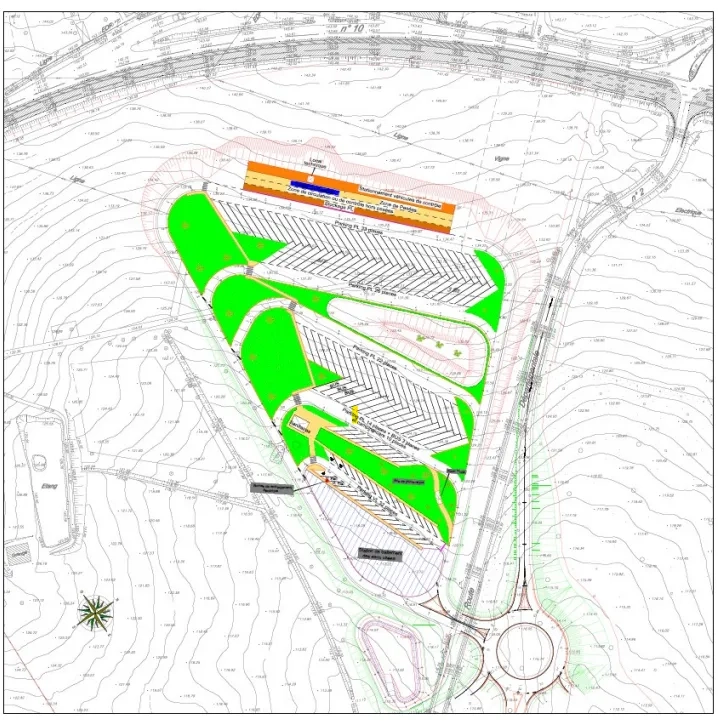
Des parkings
Les zones de stationnement sont bien définies et identifiées. L’aire de repos comporte une zone de stationnement réservée aux poids lourds, une zone de stationnement réservée aux véhicules légers et une zone de contrôle des poids lourds. Elle peut accueillir :
- 105 places pour poids lourds ;
- 32 places pour véhicules légers, y compris 2 places PMR et 2 places pour des voitures électriques ;
- 3 places d’autocars ;
- 10 places pour camping-cars ou caravanes ;
- 1 place pour un camion-restaurant.
« Toutes les places dédiées aux véhicules légers ainsi que tous les cheminements piétons (y compris depuis les parkings pour poids lourds) seront suffisamment éclairés pour permettre la circulation piétonne et sécuriser la zone de parking », ajoute Gilles Petit.
« Toutes les places dédiées aux véhicules légers ainsi que tous les cheminements piétons seront suffisamment éclairés pour permettre la circulation piétonne et sécuriser la zone de parking »
Une zone de contrôle des PL
Cette zone comprend :
- Zone de stationnement des véhicules des contrôleurs et des forces de l’ordre ;
- Zone de stationnement temporaire des poids lourds qui vont être contrôlés ;
- Un bâtiment à usage de local technique ;
- Un système de pesée des poids lourds.
Un bâtiment sanitaire
L’aire est considérée comme une installation ouverte au public (IOP). À ce titre, elle doit être accessible aux personnes à mobilité réduite (PMR) (article R.111-19 et suivant du Code de la construction et de l’habitat).
Une aire de pique-nique
Elle comprend six bancs et six tables, dont les plateaux participeront notamment à la valorisation des territoires.
Objectifs
La RN10 étant une voie encombrée et dangereuse, les objectifs de l’aménagement de cette aire de repos sont de :
• Sécuriser les arrêts et, en particulier, ceux des poids lourds ;
• Permettre aux usagers de la route d’effectuer un arrêt programmé, pour des motifs de sécurité et de confort.
Exigences
Les exigences, prises en compte dans la conception de l’aire de repos, couvrent les trois aspects suivants :
Aspect social (ou humain)
Il comprend :
- Le confort d’usage pour tous les publics, sans discrimination, notamment concernant l’accueil ;
- La possibilité d’offrir un service public accessible aux personnes à mobilité réduite (PMR) ;
- La facilité d’accès aux équipements pour l’exploitant DIRA, visant l’entretien et le remplacement (maintenance, équipements sanitaires et équipements électriques).
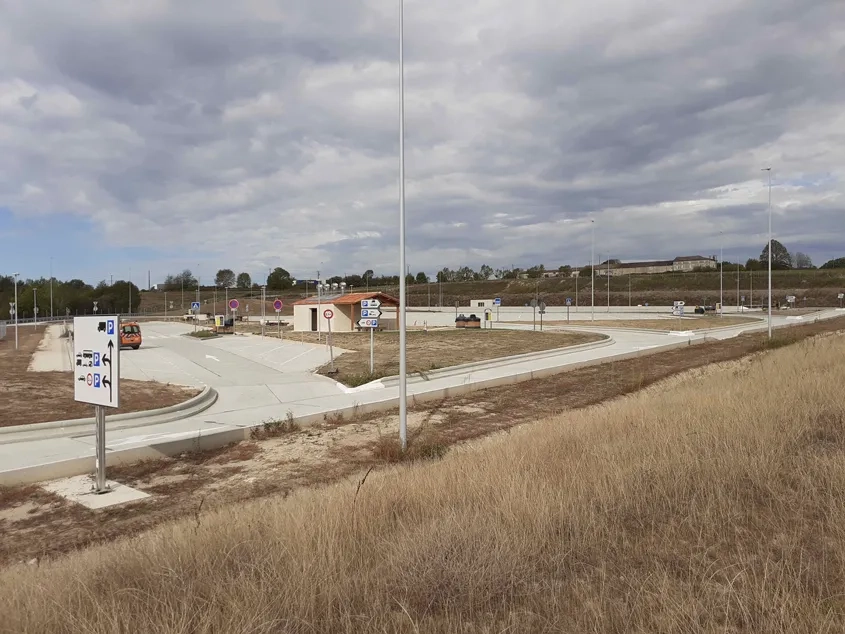
Aspect économique
Il prend en compte deux idées-forces :
- Un raisonnement en coût global dans les choix d’équipements à mettre en place (porter une attention particulière aux coûts d’entretien, de maintenance, et aux moyens humains associés) ;
- L’utilisation de matériaux très résistants à la dégradation, au vandalisme, et peu tentants pour le vol (peu valorisables ou difficiles à extraire).
Aspect environnemental
Il intègre les exigences d’un développement écoresponsable et respectueux de l’environnement et en particulier :
- La conservation du patrimoine architectural et paysager ;
- Les économies d’énergie grâce à la mise en place de systèmes d’éclairage et de matériel à faible consommation énergétique ;
- Le recyclage des déchets de chantier, de démolition et de déconstruction ;
- Le fait de favoriser, dans la plupart des cas, les produits répertoriés dans la base de données INIES dont les performances environnementales et sanitaires sont faibles ou écolabellisées ;
- L’économie des ressources naturelles.
L’aire est aussi pressentie pour accueillir une centrale photovoltaïque avec ombrières sur les parkings de poids lourds et panneaux solaires au sol.
Choix du béton comme matériau de surface
Pour une aire de repos où le stationnement est la fonction d’usage par excellence, il était impératif de rechercher un matériau de revêtement de chaussée capable de résister durablement au poinçonnement, aux charges lourdes et aux efforts tangentiels.
Pour l’aire de repos de la Grolle, la DREAL, maître d’ouvrage, et la DIRA, maître d’œuvre, n’ont pas hésité sur le choix du béton comme matériau de surface. « Le béton est incontournable sur ce type d’ouvrage. Par sa résistance au poinçonnement et aux agressions chimiques causées par les chutes accidentelles de kérosène, le béton est bien plus approprié qu’une couche de surface en enrobé », commente Gilles Petit, responsable du projet à la DIRA.
En outre, compte tenu du trafic élevé et des charges lourdes qui vont circuler et stationner sur ce revêtement, la DIRA a choisi un revêtement en béton non armé mais à joints goujonnés BC5g. « Nous avons choisi une chaussée en dalles de béton à joints goujonnés, car ce type de revêtement en béton présente une durée de vie très élevée, ce qui – en termes de coût global – est important », poursuit Gilles Petit.
« Le béton est incontournable sur ce type d’ouvrage. Par sa résistance au poinçonnement et aux agressions chimiques causées par les chutes accidentelles de kérosène, le béton est bien plus approprié qu’une couche de surface en enrobé »
Choix de la chaussée composite comme type de chaussée
La grande originalité de ce chantier réside aussi dans la typologie de la structure de chaussée utilisée. En effet, plutôt que de faire appel à une structure traditionnelle en béton, constituée d’un revêtement en béton non armé et à joints goujonnés BC5g, et d’une couche de fondation en béton maigre BC3, structure conçue avec un décollement à l’interface entre le revêtement et la fondation, la DIRA a décidé d’utiliser en fondation une couche de grave-bitume en lieu et place du béton maigre. « Cette structure innovante et éprouvée depuis vingt ans autorise à retenir l’hypothèse d’un collage à l’interface revêtement-fondation, synonyme d’une optimisation de la structure (réduction de l’épaisseur de celle-ci d’environ 25 %) et, par conséquent, d’une réduction de la consommation des matériaux nobles dans la chaussée », ajoute Gilles Petit.
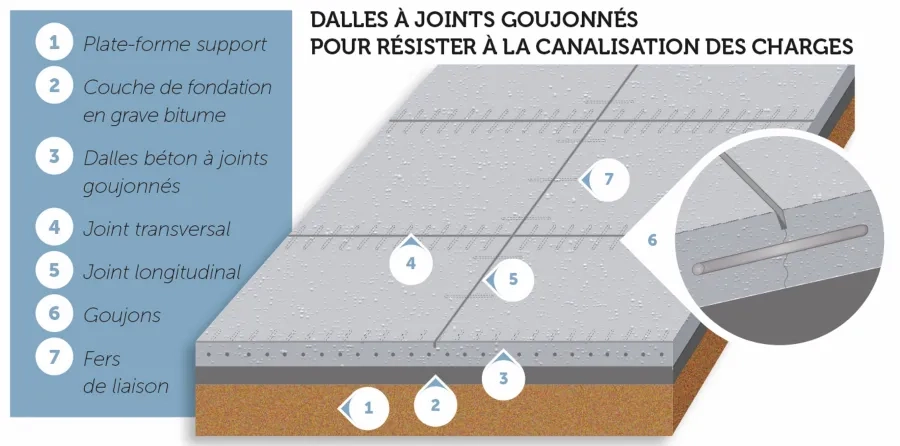
Choix du traitement des sols en place au LHR pour la plate-forme support
En dessous des couches de roulement et de fondation et sur toute la surface de l’aire de repos, la plate-forme support a été conçue avec un complexe arase terrassement-couche de forme en matériaux du site traités avec des dosages et des épaisseurs à déterminer lors des études.
Grâce au traitement en place des sols, on minimise l’apport de matériaux nobles, d’où un bénéfice écologique certain : moins d’extraction de granulats de carrières ; moins de nuisances dues au transport des granulats en camion.
« Par ses avantages économiques et environnementaux, qui ne sont plus à démontrer, la technique de traitement des sols en place aux liants hydrauliques routiers se prête parfaitement à ce type de chantier et s’impose d’elle-même. Elle avait été précédemment mise en œuvre sur les 11 km de la RN10, aménagée à 2 x 2 voies de part et d’autre de l’aire », précise Gilles Petit.
Compte tenu de l’utilisation d’une chaussée composite, la plate-forme support doit donc avoir une portance minimale PF3.
« Par ses avantages économiques et environnementaux, qui ne sont plus à démontrer, la technique de traitement des sols en place aux liants hydrauliques routiers se prête parfaitement à ce type de chantier et s’impose d’elle-même »
Études
Le contexte géotechnique
Le site de l’aire de repos de la Grolle se situe sur une formation géologique sablo-argileuse. Cette dernière occupe, en surface, la totalité de l’aire, avec des gisements importants et homogènes.
Les reconnaissances géotechniques
Une campagne de reconnaissance géotechnique a été menée pour les besoins des études de terrassement : neuf sondages géotechniques, tous types confondus, ont été réalisés. Les différents matériaux ont été identifiés et classés conformément au Guide des terrassements routiers (GTR) et à la norme NF P 11 300 « Classification des sols ». On peut regrouper ces matériaux en deux grandes catégories :
• Sols classés B5, conformément au GTR ;
• Sols classés B6, conformément au GTR.
Les études de traitement
La présence des matériaux B5 et B6 sur le site a rapidement permis d’identifier les gisements potentiels en matériaux pour la partie supérieure des terrassements (PST) et la couche de forme (CDF). Associée à leur facilité d’utilisation (taux de réemploi proche de 100 % lors des mouvements des terres), la stratégie – qui avait été imaginée dès les études préalables – consistait à optimiser les mouvements des terres en maximisant le réemploi des matériaux du site et en les traitant soit à la chaux, soit au liant hydraulique routier (LHR) pour les couches nobles de la future plate-forme support de chaussée. Le matériau obtenu par mélange de ces deux sols (B5 et B6) a fait l’objet d’une série d’essais pour :
• Vérifier l’aptitude du sol au traitement (norme NF P 94 100) ;
• Déterminer les performances mécaniques obtenues par un traitement à la chaux ;
• Déterminer les performances mécaniques obtenues par un traitement au LHR.
L’objectif était de trouver un liant adapté au sol afin de garantir à la fois les performances mécaniques visées (résistance mécanique et tenue au gel) et les contraintes spécifiques de mise en œuvre du chantier.
En outre, pour la CDF, une étude géotechnique de niveau 1 a été menée avec l’objectif d’obtenir :
• Une plate-forme support de classe PF3 ;
• Un matériau traité de classe mécanique 5 (zone 4 du diagramme de classification des sols traités).
Les résultats sont donnés dans le tableau suivant :
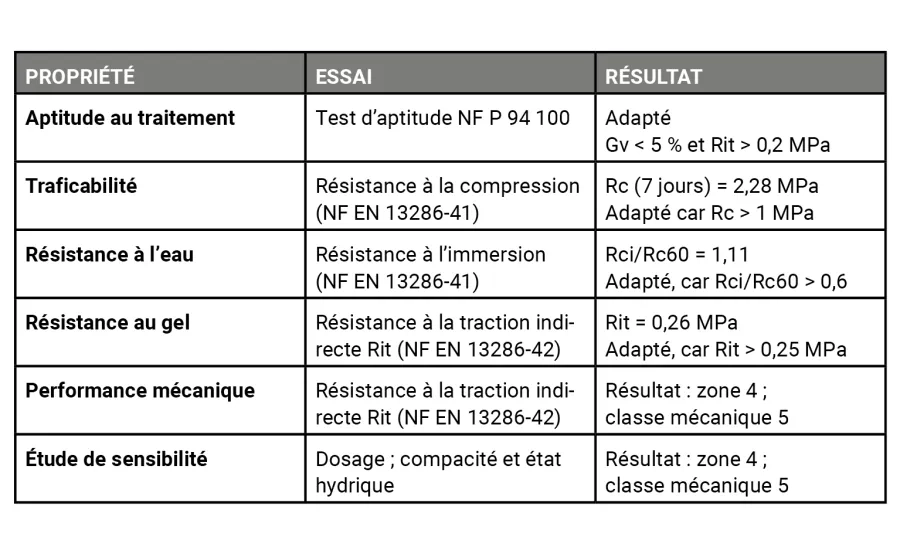
La solution retenue pour la plate-forme support de chaussée
Les études ont permis de caractériser le matériau traité, de définir les dosages en vue d’atteindre les performances visées et d’établir un dimensionnement de la plate-forme support de chaussée. Compte tenu de l’utilisation d’une chaussée composite, la plate-forme support doit avoir une portance minimale PF3.
Pour atteindre cet objectif, il a été choisi de réaliser le traitement du sol en place en deux couches successives : traitement de la PST et traitement de la CDF.
Partie supérieure des terrassements
L’arase (PST) constituée d’un sol B5/B6 sera traitée à la chaux (dosage : 1,5 %) sur une épaisseur de 40 cm afin, d’une part, d’assécher et de figer le matériau du site et, d’autre part, d’améliorer la portance du sol de la PST. L’objectif de portance sur l’arase traitée est fixé à 50 MPa au minimum.
- Objectifs :
• Densification : q3.
- Critères de réception :
• Compacité conforme à densification q3.
• Portance EV2 ≥ 50 MPa.
Couche de forme traitée au LHR
Au-dessus de l’arase traitée, la CDF est conçue par un traitement du sol B5/B6 en place avec un LHR. L’objectif de portance sur la CDF traitée est fixé à PF3 (120 ≤ EV2 < 200 MPa). Le matériau B5/B6 est traité au LHR Ligex (dosage : 6 %) et sur une épaisseur de 35 cm.
- Objectifs :
• Matériau non gélif (Rtb ≥ 0,25 MPa).
• Densification : q3.
• Matériau de classe mécanique 5 (zone 4).
- Critères de réception :
• Compacité conforme à densification q3.
• Portance : 120 ≤ EV2 < 200 MPa.
• Déflexion : d ≤ 60/100 mm.
• Déflexion caractéristique mesurée au FWD : 48,3/100.
Choix de la structure de la chaussée composite
Compte tenu des performances attendues de la plate-forme support, la structure de la chaussée composite est la suivante :
• Pour la zone réservée à la circulation et au stationnement des poids lourds :
- Enduit bicouche clouté qui assure à la fois la protection de la couche de forme traitée et le collage à l’interface entre la couche de forme et la structure de chaussée.
- Couche de fondation en grave-bitume GB3, de granulométrie 0/14, d’épaisseur 10 cm.
- Revêtement en béton non armé à joints goujonnés BC5g, de granulométrie 0/20, d’épaisseur 18 cm.
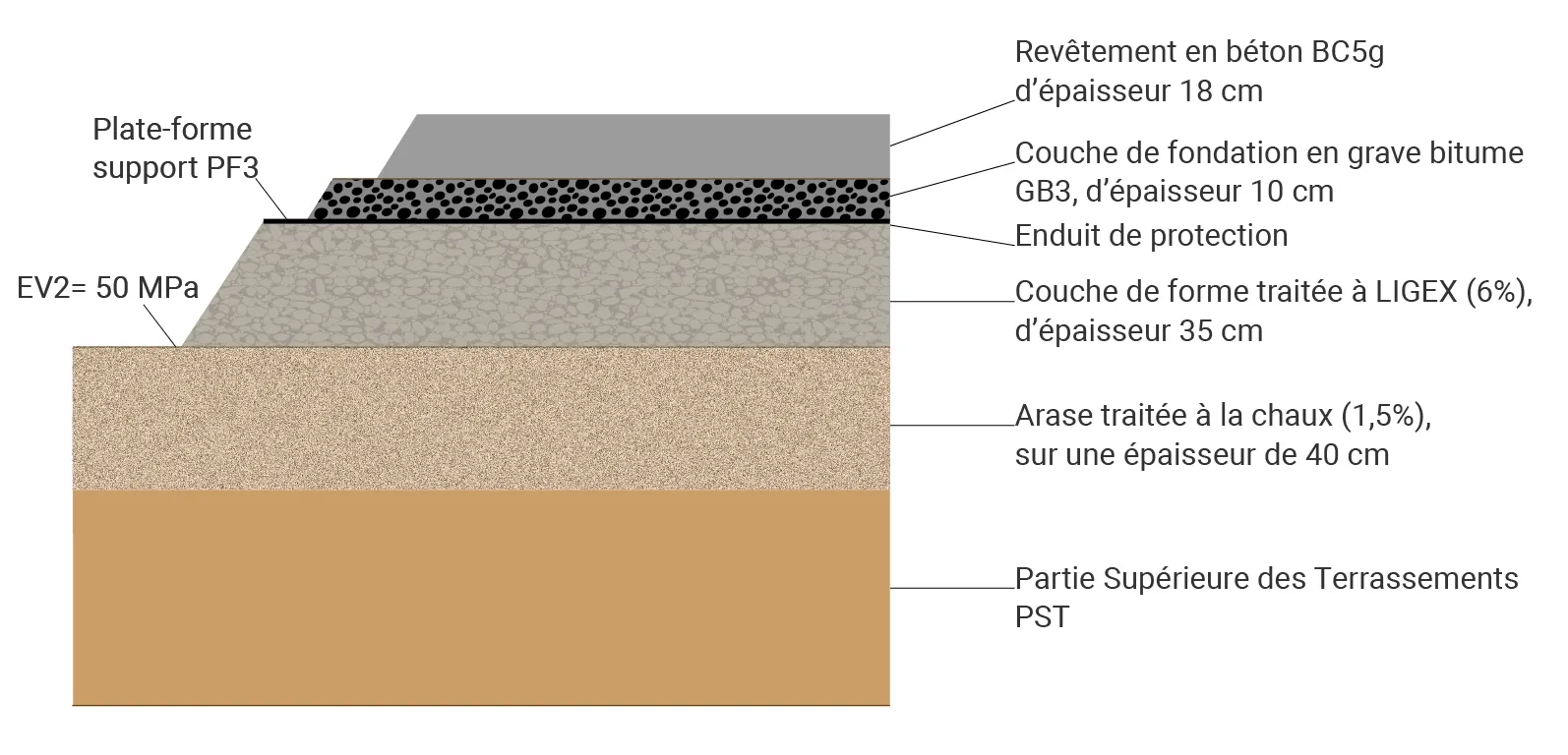
• Pour la zone réservée aux piétons comme à la circulation et au stationnement des véhicules légers :
- Enduit bicouche clouté qui assure à la fois la protection de la couche de forme traitée et le collage à l’interface entre la couche de forme et la structure de chaussée.
- Couche de fondation en grave-bitume GB3, de granulométrie 0/14, d’épaisseur 10 cm.
- Revêtement en béton non armé à joints non goujonnés BC5, de granulométrie 0/20, d’épaisseur 14 cm.
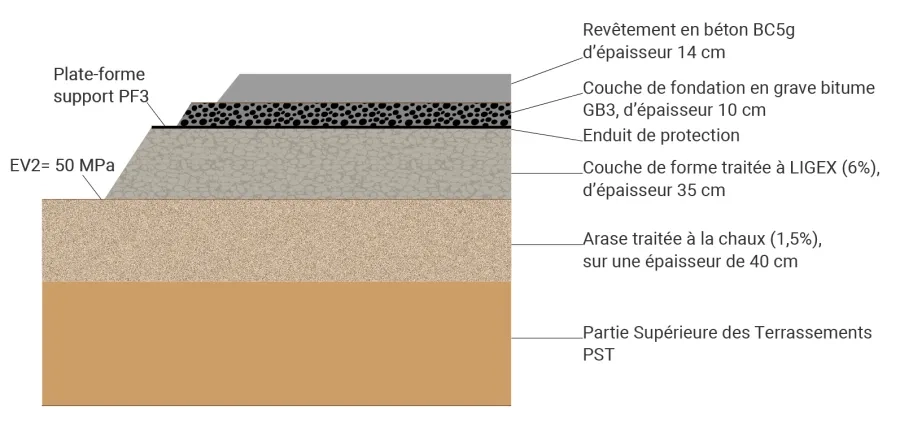
Mise en œuvre
Le chantier a été réalisé par deux entreprises : Garraud TP/Ecostab, mandataire pour les terrassements, et Eurovia, mandataire pour les travaux relatifs à la grave-bitume, à l’assainissement et à la chaussée en béton.
Cette aire de repos, d’une superficie de 20 000 m2, a été réalisée en quatre phases, de mars 2021 à juillet 2022. Cela consistait à effectuer successivement :
• Travaux de terrassement généraux et d’assainissement ;
• Traitement de l’arase à la chaux vive sur 40 cm ;
• Réalisation de la couche de forme traitée avec un LHR, d’épaisseur 35 cm ;
• Réalisation de l’enduit de protection ;
• Mise en œuvre de la couche de fondation en grave-bitume, d’épaisseur 10 cm ;
• Réalisation du revêtement en béton non armé et à joints goujonnés BC5g, d’épaisseur 18 cm, sur la zone réservée aux poids lourds ;
• Réalisation du revêtement en béton non armé et à joints non goujonnés BC5, d’épaisseur 14 cm, sur la zone réservée aux véhicules légers et sur les zones de circulation piétonne.
Travaux de terrassement généraux et d’assainissement
Le site de la future aire de repos de la Grolle ayant servi de base de vie pour l’entreprise qui a mis à 2 x 2 voies la section de la RN10 comprise entre Reignac et Chevanceaux, une partie des travaux de terrassement généraux avait été déjà réalisée. Mais, pour les besoins de la future aire de repos, des travaux d’assainissement ont été conduits par Eurovia.
Travaux de la PST traitée à la chaux
Le traitement des matériaux en place, essentiellement des matériaux B5 et B6, a été fait selon la technique habituelle : préparation du sol, ajustement de l’état hydrique, épandage du liant, malaxage, premier compactage, réglage, puis compactage final. « Le traitement de sol a été réalisé en deux phases. Nous avons d’abord traité à la chaux vive (1,5 %) la partie supérieure des terrassements sur une épaisseur de 40 cm, puis rapporté des sols B5/B6 et traité au LHR Ligex (6 %) la couche de forme sur une épaisseur de 35 cm », précise David Daguzan, Responsable de chantier en charge des travaux de terrassement de l’entreprise Ecostab.
Après la scarification de l’arase, la chaux vive a été épandue à l’aide d’un épandeur asservi, à raison de 10 kg/m2. Le malaxage du sol et de la chaux a été réalisé sur une épaisseur de 45 cm (pour une épaisseur finale, après compactage et découpe, de 40 cm), à l’aide d’un pulvimixeur Wirtgen type WR 250. Un réglage avec une niveleuse a ensuite été effectué, puis un compactage à l’aide d’un compacteur VP5 pour garantir l’obtention de la compacité visée.
Travaux de mise en œuvre de la CDF traitée avec un LHR
Une fois l’arase traitée, la portance de la partie supérieure des terrassements (PST) s’élevait à 50 MPa. Ensuite, pour réaliser la couche de forme, il a fallu dans un premier temps, acheminer les matériaux du dépôt provisoire (approvisionnement avec reprise sur stock à l’aide d’une pelle sur chenilles et tombereaux articulés) ; suivie de l’opération de mise en œuvre du matériau sur 40 cm pour une épaisseur finale de 35 cm, afin de tenir compte du compactage et de la recoupe finale. Un préréglage avec une niveleuse asservie, a ensuite été réalisé de façon à avoir une épaisseur homogène avant traitement. Cette phase est très importante, car un bon réglage ne peut être garanti que s’il y a une recoupe de la couche après traitement. Aucun apport n’est possible dans la phase de réglage. « Une étape clé a été la parfaite humidification du matériau. Pour obtenir une teneur en eau optimale, nous avons pré-humidifié le matériau jusqu’à l’obtention de la teneur optimale en eau et ce préalablement aux opérations de traitement de la couche de forme », explique David Daguzan.
« Une étape clé a été la parfaite humidification du matériau. Pour obtenir une teneur en eau optimale, nous avons pré-humidifié le matériau jusqu’à l’obtention de la teneur optimale en eau et ce préalablement aux opérations de traitement de la couche de forme »
Cette opération a été suivie de l’opération de traitement proprement dit. Elle a été réalisée en deux opérations successives :
• Un épandage du liant hydraulique routier Ligex, à raison de 6% (soit 40 kg/m2) à la surface du matériau, a été réalisé à l’aide d’un épandeur Streumaster SW18 sur nos châssis Renault modifié et adapté à notre métier par le constructeur Français Bulltech,
• Un malaxage et les derniers ajustements en teneur en eau jusqu’à l’obtention de la teneur optimale se font en injection d’eau directement dans la cloche du pulvimixeur, ceci pour ajuster au plus fin et sans gaspillage les teneurs en eau.
• À l’aide d’une niveleuse, le matériau a ensuite été remis en forme.
Trois types de compacteurs se sont chargés du compactage du matériau traité afin d’atteindre l’objectif q3 fixé : à bille lisse, dameur (pour limiter le feuilletage), puis à pneus (pour donner un bel uni). Une niveleuse assistée par GPS effectue le réglage par recoupe de la couche traitée, pour obtenir un résultat au centimètre près. On obtient ainsi un très bon uni et un profil en long très régulier.
Enduit de protection
Un enduit de cure bicouche clouté a ensuite été appliqué pour, d’une part, protéger la couche de forme et assurer une bonne prise hydraulique du mélange et, d’autre part, garantir un bon collage à l’interface entre la couche de forme et la couche de fondation en GB3. À noter que la circulation des véhicules a été neutralisée pendant un délai de vingt-huit jours, pour ne pas rompre la prise hydraulique.
Contrôles
De nombreux contrôles ont été effectués au cours de la réalisation du chantier de terrassements afin de s’assurer l’obtention des caractéristiques mécaniques visées. Des contrôles de portance ont ainsi été réalisés pour la PST inférieure, traitée à la chaux vive permettant de valider la classe d’arase obtenue PF2.
Pour les travaux de la couche de forme traitée au LHR, la validation de la classe de portance a été effectuée par des contrôles de déflexion : c’est le Falling Weight Deflectometer FWD de Rincent Laboratoires qui a été mobilisé dans le cadre du contrôle extérieur. Cette méthode a été préférée aux mesures de portance in situ car mieux adaptée au traitement aux liants hydrauliques routiers.
Pour l’ensemble des couches, la qualité de compactage (q3) a été validée par des essais fréquents de densité en place mesurées à l’aide d’un gamma-densimètre.
Au cours de l’ensemble du chantier, afin de maîtriser notamment la teneur en eau des matériaux, des analyses en laboratoires et des contrôles ont été réalisés quotidiennement.
Le liant hydraulique routier LIGEX
« Le Ligex M4 est un liant à base de clinker. Sa composition permet d’obtenir une cinétique rapide de montée en performance, tout en bénéficiant d’un délai de maniabilité adapté à une mise en œuvre des travaux de traitement des sols en place », précise Bruno Classen, chef de l’agence Routes de Ciments-Calcia. Au total, ce sont 800 t qui ont été livrées sur ce chantier. « Les cadences de livraison ont été variables selon l’avancée des travaux. Certaines cadences journalières ont pu atteindre 150 tonnes », souligne Wilfrid Beck, technico-commercial chez Ciments-Calcia. La logistique a été un élément-clé de la réussite de ce chantier pour Ciments-Calcia : la bonne communication entre les équipes de traitement de GARRAUD TP/ECOSTAB et de Ciments-Calcia a permis une fluidité des livraisons.
Réalisation de la couche de fondation en GB3
La couche de fondation, constituée de 10 cm de grave-bitume GB3, a été réalisée par l’entreprise EUROVIA, à l’aide d’un finisseur et d’un atelier de compactage. L’objectif est d’obtenir une compacité minimale de 92%, conformément aux exigences de la norme NF EN 13 108-1 « enrobés bitumineux » et aux spécifications données dans le catalogue des structures-types de chaussées neuves SETRA-LCPC (1998).
La mise en œuvre de la grave-bitume a été effectuée par bandes de largeur 5,5 m, juxtaposées afin de couvrir la totalité de la surface de l’aire de repos, soit sur 20 000 m2.
Réalisation du revêtement en béton
« Avant le démarrage des travaux, nous avons remis à la DIRA, pour validation, un plan précisant l’organisation de la mise en œuvre des revêtements en béton », précise Luc Le Foll, conducteur de travaux de l’entreprise Eurovia – Cognac TP. Ce plan définit le séquençage de la mise en place du matériau (sens de bétonnage, longueur et largeur des bandes, réalisation des bandes en peigne c’est-à-dire une bande sur deux) et l’emplacement des joints de construction.
« L’objectif, pour nous, est d’assurer une mise en œuvre continue, de maîtriser les délais d’exécution et de minimiser les joints de construction », ajoute Luc Le Foll.
La mise en œuvre du revêtement en béton comprend deux étapes :
• Fabrication et transport du béton ;
• Mise en œuvre du béton.
« L’objectif, pour nous, est d’assurer une mise en œuvre continue, de maîtriser les délais d’exécution et de minimiser les joints de construction »
Fabrication et transport du béton
Le béton a été fabriqué et livré par Lafarge Bétons, à partir de sa centrale BPE de Barbezieux, située à 15 km du chantier. Eurovia et Lafarge Bétons ont établi conjointement, par ajustements successifs, les deux formulations du béton employées sur ce site :
- Formule adaptée pour une mise en œuvre à la machine à coffrages glissants :
« NF EN 206/CN - S2,7 - C35/45 – CEM II/A 42,5 R CP2 - D20 - S1 - XF2 – CL 0,40 ».
- Formule adaptée pour une mise en œuvre manuelle à l’aiguille et à la règle vibrantes :
« NF EN 206/CN - S2,7 - C35/45 – CEM II/A 42,5 R - D20 - S2 - XF2 – CL 0,40 ».
Les deux bétons se distinguent uniquement par leurs classes de consistance (S1 pour le béton destiné à une mise en œuvre à la machine à coffrages glissants et S2 pour le béton destiné à une mise en œuvre manuelle). Ces deux bétons ont deux particularités : leur granulométrie (0/20) et les caractéristiques techniques demandées par le maître d’ouvrage, à savoir une résistance de 2,7 MPa en traction indirecte. « Pour tenir ces exigences, il a fallu nous assurer d’une grande régularité dans la fabrication des bétons à couler. Une fois les essais de convenance terminés et les deux formules définies, nous nous sommes efforcés de tenir cet optimum de production en contrôlant régulièrement la consistance au départ et à l’arrivée sur le chantier », précise Luc Le Foll.
Le béton a été ensuite acheminé depuis la centrale jusqu’au chantier par camions-toupies qui déversent le béton devant la machine à coffrages glissants ou devant la règle vibrante dans les zones où le bétonnage a été réalisé d’une façon manuelle.
Outre le classique autocontrôle, chaque jour Lafarge Bétons réalise 6 éprouvettes de béton qui sont remises à la DIRA, afin de les stocker dans des conditions bien définies de température et d’hygrométrie, dans le but de réaliser d’éventuels essais de contrôle des performances mécaniques du béton.
« Pour tenir ces exigences, il a fallu nous assurer d’une grande régularité dans la fabrication des bétons à couler »
Mise en œuvre du béton
L’exécution du revêtement en béton comprend plusieurs opérations : bétonnage ; talochage ; traitement de surface ; protection et exécution des joints de retrait.
• Le bétonnage
Après nettoyage de la surface de la couche de grave bitume dans le but d’assurer l’obtention d’une interface semi-collée entre le revêtement en béton et la fondation en grave bitume, le bétonnage a été conduit principalement de façon mécanisée. En effet, sur la majeure partie de l’aire de repos, une machine à coffrages glissants a été utilisée. Les endroits les moins accessibles (zones de formes complexes ; zones d’une largeur inadaptée pour le passage de la machine), qui représentaient moins de 5 % de la surface, ont été traités de façon manuelle.
Pour le bétonnage mécanisé, le béton est déversé directement par le camion-toupie à l’avant de la machine à coffrages glissants (slip-form). La double vis de répartition à l’avant de la machine à coffrages glissants se charge de la répartition du béton avant son coffrage et sa vibration, réalisant ainsi une dalle continue de 4,5 m de large, d’épaisseur bien définie (18 cm pour la zone réservée au poids lourds et 14 cm pour la zone réservée aux véhicules légers et pour les cheminements piétons) et de plusieurs dizaines de mètres de long.
Un palpeur et un fil sur potence assurent le nivellement et le guidage de la machine. Gage de qualité, ce type de machine nécessite l’emploi d’un béton très ferme (béton de consistance S1 avec un slump compris entre 2 et 3 cm).
Pour le bétonnage manuel, le béton, de formulation spécifique (consistance S2) est déversé entre coffrages fixes et tiré manuellement à l’aiguille et à la poutre vibrantes.
« Le bétonnage a été effectué en grande partie à l’aide d’une machine à coffrages glissants guidée sur fils (deux fils, un fil de chaque côté) », ajoute Luc Le Foll.
Pour la couche de roulement en BC5g, entre 200 m3 et 250 m3 de béton sont mis en œuvre quotidiennement, en fonction notamment de la météo. Avancement : environ 300 ml par jour à la machine à coffrages glissants et 50 ml à la poutre vibrante.
« Nous appliquons la technique du clavage, qui consiste à couler une bande sur deux, puis à revenir pour les bandes intermédiaires », explique Luc Le Foll.
Un mode opératoire qui évite les temps morts : « Si nous progressions d’une bande adjacente à l’autre, nous devrions attendre que le béton soit suffisamment ferme pour permettre à la machine d’y prendre appui », ajoute Luc Le Foll.
L’exécution de ce béton fait appel à un mode opératoire particulier. La machine réalise lors d’une première phase les bandes impaires, puis vient combler les bandes intermédiaires.
Pour réaliser les bandes primaires, on équipe la machine à coffrages glissants d’un système d’insertion automatique des goujons à mi-hauteur sur les deux flancs du revêtement béton dans le but de solidariser les bandes paires et impaires, et garantir ainsi la planéité de l’ensemble de la plate-forme.
Pour chaque zone, la surface du béton a été profilée pour qu’elle ait une pente unique à 2,5 % dans le sens transversal. Dans le sens longitudinal, la pente varie selon les zones mais reste assez faible dans l’ensemble (0,5 % au maximum). Les eaux de ruissellement sont recueillies en bord de chaussée dans des caniveaux en béton, conduisant l’eau vers des regards à grille disposés dans des endroits bien précis.
• Zone de circulation et de stationnement des Poids lourds
La dalle est réalisée à l’aide d’une machine à coffrage glissant travaillant en largeur de 4,5 m. Pour cette zone, le revêtement en béton est d’épaisseur 18 cm et il est non armé et à joints de retrait transversaux goujonnés. La surface du revêtement des plateformes des parkings présente un dévers de 2,5 % vers les caniveaux réalisés en bordure de la zone.
- Positionnement des goujons
Le bétonnage a été réalisé par bandes de largeur 4,5 m. Le béton est mis en place alors que des paniers de goujons (en fer lisse plastifié ; diamètre 25 mm ; longueur 45 cm ; espacés de 30 cm) ont été préalablement installés avec un espacement de 4,5 m, de telle manière que les goujons soient placés à mi-hauteur de la dalle et se trouvent ainsi à cheval sur les futurs joints, qui sont ensuite réalisés par sciage. Ces goujons assurent le transfert de charge au niveau des joints de retrait transversaux et maintiennent ainsi les dalles solidaires dans le plan vertical, tout en leur conservant un libre mouvement dans le plan horizontal.
Ces paniers maintiennent les goujons en position (mi-hauteur de la dalle : 9 cm) pendant le bétonnage. Leur conception doit être telle qu’elle ne crée pas de liaison mécanique entre les dalles au niveau des joints. Il s’agit généralement d’aciers Ø 6, sur lesquels les goujons sont attachés par ligature. Ces paniers stockés sur le chantier, seront positionnés avec un espacement bien défini de 4,5 m et fixés sur la fondation en grave bitume au droit des joints de retrait, repérés par une marque en dehors de l’emprise de la chaussée, juste à l’avant de la machine. « Et ce n’est pas moins de 1250 paniers porte-goujons, soit un total de 25 000 goujons qui ont été ainsi utilisés sur ce chantier », précise Luc Le Foll.
- Mise en œuvre de la couche de roulement en béton BC5g
Le béton est également mis en œuvre par bande à la machine à coffrages glissants, dans les lignes droites, et à la poutre vibrante, dans les courbes. Au moment où la machine arrive à l’emplacement d’un joint, on fixe les paniers de goujons sur la fondation en grave bitume GB3. Il y a lieu ensuite de prendre des précautions afin de ne pas les écraser lors du déchargement du béton. Le déversement direct sur les paniers est à proscrire.
Déversé à l’avant d’une machine à coffrage glissant réglée à 4,5 m de large, le béton est mis en forme et vibré en une seule opération sur une épaisseur de 18 cm. L’aire de repos est réalisée en plusieurs bandes successives de 4,5 m de large, recoupées tous les 4,5 m dans le sens transversal. Les bandes de béton se raccordent entre elles au moyen d’un joint longitudinal équipé de goujons de diamètre 25 mm et espacés de 30 cm.
« À chaque extrémité de la bande ainsi bétonnée, a été interposée une épaisseur de polystyrène jouant le rôle de joint de dilatation », commente Luc Le Foll.
• Zone de circulation et de stationnement des véhicules légers, et zones de circulation piétonne
La dalle est réalisée à l’aide d’une machine à coffrage glissant travaillant en largeur de 4,5 m. Pour cette zone, le revêtement en béton est d’épaisseur 14 cm et il est non armé et à joints de retrait transversaux non goujonnés. Le profil ondulé des joues de la machine permet d’obtenir un transfert de charge entre les bandes de béton.
• Le talochage
Immédiatement après le bétonnage, les opérations manuelles de talochage et de lissage ont été réalisées par des équipes de maçons experts pour conférer au revêtement en béton un état de surface plan et d’aspect fermé (exempt de cavités ou de trous).
• Le traitement de surface
Destinée à donner au revêtement en béton les caractéristiques d’adhérence exigées par le cahier des charges, le traitement de surface a été réalisé par balayage fin. « Le niveau d’adhérence souhaité a été obtenu grâce à un balayage fin transversal réalisé manuellement », confirme Gilles Petit.
• La cure du béton
L’opération de balayage a été immédiatement suivie de la protection du béton, réalisée en pulvérisant manuellement à la surface du revêtement un produit de cure, à raison d’un minimum de 200 g/m2.
• Des joints de retrait transversaux et de construction longitudinaux sciés espacés de 4,5 m et scellés
Six à huit heures après le coulage du béton, l’entreprise SOCOTRAS vient réaliser les joints dans le revêtement en béton.
Compte tenu de la largeur limitée des bandes de béton (4,5 m), seulement des joints de retrait-flexion transversaux ont été prévus dans le plan de calepinage. Ces derniers ont pour but de localiser la fissuration de retrait du béton de manière précise et déterminée à l’avance et de réduire ainsi les sollicitations dues au retrait et au gradient thermique. « Ces joints sont réalisés en créant dans le revêtement une saignée ou une entaille qui matérialise un plan de faiblesse, selon lequel le béton est amené à se fissurer sous l’action des contraintes de traction par flexion. Cette entaille doit avoir une profondeur comprise entre un quart et un tiers de l’épaisseur du revêtement et une largeur (souffle du joint) comprise entre 3 et 5 mm. Les joints de retrait-flexion transversaux doivent être réalisés à intervalles réguliers. Leur espacement est déterminé en fonction de l’épaisseur du revêtement (au maximum 25 fois l’épaisseur), soit 4,5 m. Les joints de retrait transversaux des bandes adjacentes doivent être alignés », précise Edwin Constans, directeur général de Socotras.
Socotras a procédé de la manière suivante :
• Repérage des joints par le géomètre de l’entreprise de bétonnage.
• Traçage des joints à la peinture indélébile.
• En fonction des paramètres liés à la météo, à la nature des agrégats, à la nature et au dosage du ciment et au mode de bétonnage, une amorce de fissuration dans le béton frais est réalisée dans des délais appropriés après le bétonnage (compris entre six et trente-six heures), sur une profondeur de l’ordre de 5 cm.
• Au bout d’un délai fixé par Socotras (de plusieurs jours), l’élargissement aux dimensions de 10 x 35 mm x mm par sciage de l’amorce de fissuration et du joint de construction est réalisé.
• Chanfreinage à 45 ° et 5 mm environ des lèvres supérieures de la réserve.
• Enlèvement des laitances de sciage par aspiration ou lavage.
• Éventuellement, séchage des lèvres du joint à la lance thermique afin d’éliminer les traces d’humidité.
• Mise en place d’un fond de joint qui doit permettre le réglage de la hauteur du produit de garnissage.
• Si le produit de garnissage le nécessite, application par pulvérisation d’un primaire d’accrochage sur les lèvres et le fond de joint.
• Préparation et application du produit de garnissage.
• Plus de 100 m3 de béton coulés chaque jour
Pour Lafarge, fournisseur de bétons prêts à l’emploi intervenant sur le site, cela n’a pas été une mince affaire. Ce que confirme Harold Gicquel, responsable commercial de Lafarge Bétons : « Il nous a fallu tenir des cadences très importantes, l’entreprise mobilisant au total deux centrales à béton (une pour la production et l’autre de secours) ! La machine d’Eurovia avançait vite, vidant un camion-toupie en six ou sept minutes. Nous avons donc eu entre 5 et 6 camions-toupies en rotation en permanence pour ne pas provoquer de rupture d’approvisionnement de la machine à coffrages glissants et parvenir à couler jusqu’à 250 m3 par jour ». La coordination entre Eurovia et Lafarge a été ajustée au plus fin pour produire, sans rupture, 3 500 m3 de béton C35/45 XF2. Outre ces cadences, le suivi de la qualité du béton prêt à l’emploi a été aussi mené avec soin : « On nous demandait une résistance au fendage de 2,7 MPa au minimum et nous avons dû nous caler correctement pour obtenir la bonne plasticité et pour que le béton se mette en place facilement. C’est un chantier imposant : il est rare, en effet, de réaliser des voies en béton de cette ampleur », précise Dorian Luzineau, responsable qualité secteur de Lafarge Bétons.
Un chantier partagé
L’originalité du chantier, outre son ampleur, réside dans la conduite simultanée de différents types de travaux sur l’aire de repos (le bâtiment des sanitaires et le local technique des contrôleurs des transports ; le mobilier ; l’assainissement ; la signalisation ; les bordures ; les caniveaux ; l’éclairage, etc.). « La coexistence de plusieurs intervenants induit des contraintes inédites pour l’entreprise », résume Gilles Petit, en évoquant des difficultés d’interface. « Concrètement, nous devons attendre que le coordinateur OPC [ordonnancement pilotage coordination] nous indique quelle zone il libère, et pendant combien de temps, pour nous permettre d’intervenir, ce qui nous oblige à fragmenter les travaux. Par exemple, une zone que nous aurions traitée d’un seul tenant sera réalisée en une dizaine d’opérations », ajoute Luc Le Foll.
Pour Eurovia, ce chantier vient s’ajouter à une longue liste de références en matière de plate-forme en béton. « Nous aimerions aussi favoriser la percée de techniques innovantes, comme la chaussée composite, une solution mature, parfaitement au point et qui est retenue dans le cadre de la norme de dimensionnement des chaussées NF P 98 086 », conclut Luc Le Foll.
Bilan
« La crise sanitaire a tout compliqué. Il a fallu adopter des mesures sanitaires strictes qui ont entraîné des modifications dans l’organisation du chantier. Malgré toutes ces difficultés, le chantier a été achevé dans les délais et l’aire de repos a été mise en service le 30 août 2022 », précise Giles Petit.
« La cadence a été soutenue à certaines périodes, sachant que le rendement d’un chantier routier en béton est de l’ordre de 1 500 m2 par jour, avec des performances atteignant parfois les 2 500 m2 par jour », conclut Luc Le Foll.
La DIRA a utilisé le béton pour la réalisation des revêtements de l’aire de repos de la Grolle. Compte tenu des risques accrus d’inondations et d’épisodes caniculaires pour cause de réchauffement climatique, contre lesquels les chaussées bitumineuses sont moins résistantes, ce choix s’avère pertinent sur le plan technique et économique, et particulièrement judicieux du point de vue environnemental.
Principaux intervenants
Maîtrise d’ouvrage
DREAL Nouvelle-Aquitaine
Maîtrise d’œuvre
DIR Atlantique
Entreprises
• Mandataire, chaussée grave-bitume/assainissement/VRD : Eurovia Poitou-Charentes-Limousin (agence d’Angoulême)
• Terrassement : Garraud TP – sous-traitant Traitement des sols : Ecostab
• Chaussée en dalles de béton : Eurovia grands projets France (agence Cognac TP)
• Exécution des joints : Socotras
Fournisseur de la grave-bitume
Eurovia (SMEC)
Fournisseur du béton
Lafarge Bétons
Fournisseur du liant hydraulique routier Ligex
Ciments-Calcia
Fournisseur de la chaux vive
Lhoist
COMMENTAIRES
LAISSER UN COMMENTAIRE